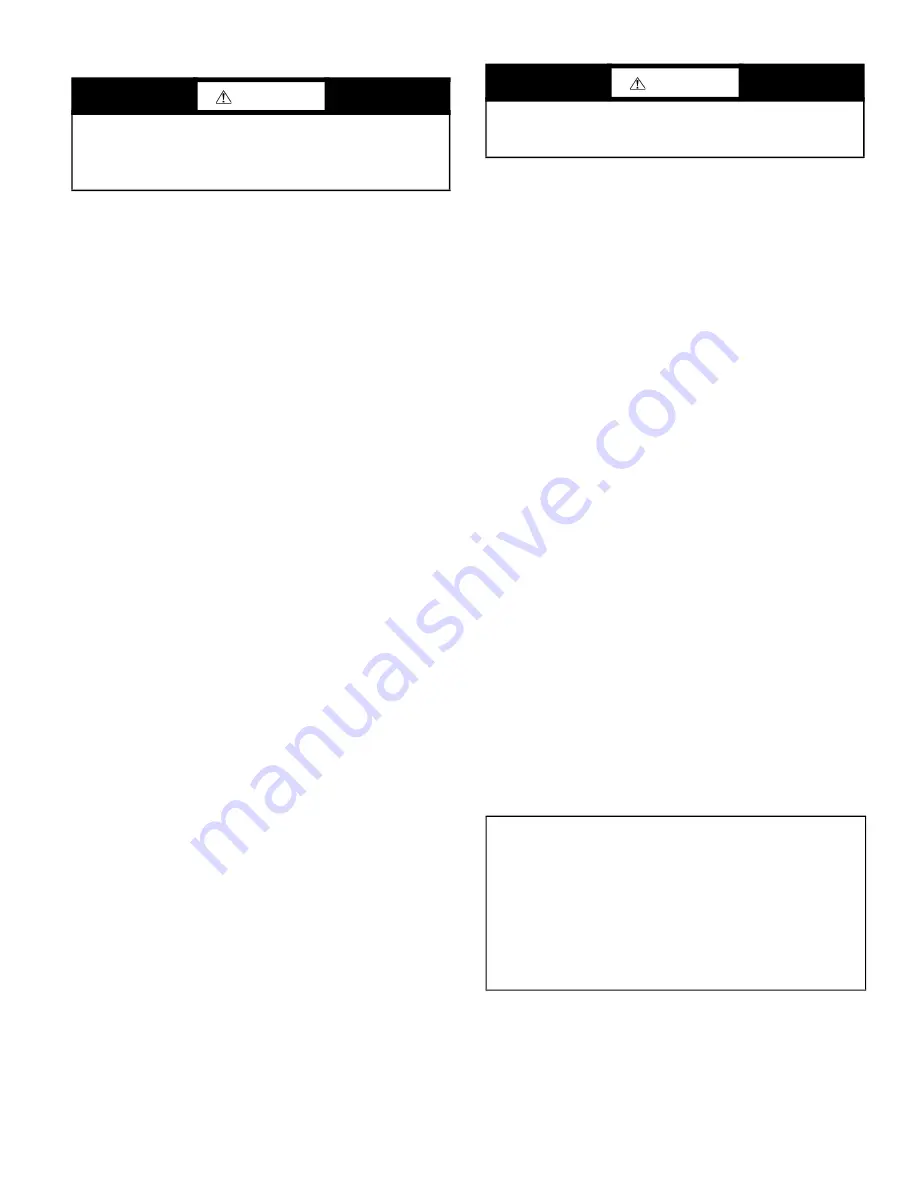
203
SERVICE
General
1. Review Safety Considerations at beginning of these in
-
structions. Good safety habits are important tools when
performing service procedures.
2. To make speed measurements, use a strobe-style tachom
-
eter or calculate per Step 7 of Start-Up, Checklist for Air
-
foil and Forward-Curved Fans (page 198).
Single Point Power Enclosure
At least once a year at start of operating season or whenever unit is
serviced, check field and factory made electrical connections for
condition of wiring insulation and tightness of connections.
Single Point Power Enclosure
At least once a year at start of operating season or whenever unit is
serviced, check field and factory made electrical connections for
condition of wiring insulation and tightness of connections.
