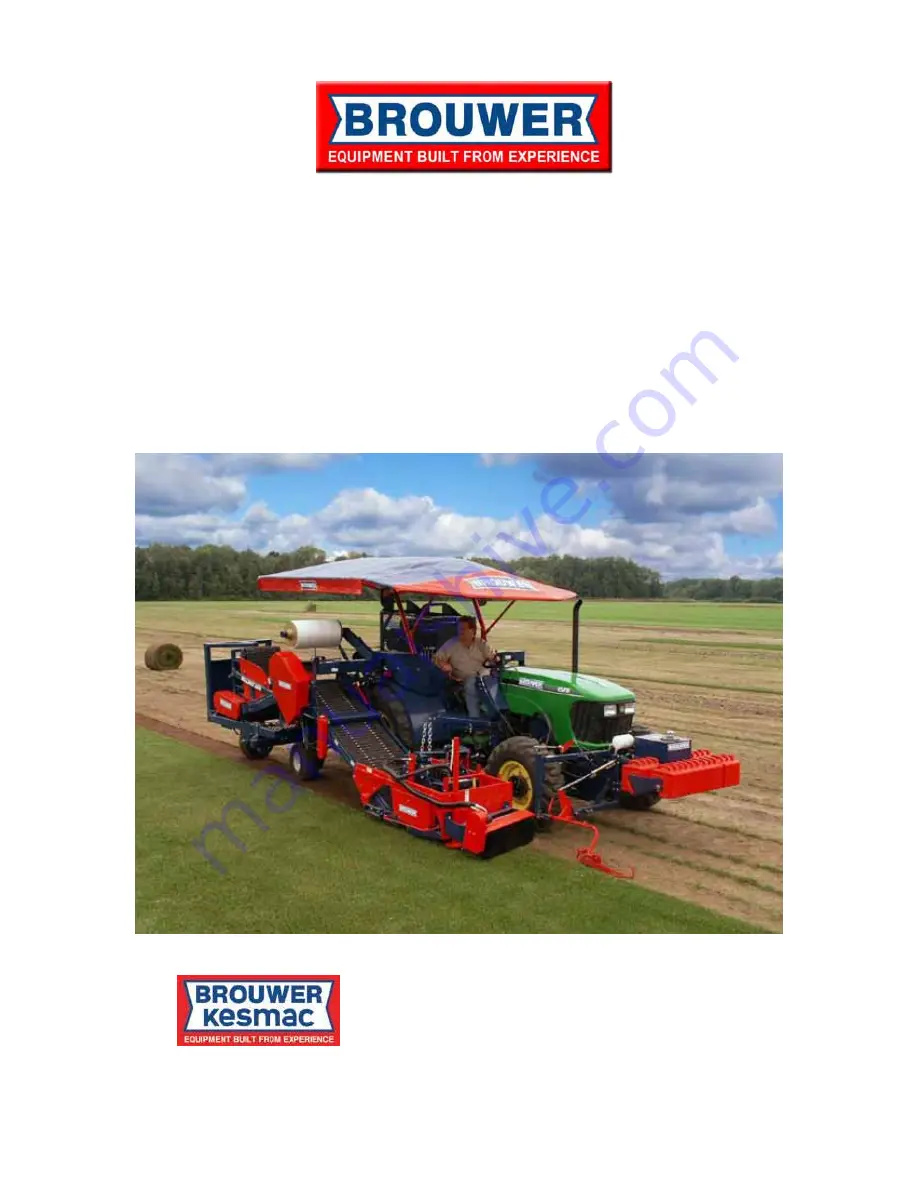
BROUWER SOD HARVESTER
ROLLMAX 2400
Model 5990280/1
OPERATOR’S MANUAL
KM99174
August 2008
Kesmac Inc.
23324 Woodbine Avenue, Keswick Ontario Canada L4P 3E9
Tel (905) 476-6222 Fax (905) 476-6744
Web Site www.brouwerturf.com Email [email protected]
Содержание 5990280/1
Страница 2: ......
Страница 4: ......
Страница 6: ......
Страница 8: ......
Страница 19: ...SAFETY 1 11 Warning Decals This page intentionally left blank ...
Страница 22: ......
Страница 34: ......
Страница 57: ...LUBRICATION SCHEDULE SECTION 4 General Information 4 01 Lubrication Charts 4 02 4 03 ...
Страница 58: ......
Страница 61: ...LUBRICATION 4 03 AUTO STEER ...
Страница 62: ......
Страница 64: ......
Страница 70: ......
Страница 71: ...ELECTRICAL SECTION 6 Electrical Control Box 6 01 Electrical Schematic 6 02 6 06 ...
Страница 72: ......
Страница 79: ......