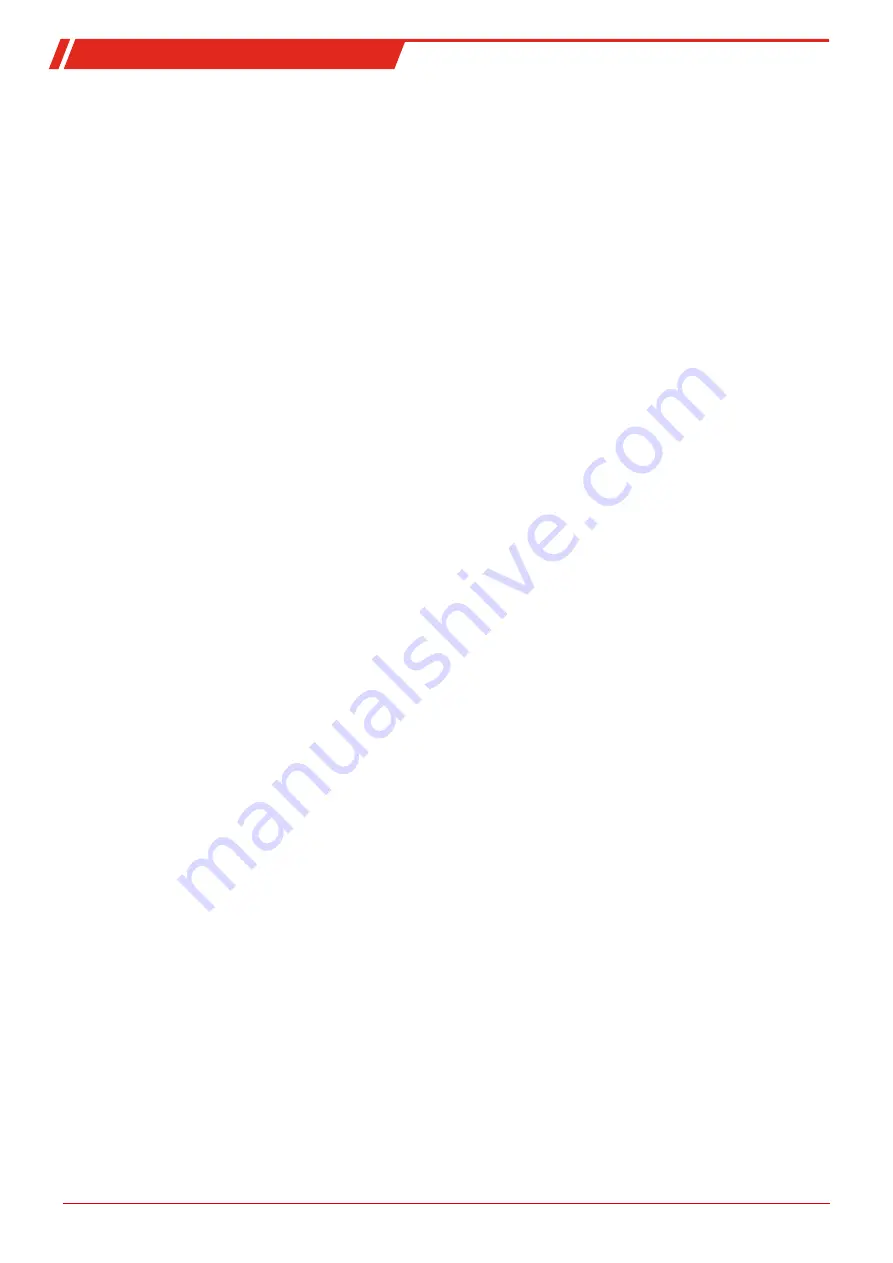
SCS 104
1 Introduction
1.1 Intended Use
The SCS 104 is a gas sample conditioning system. The specifications and their limits given in the appendices are to be main-
tained during installation. The device is not to be used in hazardous areas.