Electric Heaters
At least once a year at start of operating season or whenever unit is
serviced, check field and factory-made electrical connections for
tightness. Also periodically clean filters, fan, airways, ductwork,
grilles, and registers as required. Differential air pressure switch is
factory set to open at 0.07 in. wg, close at 0.05 in. wg and requires
no adjustment.
Refer to the Troubleshooting section for more information. Heater
electrical data is shown in Table 40.
Gas-Fired Furnaces (Duct and Rack System)
Follow these procedures for inspection and operation check.
INSPECTION
1. The duct furnace or furnace module should be inspected
annually by a qualified service agency. The condition of
the burners, heat exchanger, draft inducer, vent system,
operating controls and wiring should be determined.
Check for obvious signs of deterioration, accumulation of
dirt and debris, and heat or water related damage. Any
damaged or deteriorated parts should be replaced before
the unit is put back into service.
2. Label all wires prior to disconnection when servicing unit,
Wiring errors can cause improper or dangerous operation.
Verify proper operation after servicing.
3. Inspect burners, heat exchanger, induced draft fan and vent
ducts and clean as necessary.
4. Check the heat exchanger for cracks. If any are present, re
-
place heat exchanger before putting unit back into service.
5. Check the attachment points of the duct furnace to the cabi
-
net to verify that they are air-tight. For a rack system module,
check the attachment points to the cabinet or ducts to verify
that they are air-tight.
6. Check the automatic gas valve to ensure that the gas valve
seat is not leaking.
7. Check wiring connections to be sure they are secure, and in
-
spect wiring for any deterioration.
OPERATION CHECK
1. Turn on power to the unit and set thermostat or heat controller
to call for heat, allowing duct furnace or heater assembly
module to operate.
2. Check for proper start-up and ignition of the single unit or
each furnace in the heater assembly module. See the
section Gas-Fired Furnaces (Duct and Rack Systems) on
page 201.
3. Check the appearance of the burner flame. See Fig. 180 on
page 202.
4. For single units, be sure circulating air fan is operating and
verify proper airflow through duct furnace.
5. Return thermostat or heat controller to normal setting.
Fan Motor Replacement
1. Shut off motor power.
2. Disconnect and tag power wires at motor terminals.
3. Loosen motor brace-to-mounting-rail attaching bolts. Loosen
belt tensioning bolts to adjust the motor position so V-belts
can be removed without stretching over grooves.
4. Mark belt as to position. Remove and set aside belts.
5. Remove motor to motor bracket holddown bolts.
6. Remove motor pulley and set aside.
7. Remove motor. It may be necessary to remove the end panel
to remove larger motors for some unit sizes.
8. Install new motor. Reassemble by reversing Steps 3-7. Be
sure to reinstall multiple belts in their original positions. Use a
complete new set if required. Do not stretch belts over
sheaves. Review the sections on motor and sheave installa
-
tion, sheave alignment, and belt tensioning starting on
page 110.
9. Reconnect motor leads, remove tags, and restore power.
Check fan for proper rotation as described in Start-Up,
Checklist.
Energy Recovery Ventilation
Routine maintenance of the energy recovery cassettes includes
inspection and cleaning. On occasion, a part may need to be
completely replaced.
CLEANING
Periodic cleaning of the energy recovery wheel will depend on
operating schedule, climate and contaminants in the indoor air
exhausted and the outdoor air supplied to the building.
The wheel is “self-cleaning” with respect to dry particles due
to its laminar flow characteristics. Smaller particles pass
through; larger particles land on the surface and are blown
CAUTION
Electric shock hazard. Disconnect power before entering or
servicing.
More than one disconnect switch may be required to de-ener
-
gize the equipment.
CAUTION
If any of the original wiring needs to be replaced, it must be
replaced with wiring materials suitable for 221°F (105°C).
Unsuitable wiring materials may cause equipment damage.
IMPORTANT: This unit contains an energy recovery wheel
heat transfer device. Proper service and maintenance must be
conducted as outlined below, or loss of heat transfer and overall
system performance will occur.
1. Remove and clean or replace filters in adjoining section to
the ERV wheel every 6 months or sooner, as required.
2. Remove and wash ERV wheel (or individual segments, if
so equipped) every 6 months, or every 3 months maxi
-
mum for smoky or polluted environments. See instruc
-
tions for removal and cleaning details.