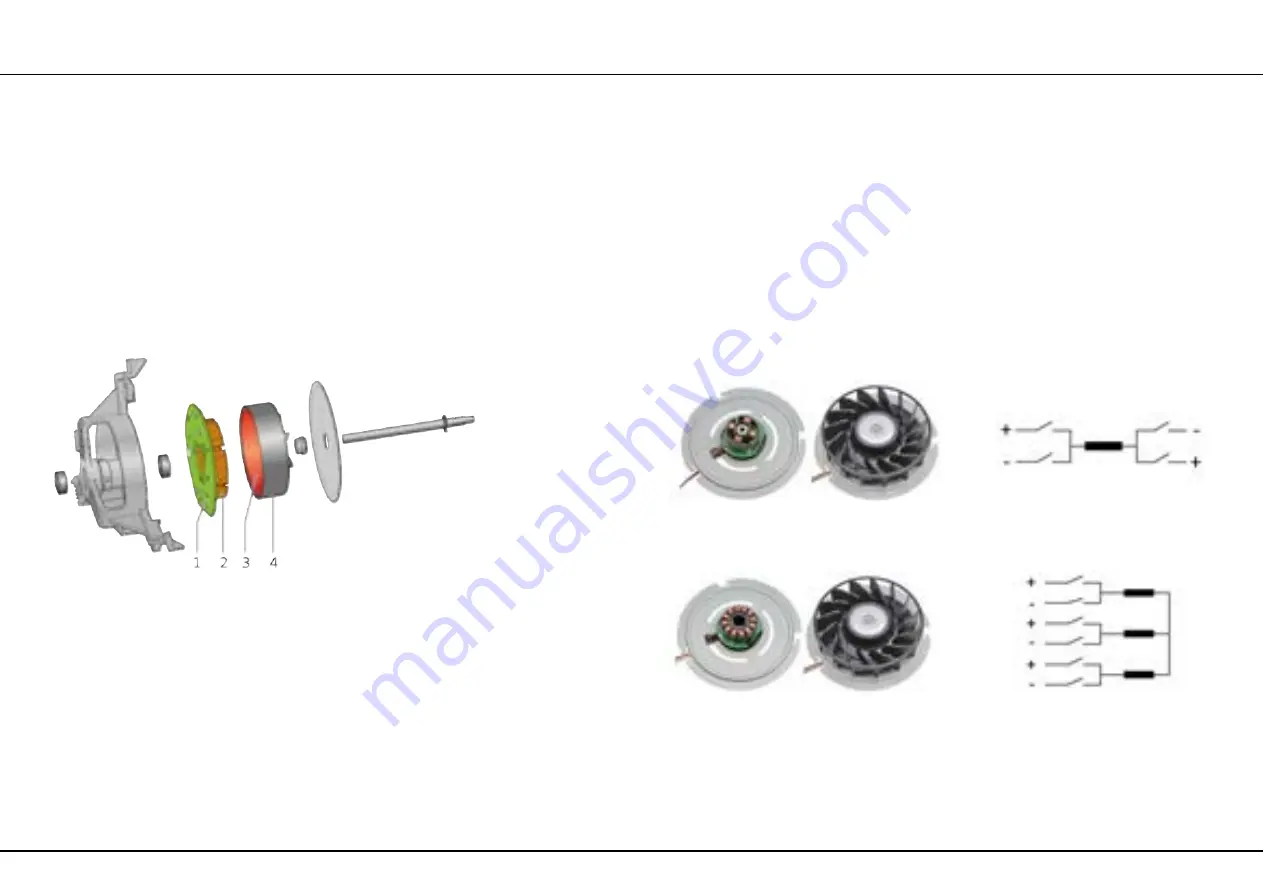
Design and function
2016-03-10 / DIS 184_58300000140186_ara_en_k
Copyright by BSH Hausgeräte GmbH
Page 14 of 181
3.3
Brushless direct current motor
A
B
rush
L
ess
D
irect
C
urrent motor (= BLDC motor) is an
E
lectronically
C
ommutated motor (= EC motor).
3.3.1
Structure
In a BLDC motor there is no electrical contact for between the movable rotor and
the fixed stator.
The movable rotor consists of permanent magnets. The fixed stator consists of
coils that are controlled in sequence by the motor electronics. This creates a rotary
field.
Fig. 9:
An external rotor motor assembly
1
Motor electronics
3
Magnets (rotor)
2
Coils (stator)
4
Motor housing (rotor)
A distinction is made between internal and external rotor motors. For internal rotor
motors, the movable rotor with the magnets is on the inside and the fixed stator is
on the outside. For external rotor motors, the movable rotor with the magnets is on
the outside and the fixed stator is on the inside.
Internal rotor motors are more efficient than external ones, but external rotor
motors have a higher torque than internal ones.
The motor electronics is made up of the power electronics and the control
electronics. The motor electronics generates the voltage with which the individual
coils are controlled.
Power transistors, for example power MOSFETs (
M
etal
O
xide
S
emiconductor
F
ield
E
ffect
T
ransistors) are used for this circuit.
3.3.2
Function and model variant
The motor is operated with direct current. Contrary to their name, the functional
principle is not based on that of a direct current motor, but on that of a three-phase
synchronous motor with excitation by means of a permanent magnet. The coils
create a rotating magnetic field, which pulls the permanent magnets with it.
There are motors with at least two or with many coils. Depending on the number of
the coils, the coils are controlled single-phase, two-phase or three-phase.
The efficiency is greater for three-phase controls than for single-phase controls.
The torque is greater for twelve coils than for four.
Fig. 10:
BLDC motor, 4-pole, single-phase, for appliances without pyrolytic self-
clean systems
Fig. 11:
BLDC motor, 12-pole, three-phase, for appliances with pyrolytic self-
clean systems