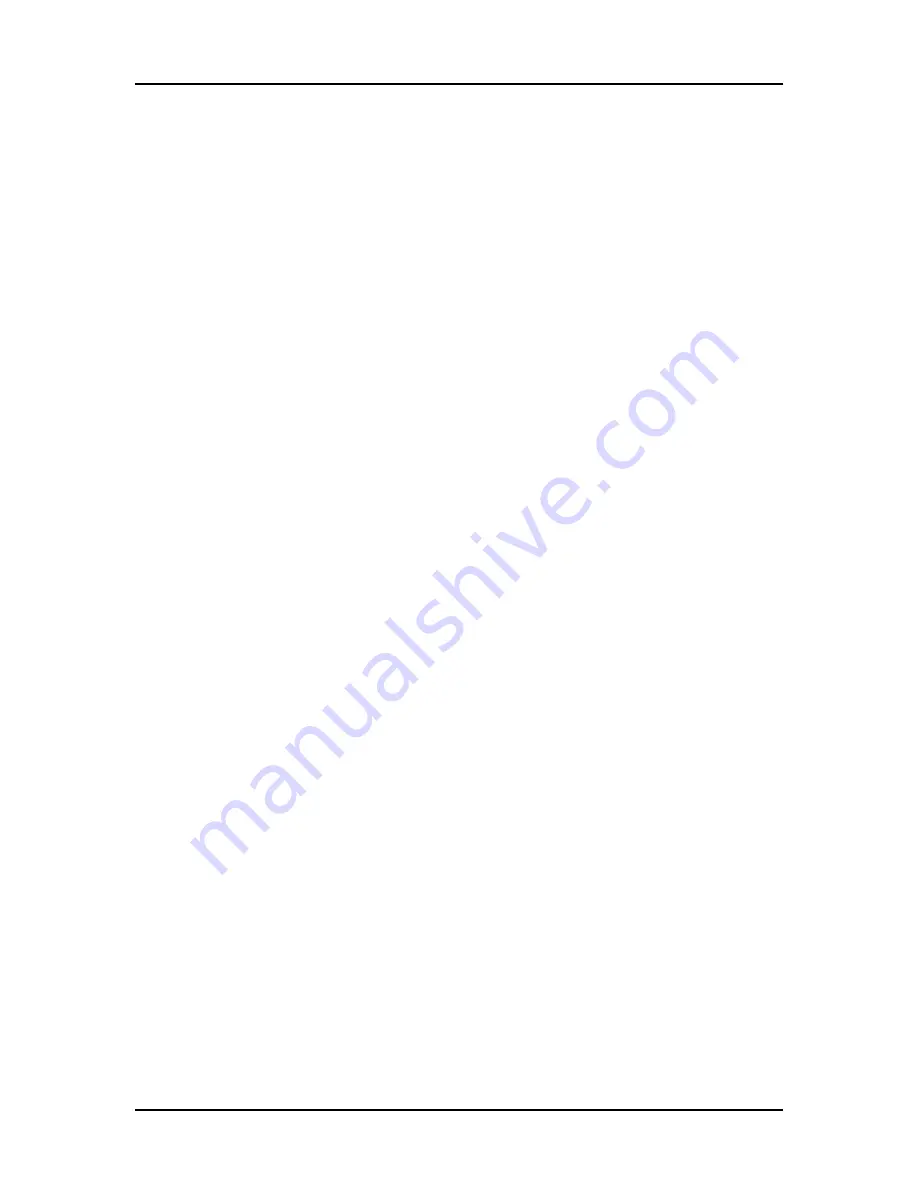
Robot Software Terminology
22
P/N 113564 Rev. 2
Twister II Robot User’s Manual
Caliper Life Sciences, Inc.
Material Layout using iLink PRO Storage
Software
The iLink PRO Storage software for the Twister II racks is used with
the iLink PRO automation control software to set up the initial
material layout. The initial material layout shows where to place the
materials in the racks before starting to run an iLink PRO method.
The iLink PRO Storage software enables you to place multiple
material in the same rack, as long as all the materials are the same
type, and each has a unique name. See
for information on creating the initial material layout.
Restacking
The Caliper Life Sciences Robot software, the Stack Storage
software, the iLink PRO Storage software, and the Caliper
automation control software can be used to automatically restack
the materials from the destination racks back into the original
source racks. This enables you to execute methods in the
automation control software that use the same starting rack
positions for materials. Restacking with CLARA is explained in the
CLARA User’s Manual
. Restacking with iLink PRO is explained in
the
iLink PRO User’s Manual
.
Lids
The Robot software, Stack Storage software, iLink PRO Storage
software, and Caliper automation control software are designed to
accommodate materials with lids. To use materials with lids, the
CLARA or iLink PRO method must be created properly. See the
CLARA User’s Manual
or the
iLink PRO User’s Manual
for
instructions on processing materials with lids.
Remote and Standalone Modes
The Robot software can operate in either Standalone mode or
Remote mode.
•
The Robot software is in
Standalone mode
if it is opened
manually from the Start menu or the desktop.
•
The Robot software is in
Remote mode
if it is opened by
automation control software such as CLARA.
The Robot software must be in Remote mode when the robot is
controlled by the automation control software.