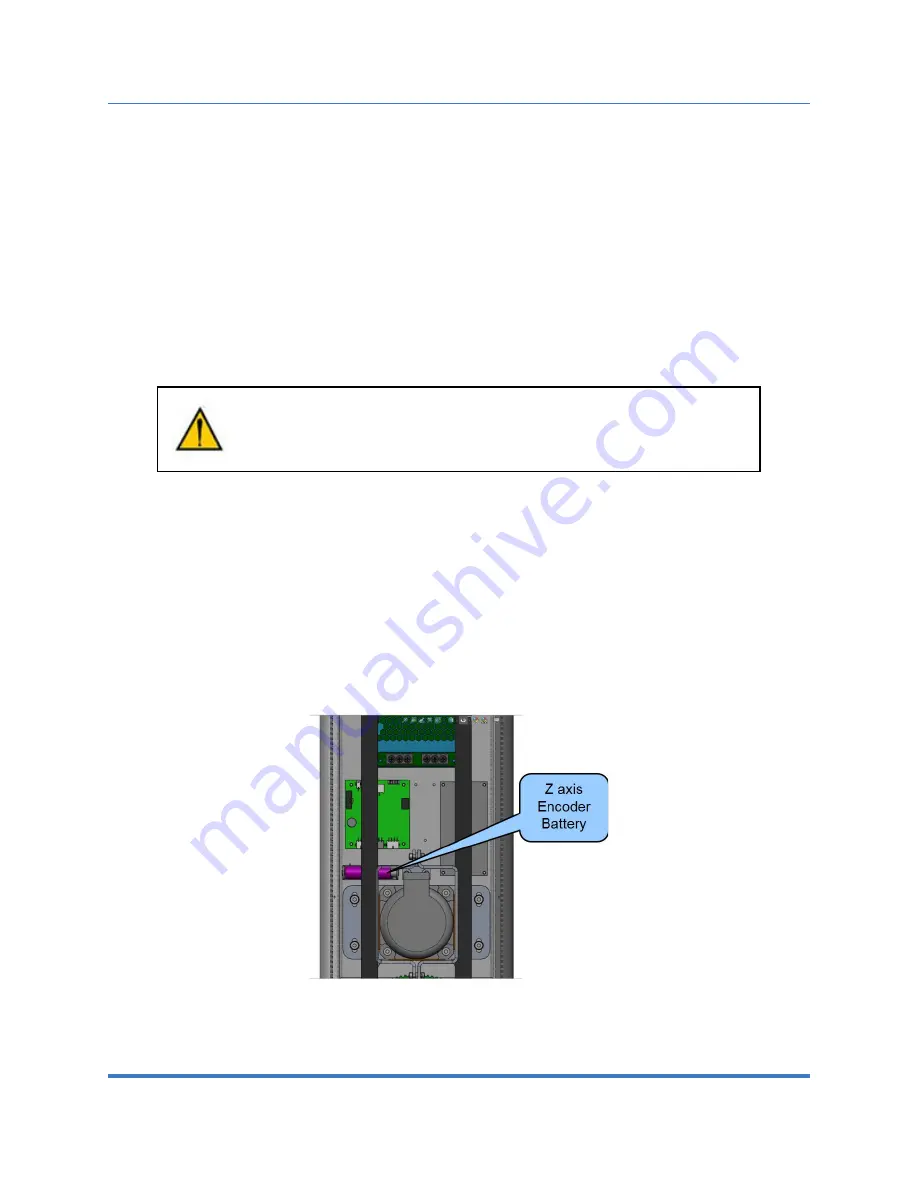
Brooks Automation
P/N: PFD0-DI-00010, Rev 5.0.0, April 9, 2022
Service Procedures
Copyright © 2022, Brooks Automation, Inc.
95
the calibration pins if desired-see Calibrating the Robot), or another known position,
and check the joint angles in the Virtual Pendant in the Web Operator Interface. See
the Calibration Procedure below for the joint angles in the Calibration Position.
If the robot joints after this procedure followed by homing are different from the
above, then the robot needs to be re-calibrated. See procedure below.
Replacing the Encoder Batteries
DANGER:
Before replacing the encoder battery, the AC power should be
disconnected. Removing the front cover allows access to the AC power
terminals.
The Encoder Batteries are designed to last for several years with robot power turned off. With robot
power turned on, there is no drain on the battery. The battery voltage is monitored by the system. The
nominal battery voltage is 3.6 volts. If the battery voltage drops to 3.3 volts an error message “Encoder
Battery Low” is generated. At this level the absolute encoder backup function will still work, however the
Battery should be replaced. If the voltage drops to 2.5 volts, an error message “Absolute Encoder Down”
is generated. At this point, the absolute encoder backup function will not work.
Note that if any motor/encoder is disconnected from the encoder battery by disconnecting the encoder
cable, the “Encoder Battery Low” or Encoder Battery Down” message will be generated. However, in this
case the encoder battery does not need to be replaced. It is only necessary to re-calibrate the robot, see
below.