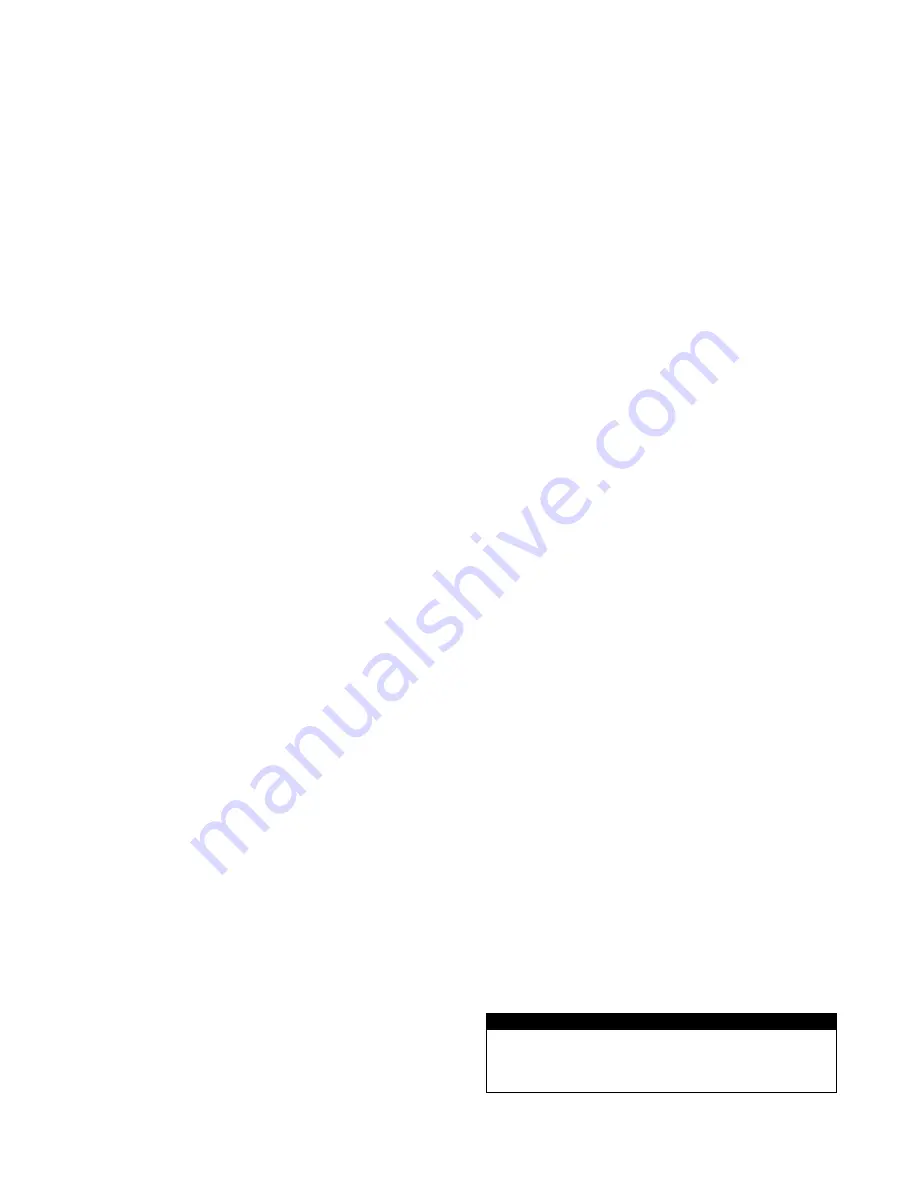
34
The condensate will typically have a pH ranging from 4.0 to
5.0 as it is discharged from the condensate drain of the
appliance.
The condensate collection box inside each Valiant FT
Series II boiler where the condensate is collected is
constructed of a non-corrosive material.
All materials external to the appliance in contact with the
condensate must be corrosion resistant.
Condensate must be able to flow freely from the appliance.
All condensate flow is accomplished by gravity requiring a
minimum downward slope of 1/4” per foot (21mm/m) to
ensure proper flow to a suitable drain.
All condensate piping and connections must be easily
accessible for routine maintenance and inspection.
Use solid piping when running condensate line across the
floor.
Check neutralized pH level regularly or as required by local
jurisdiction. Replace neutralizer medium as required.
There are several factors affecting amount of condensation
created by the appliance, however for rough approximation
use.
