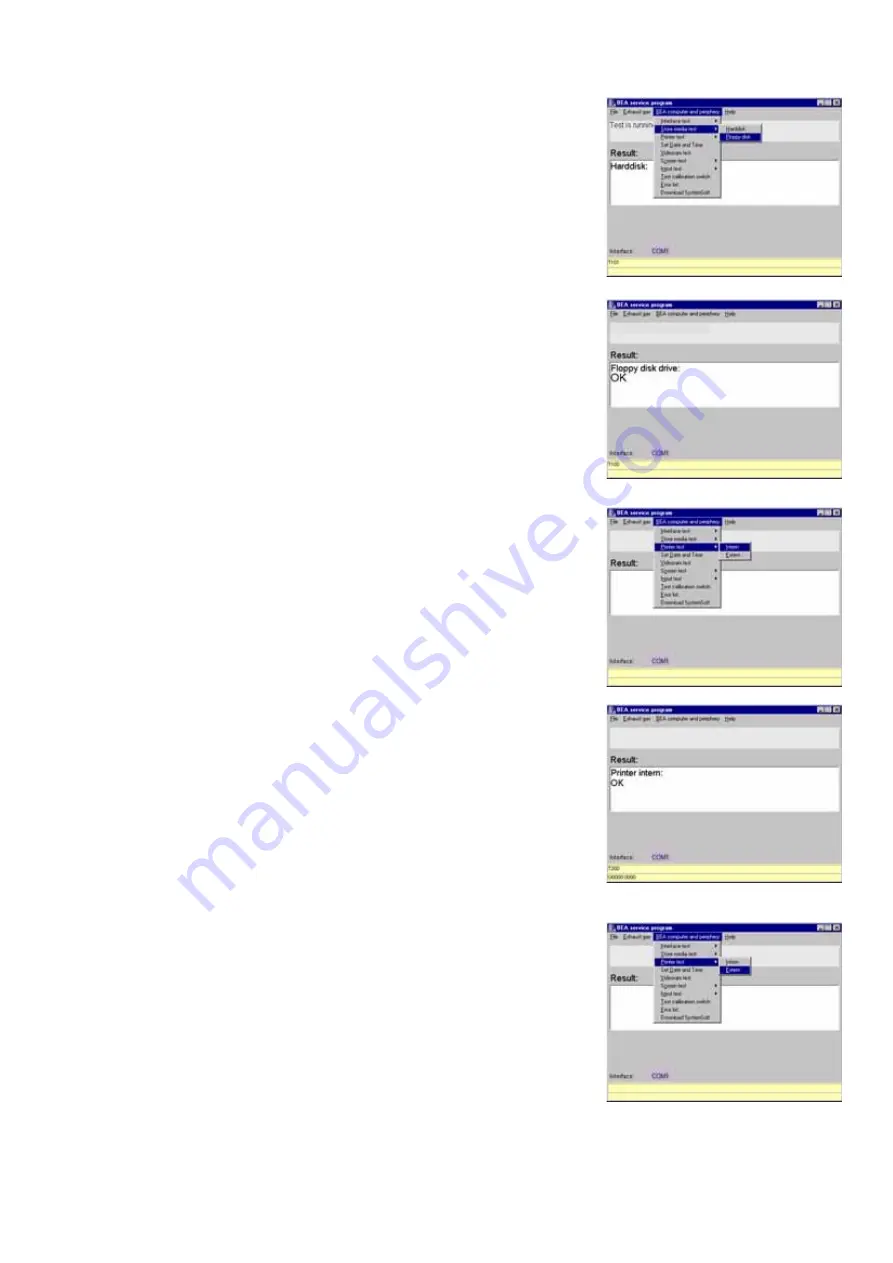
39
5.9
Checking the Floppy disk drive
5.10
Checking the internal printer
5.11
Checking the external printer
Insert an OS9-formatted floppy disk in the
disk drive.
Open the menu
Store media test
and
then select
Floppy disk
.
The Floppy disk drive test is executed
automatically.
If the disk drive test is error-free, the
message
OK
appears in the results box.
If the test is unsuccessful, an error messa-
ge is displayed.
For example: B0246:
1300
.
1300
= No connection to disk drive
Open the
Printer test
menu, then select
Intern
.
The printer test is executed automatically.
A printout is produced on the internal
printer bearing the possible font.
The message
OK
appears on screen if the
printer test is passed.
Open the
Printer test
menu, then select
Extern
.
Содержание BEA 150
Страница 91: ...92 12 Overview 12 1 Electrical wiring Siemens analysis chamber 459716 2Ha ...
Страница 94: ...95 12 4 Hosing Siemens analysis chamber X26 X24 X25 X22 X5 LP 223 X19 459716Ht ...
Страница 96: ...97 12 6 Electrical wiring Andros analysis chamber 4597162Ht ...
Страница 99: ...100 12 9 Hosing Andros analysis chamber 459869_03Ht ...
Страница 100: ...101 12 10 Gas circuit diagram Andros analysis chamber ...