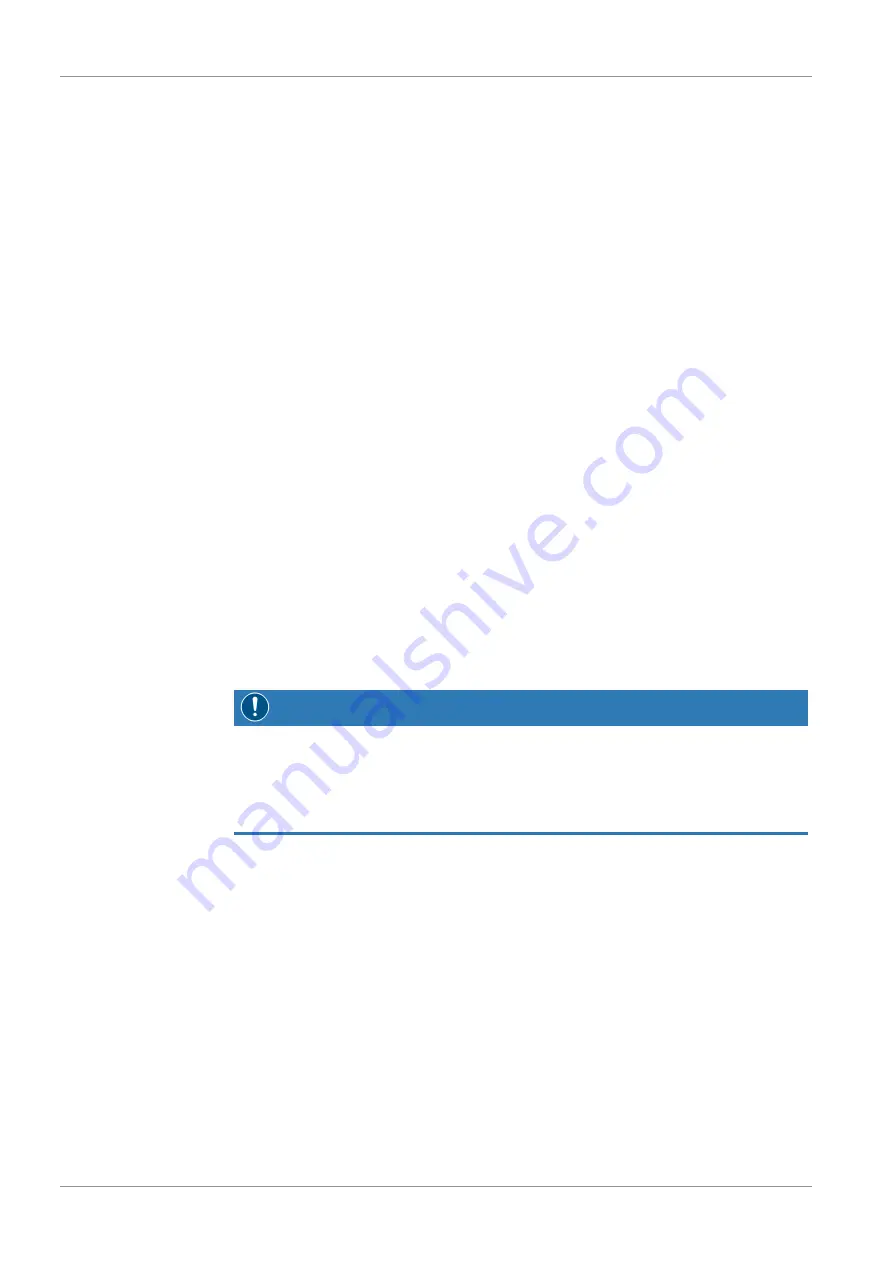
6 | Commissioning
18 / 32
0870237638_LR0110-0580A_-_IM_en
• Make sure that the installation conditions (see
) are
met.
Before operating the machine:
• Make sure that the operating liquid level is at the machine shaft centre.
• Check the operation of all automatic valves before start up
– Machines with gland packing for shaft sealing: loosen the packing gland plate and
apply a few drops of oil to the packing for lubricating purpose.
– Ensure external shaft sealing liquid is available to packing gland or double cartridge
mechanical seal before switching on the machine. Supply pressure for packing gland
0.1 to 0.3 bar(g) with flow rate to suitably lubricate the packing.
– For mechanical seal supply pressure and flow rate, see manufacturers instructions for
the contract.
• Switch on the machine.
• Make sure that the maximum permissible number of starts does not exceed the re-
commendation from the motor manufacturer.
After a few seconds of operation:
• Turn on/activate the operating liquid system device.
• Make sure that the operating conditions comply with the
.
As soon as the machine is operated under normal operating conditions:
• Measure the motor current and record it as reference for future maintenance and
troubleshooting work.
– Machines with gland packing for shaft sealing require the gland to be adjusted dur-
ing operation. Uniformly tighten the gland plate so that the liquid leakage along the
shaft from the packing is 20 to 40 drips per minute.
6.1 Preventing Cavitation
NOTICE
Cavitation.
Risk of damage to the machine!
If you hear crackling noise:
• Control the pressure.
At very low pressures and sufficiently high temperatures the operating liquid can locally
transfer into the vapour phase, creating bubbles within the operating liquid. As the pres-
sure rises towards the outlet slot the bubbles collapse. This process is called cavitation.
In case of bubbles that have been located on surfaces the operating liquid cannot intrude
the cavity left by the bubble equally from all directions. Instead the inflowing liquid hits
the surface with high speed. This causes erosion, which can destroy the machine rapidly.
The formation of bubbles also deteriorates the pump performance. Cavitation is clearly
audible by its crackling noise.
The working pressure of the vacuum pump shall therefore be sufficiently above the va-
pour pressure of the operating liquid. In particular the pressure control in the vacuum
system must by no means be achieved by throttling or even closing of the suction line!
The vapour pressure of the operating liquid and consequently the ultimate pressure can
be reduced by cooling. However, this increases the cooling water flow considerably. In
most cases the low ultimate pressure is not required and cavitation shall be avoided by
means of vacuum limitation rather than cooling.