Condensation Volume, US Gallon/Hr = Input, MBH/1000 x
5.0
Many jurisdictions will require the acidic condensate to be
neutralized before it can be placed in a drain system.
8.4
IGNITER AND FLAME SENSOR ELECTRODES
The direct spark igniter is to be checked at every service
interval. Clean the direct spark igniter as required to
maintain peak ignition efficiency.
1. Turn off main electrical power to the appliance.
2. Turn off main manual gas shutoff to the appliance.
3. Locate the direct spark igniter and flame sensor.
4. Disconnect the power lead to the direct spark
igniter and flame sensor
5. Loosen and remove the two (2) torx screws that
hold the igniter and flame sensor to the heat
exchanger flange.
6. Pull the igniter horizontally out of the heat
exchanger flange. Use care, do not hit or break the
igniter leads.
7. Remove any debris that has accumulated on the
electrodes using steel wool. If the electrodes
cannot be cleaned to their original appearance,
replacements are needed. Do not use sandpaper
since this will contaminate the surface.
8. Check that the igniter and flame sensor gaskets
are still in good condition (no tears or seams). If
the gaskets are in good condition the electrodes
can be re-installed back to the heat exchanger
flange.
9.
Check that the igniter gap is 13/64”.
10. Re-install and tighten the mounting screws.
CHECK IGNITER GROUND WIRING
1. Inspect boiler ground wire from the heat
exchanger flange to ground on boiler. Check boiler
ground wire continuity.
2. Verify that all wiring is in good condition and is
securely anchored
8.5
BURNER MAINTENANCE
The burner should be removed for inspection and cleaning
on an annual basis. An appliance installed in a dust or dirt
contaminated environment will require inspection and
cleaning on a more frequent schedule. The fan assisted
combustion process may force airborne dust and dirt
contaminants, contained in the combustion air, into the
burner. With sustained operation, non-combustible
contaminants may reduce burner port area, reduce burner
input or cause non-warrantable damage to the burner.
Never operate this appliance during construction.
Airborne contaminants such as dust, dirt, concrete dust or
dry wall dust can be drawn into the burner with the
combustion air and block the burner port area.
8.5.1 Burner Removal and Cleaning
Access to the burner will require the following steps:
1. Turn off main electrical power to the appliance.
2. Turn off main manual gas shutoff to the appliance
3. Disconnect the gas train to the fan inlet.
4. Disconnect the fan motor power wires at the
harness.
5. Remove the screws from the burner flange and
then remove the burner flange to gain access to
the burner.
6. The burner can now be pulled vertically out of the
heat exchanger.
7. Use care to prevent damage to the knitted metal
fiber of the burner surface.
8. Wash the burner with water, such as a garden
hose. Never wipe or brush the surface of the
burner.
9. For optimal results immerse the burner port area
in a solution of dishwashing detergent and hot
water. DO NOT use chlorine-based solvents or
cleaning agents on the burner. Allow the burner to
remain in the solution for a short period of time to
remove, dust, dirt and oil or grease laden
contaminants.
10. Rinse the burner thoroughly with clean water to
remove any residue from the detergent cleaner.
11. The burner should be air dried after removal from
the cleaning solution and rinsing.
12. Check all gaskets and replace as necessary.
Gaskets affected by heat will not reseal properly
and must be replaced.
13. Replace the burner in the reverse order that it was
removed.
NOTE
When the combustion air fan is removed for any reason,
the inlet to the burner must be covered to prevent foreign
objects from falling into the burner. Always look inside
the burner to check for dents. Do not place a burner back
Содержание Valiant-FT II Series
Страница 2: ...99 0419 Rev 00...
Страница 40: ...36 PART 9 PIPING DIAGRAMS Figure 40 Single Boiler Hydronic Heating Zoned Piping...
Страница 41: ...37 Figure 41 Multiple Boiler Hydronic Heating Zoned Piping...
Страница 42: ...38 Figure 42 Single Boiler with DHW Tank Hydronic Heating Zoned Piping...
Страница 43: ...39 PART 10 PARTS LIST...
Страница 44: ...40...
Страница 45: ...41...
Страница 46: ...42...
Страница 47: ...43...
Страница 48: ...44...
Страница 49: ...45...
Страница 50: ...46...
Страница 51: ...47...
Страница 52: ...48...
Страница 53: ...49...
Страница 54: ...50...
Страница 60: ...56 PART 11 TUBING DIAGRAM...
Страница 61: ...57 PART 12 WIRING DIAGRAM...
Страница 62: ...58...
Страница 63: ...59...