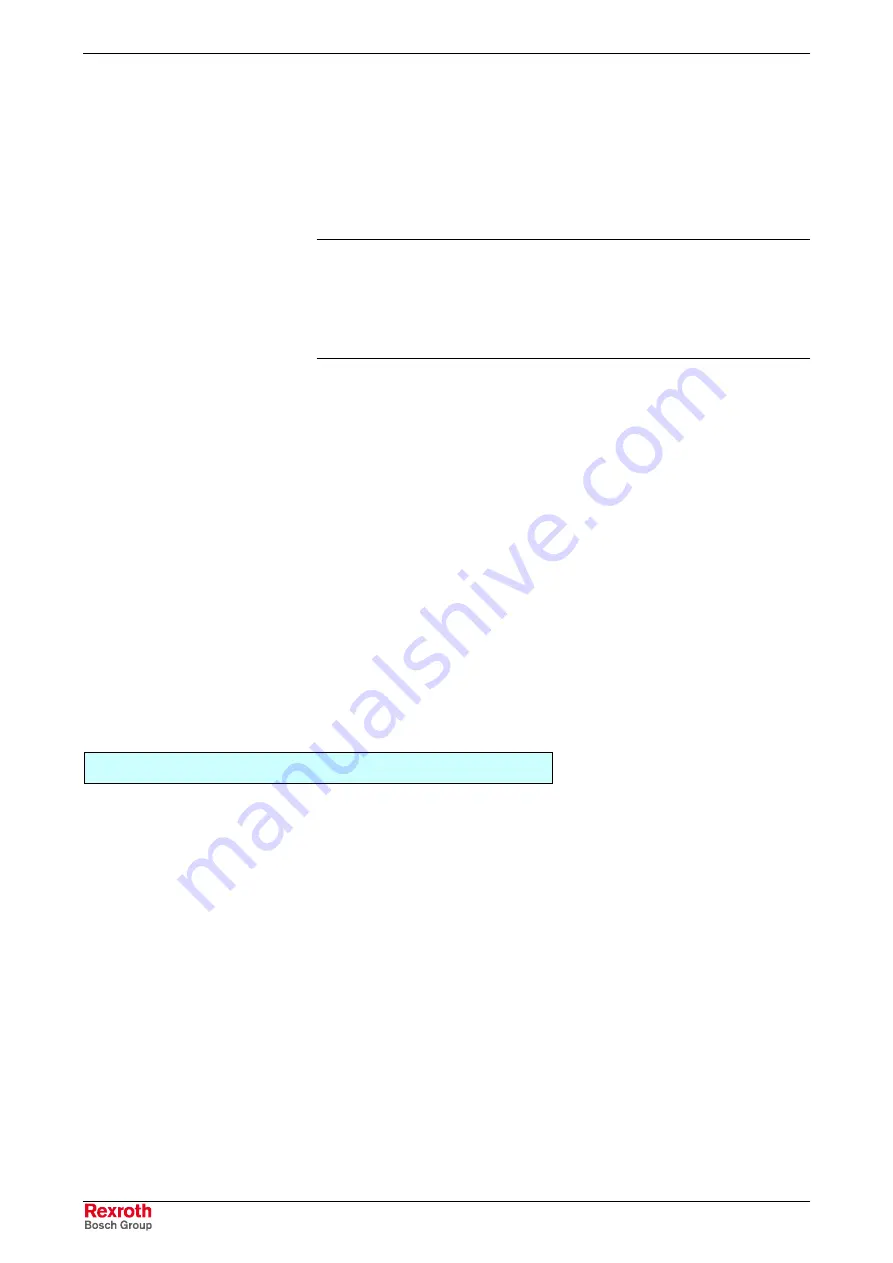
8-78
Drive Functions
MPH-02, MPB-02, MPD-02
DOK-INDRV*-MP*-02VRS**-FK01-EN-P
smoothness of running and positioning velocity (e.g. for cutting
material into sections) [watch
P-0-0038, Torque-generating current,
command value
!].
The slip monitor with active measuring wheel mode is activated by
entering a value greater zero in parameter
•
P-0-0244, Monitoring window of slip in %
.
Note:
The value "0" in parameter P-0-0244 causes the slip monitor
to be switched off! The value in
P-0-0242, Current actual slip
value in %
then is no longer reset after each revolution of
measuring wheel or external encoder, but the total slip since
the deactivation of the slip monitor is displayed (possibly
continuously increasing value).
Procedure:
1. First enter high value in parameter
P-0-0244, Monitoring window of
slip in %
so that slip monitor cannot be triggered.
2. Enter value "0" in parameter
P-0-0243, Maximum occurred actual
slip value in %
and run complete positioning cycle of axis with
maximum infeed velocity several times, if necessary.
3. After having cyclically moved axis read parameter P-0-0243 and enter
the value, multiplied by a safety factor (e.g. "2"), in parameter
P-0-0244, Monitoring window of slip in %
!
If the value in
P-0-0242, Current actual slip value in %
exceeds the
value of P-0-0244, the controller generates the error message
F2036
Excessive position feedback difference
and the drive reacts with the
error reaction that has been set.
8.8
Positive Stop Drive Procedure
Brief Description
For special applications it is required to move machine axes operated in
position or velocity control up to a limit stop in order to generate forces of
pressure.
When an axis in the standard situation has moved up to a limit stop, the
drive should signal a drive error by the monitoring facilities of the position
or velocity control loop and react with shutdown.
But if the drive can detect the special case of operation "positive stop
drive procedure", it can ignore the messages of the position and motions
monitors and generate the required force of pressure, if necessary.
The control master signals this special case to the controller of IndraDrive
devices via a command. Upon this command, the drive switches off the
respective monitors and acknowledges axis standstill to have been
detected and a parameterizable force or torque threshold to have been
exceeded.
Slip Monitoring with Measuring
Wheel Mode
Base package
of all variants
Courtesy
of
CMA/Flodyne/Hydradyne
▪
Motion
Control
▪
Hydraulic
▪
Pneumatic
▪
Electrical
▪
Mechanical
▪
(800)
426-5480
▪
www.cmafh.com