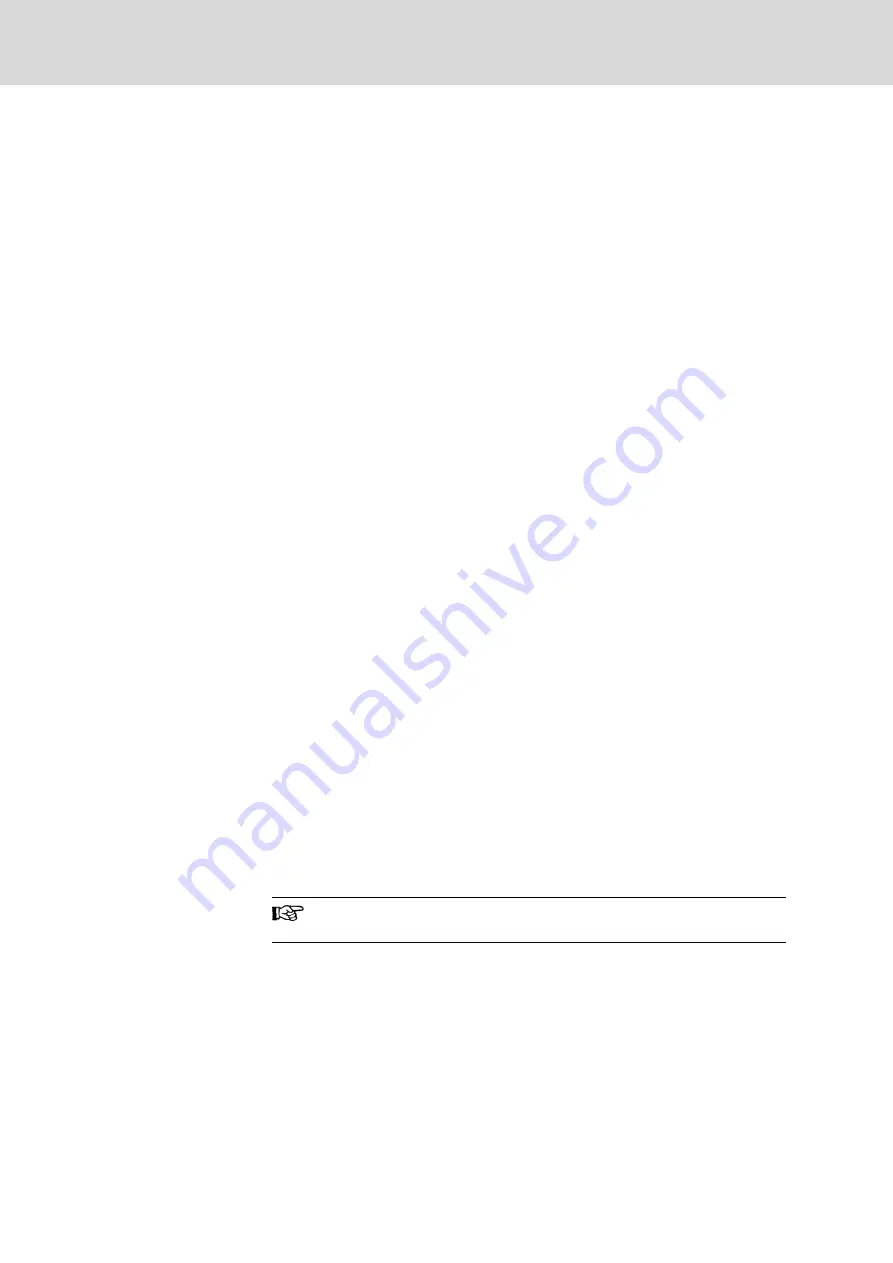
Third-Party Motors
General Information on Third-Party Motors
Why Use Third-Party Motors at Rexroth IndraDrive Cs Controllers?
Today, machine axes are mainly moved with electric drives. Motors of stand‐
ard design are used in most cases, as this is the most cost-efficient solution.
Special Requirements
Due to special requirements at machine axes, constructional or safety-related
aspects, it may be necessary for the machine manufacturer to use a motor
construction diverging from the standard.
Motor Design not Included in
Product Range
For these cases, there is the demand on drive suppliers to realize drives with
motors that are not included in their own product ranges due to the special
design.
Check Before Using Third-Party
Motors
At drive controllers of the Rexroth IndraDrive Cs range, it is possible to use
third-party motors. For this purpose, check whether the third-party motor
complies with the requirements of use.
The Functional Description of the firmware contains forms for motor data.
Procure the completed forms for the performance test of a third-party motor.
Which are the Important Directives?
In accordance with the legal regulations (EU Directive EMC 89/336/EEC and
the German EMC laws), installations and machines must be designed and
built in accordance with the present state-of-the-art of standardization.
In order to comply with the machine directives regarding "electromagnetic
compatibility (EMC)", a conformity test of the drive system (motor with con‐
troller and connection design) must be carried out. The machine manufactur‐
er must guarantee the test of the drive system and compliance with the direc‐
tives.
Third-Party Motors to be Controlled
Motor Types
The following motor types can be controlled:
●
Asynchronous motors, rotary
●
Asynchronous motors, linear
●
Synchronous motors, rotary
●
Synchronous motors, linear
These motors can be operated within the scope of the technical data of the
selected Rexroth IndraDrive Cs controller. If motors have been provided with
a holding brake, it should be controlled via the drive controller. Make sure
that the relevant technical data of the motor holding brake are complying with
those of the holding brake output!
For third-party motors Rexroth, as a matter of principle, does not
assume the guarantee for the power data at the motor shaft!
Synchronous Motors
For synchronous motors with motor encoder, the commutation offset must be
set during commissioning. The drive firmware provides several methods for
determining this offset so that it is possible to determine the value for different
motor characteristics.
Bosch Rexroth AG
DOK-INDRV*-HCS01******-PR05-EN-P
48/341
Rexroth IndraDrive CsDrive Systems with HCS01
Combining the individual components
Содержание Rexroth IndraDrive CsDrive System with HCS01
Страница 1: ...Rexroth IndraDrive Cs Drive Systems with HCS01 Project Planning Manual R911322210 Edition 05 ...
Страница 30: ...Bosch Rexroth AG DOK INDRV HCS01 PR05 EN P 28 341 Rexroth IndraDrive CsDrive Systems with HCS01 ...
Страница 250: ...Bosch Rexroth AG DOK INDRV HCS01 PR05 EN P 248 341 Rexroth IndraDrive CsDrive Systems with HCS01 ...
Страница 314: ...Bosch Rexroth AG DOK INDRV HCS01 PR05 EN P 312 341 Rexroth IndraDrive CsDrive Systems with HCS01 ...
Страница 318: ...Bosch Rexroth AG DOK INDRV HCS01 PR05 EN P 316 341 Rexroth IndraDrive CsDrive Systems with HCS01 ...
Страница 332: ...Bosch Rexroth AG DOK INDRV HCS01 PR05 EN P 330 341 Rexroth IndraDrive CsDrive Systems with HCS01 ...
Страница 342: ...Notes Bosch Rexroth AG DOK INDRV HCS01 PR05 EN P 340 341 Rexroth IndraDrive CsDrive Systems with HCS01 ...
Страница 343: ...Notes DOK INDRV HCS01 PR05 EN P Bosch Rexroth AG 341 341 Rexroth IndraDrive CsDrive Systems with HCS01 ...