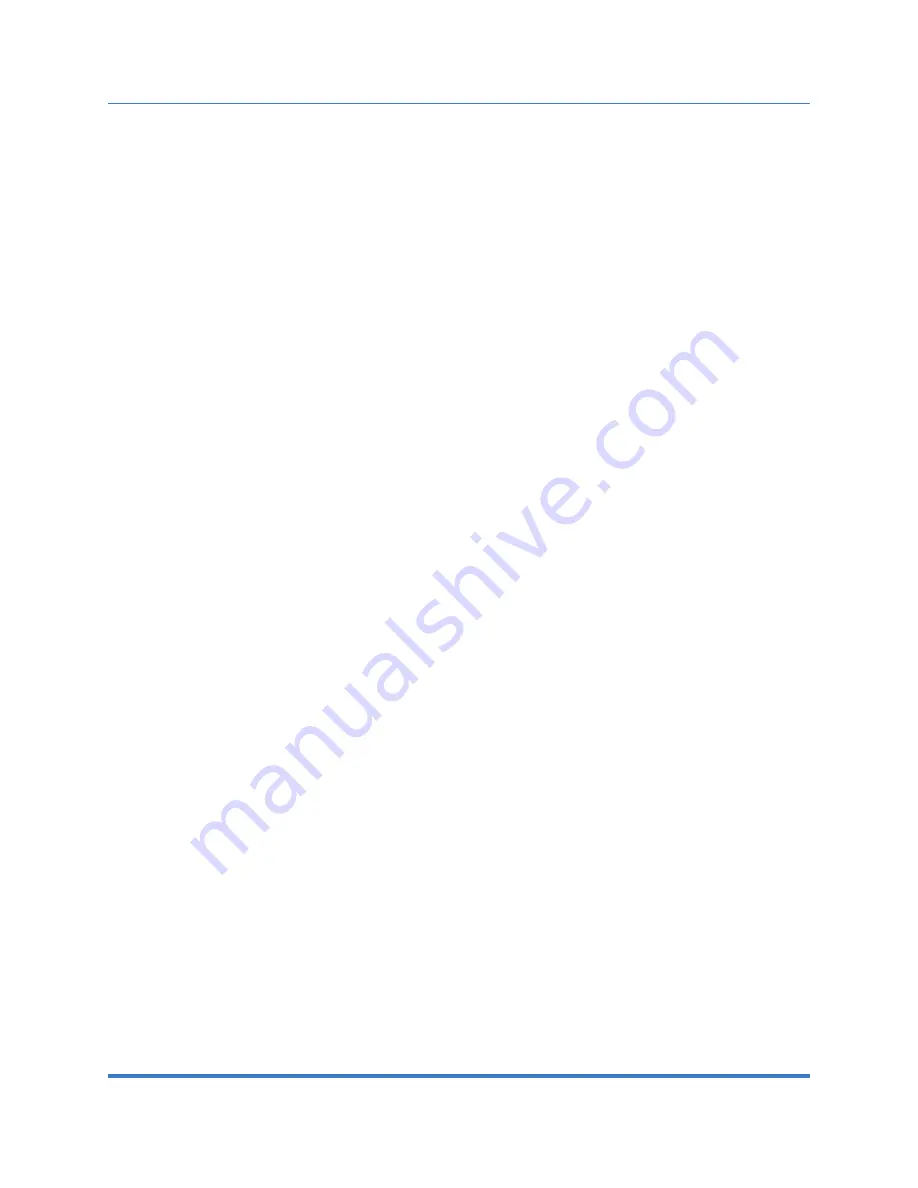
Brooks Automation
P/N: PFD0-DI-00010, Rev 5.0.0, April 9, 2022
Collaborative Robot Safety
Copyright © 2022, Brooks Automation, Inc.
25
2.
Impact force in free space (Transient contact).
This is the dynamic case of the robot colliding
with person where the person is free to recoil from the collision. In some cases, the speed and
inertia of the person should be added to the speed and inertia of the robot. The inertia of the
robot will include the payload, the robot structure, and the forward reflected inertia of the motor
and gear train, which can be quite significant. Impact force is considered to be a transient force of
short duration.
3.
Impact force against a surface. (Trapping)
This is the case where the person or appendage is
trapped between the robot and a hard surface with the
robot moving at speed
. While this can
be rare for many applications given proper workcell design, it should be considered. High speed
impacts which trap an operator against a surface may be avoided by teaching an “Approach”
position which is a greater distance from a fixture than any operator appendage that might enter
the workcell, and moving to this “Approach” position at high speed, then moving to the final
position at a rigid surface at a slow speed which will not create excessive force in the event of a
trapped operator.
4.
Pressure, or force per unit area.
130N of force applied to a large area, for example 50mm X
50mm is quite different from this same force applied to a small area, for example 1mm X 1mm.
Note that ISO/TS 15066 does not differentiate between clamping/squeezing force (low speed) and impact
forces against a rigid surface (high speed) and refers to both cases as “quasi-static” even though they are
quite different, as the high speed impact will include dynamic forces from the moving mass, while the low
speed clamping forces will be mainly due to motor torques.
Robot Testing and Safety Circuits
While some robots have 6 or even 7 axes and can move in many directions, generally testing can be
done in the horizontal plane and in the vertical direction. Since gravity adds to the force in the
downwards vertical direction, and since in the horizontal plane forces are symmetric in opposite
directions, testing in +X, +Y, and –Z (downwards) is generally sufficient to characterize robot forces.
Precise uses a test stand, to which a certified force gage can be attached in either the vertical or
horizontal direction, for testing forces. A “compliance plate” assembly is attached to the robot to simulate
the compliance of the human hand of 75N/mm.
Clamping/squeezing force is measured by moving the robot slowly into the force gage until the robot
reaches its maximum force and generates an error.
Based on Table A2 from ISO/TS 15066 (Appendix
C), Precise has selected the maximum clamping force (quasi-static) to be 140N for a collaborative
robot.
Transient impact force in free space is measured by moving the robot at its maximum permitted speed
and payload with the compliance plate impacting the force sensor when the force sensor is held by a
person in free space.
Based on Table A2 from ISO/TS 15066, Precise has selected the maximum
impact force (transient force) in free space to be 280N for the hand and forearm and 130N for the
skull for a collaborative robot.
Impact force against a rigid surface (trapping) is measured by moving the robot at speeds up to its
maximum permitted speed and payload with the compliance plate impacting the force sensor when the