1.2 System Description
Please consult the illustrations and the legend at the end of the operating manual. The components are numbered. The num-
bers are referenced in the text.
1.2.1 Sample conditioning section
The sample gas is pulled in at the sample inlet (1) and through the cooler (2) by the sample pump (6). The cooler (2) operates at
approximately 5 °C (41 °F). The moisture in the sample gas drops out inside the heat exchanger (integral to the cooler) and is de-
livered to the condensate outlet (10) by the condensate pump (3). The condensate pump is often referred to as a peristaltic
pump.
The heat exchanger temperature is shown in the display (30). In the event of a cooler (2) overload and temperature increase of
3 K the sample pump (6) will turn off to avoid downstream moisture damage, and the temperature alarm LED (25) will turn red.
Additionally, a highly sensitive moisture sensor (4) is located downstream from the cooler (2) and before the filter (5). If the mois-
ture sensor (4) detects even the slightest amount of moisture in the sample gas stream, the pump will turn off, and the moisture
alarm (26) will illuminate and the display shows “h20.1”.
Downstream from the moisture sensor (4) the sample gas passes through the filter (5) to remove particulates. The filter element
is visible and accessible at the front panel.
From the outlet of the filter the sample gas is directed to a manual three way valve (7) located on the front panel that allows
either sample gas or calibration gas to enter the inlet of the sample pump (6). The manual valve provides calibration gas directly
to the analyzers, bypassing the probe when in the calibration position.
The sample pump output passes through an adjustable flowmeter with needle valve (8a) to the analyzer(s). The portion of the
sample gas or calibration gas not required by the analyzer(s) flows through a second flowmeter without needle valve (8b). The
amount of sample gas being used by the analyzer(s) is the difference between the two flowmeters. Both flowmeters are visible
and accessible from the front panel. If flow decreases the set limit at flowmeter (8a), the flow alarm LED (27) on the front panel
will turn red.
Condensate pump (3) and gas pump (6) are redundant. Switches (3c and 6c) on relay board RB0291 (23) can be used to change
the active pumps.
Whenever the SCS is powered up the sample conditioning system is operating.
1.2.2 Calibration gas section
Up to 6 calibration gases and 1 zero gas (span 1 – span 6 + zero gas) can be connected to the bulkhead fittings (11a..g + zero gas)
on the rear panel of the SCS. The flow of each calibration gas is controlled by an independent solenoid valve (12a..g) into a com-
mon, adjustable flowmeter with needle valve (13) located on the front panel. From the flowmeter (13) the selected calibration gas
flows to the span outlet bulkhead fitting (14) located on the rear panel and to the manual three way valve (7). A specific calibra-
tion gas is selected using the mode switch (28) and indicated by the system mode LEDs (29), all located on the front panel. Calib-
ration gases can also be controlled by an external controller when the mode switch (28) is in the sample (external control) posi-
tion.
1.2.3 Blowback air section
Instrument air for blowback is connected to the inlet bulkhead fitting (15) on the rear panel. The blowback air pressure is adjus-
ted with a regulator (16), displayed on a pressure gauge (19) and controlled by a solenoid valve (17). The blowback air passes
through the outlet bulkhead fitting (18) located on the rear panel. Operation of the blowback solenoid is selected with the mode
switch (28) and indicated by a system mode LED on the front panel. Blowback air can also be controlled by an external controller
(40) when the mode switch (28) is in the sample (external control) position.
3
Bühler Technologies GmbH
BECS0031 ◦ 02/2020
Содержание SCS 104
Страница 30: ...SCS 104 9 3 Drawing 1 Flow chart 28 Bühler Technologies GmbH BECS0031 02 2020 ...
Страница 32: ...SCS 104 9 5 Drawing 3 Front view 9 6 Drawing 4 Back view 30 Bühler Technologies GmbH BECS0031 02 2020 ...
Страница 34: ......
Страница 71: ......
Страница 72: ......
Страница 73: ......