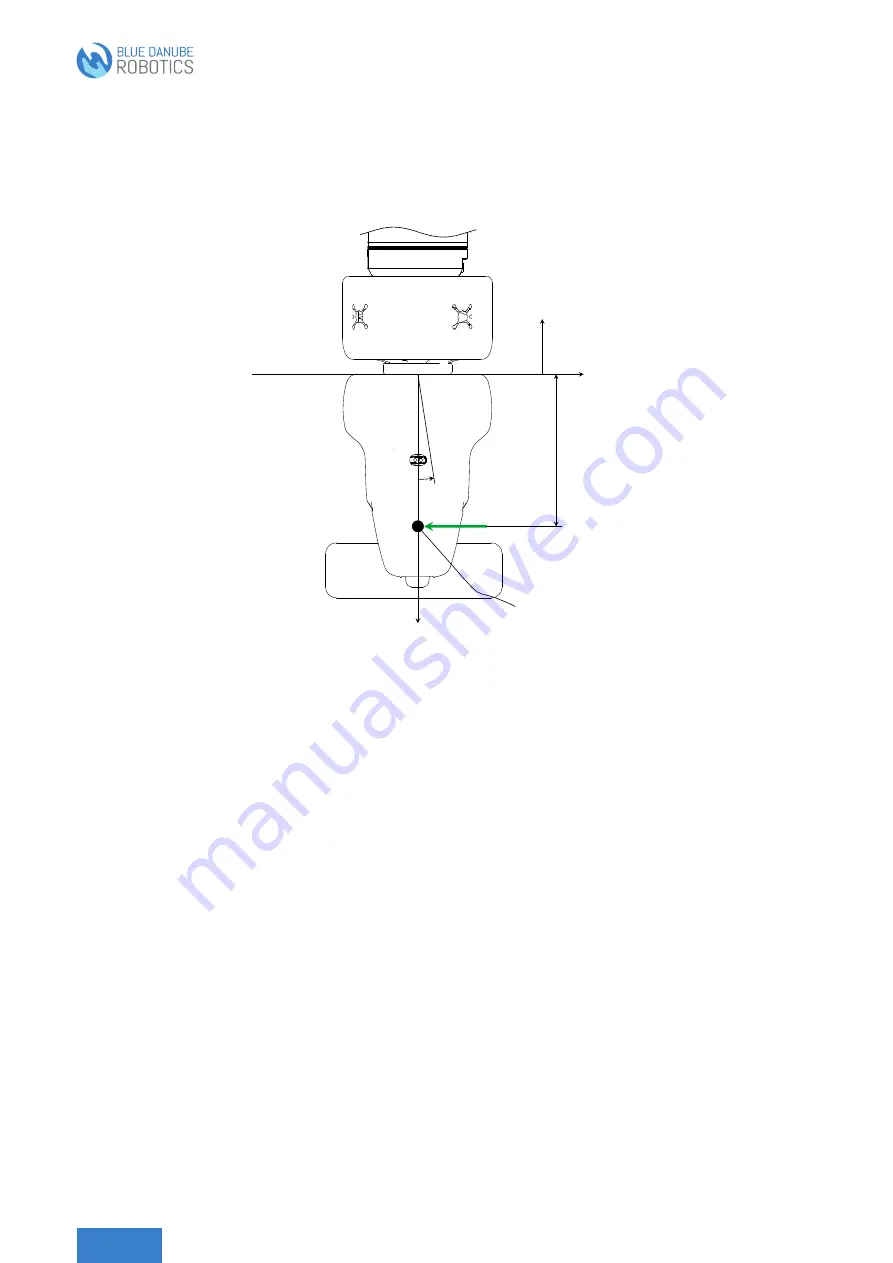
5.4 Actuation due to robot accelerations
a
R
Excessive acceleration by the robot can actuate the AIRSKIN® Safetyflange. Excessive accelerations lead to tilting
(tilt angle
±
8
.
8
°) of the AIRSKIN® Safetyflange. When it comes to acceleration, the geometries of the gripper and
the load that is to be manipulated have an important role to play because they are crucial for the center of gravity
position
l
s
.
x
z
11 mm
z-compliance
F
a
l
s
±
8
.
8
° Tilt angle
m
G
m
L
Center of gravity
(robot gripper incl. load)
Fig. 5.12: Actuation due to robot accelerations
a
R
.
F
a
=
m
g
·
a
R
= (
m
G
+
m
L
)
·
a
R
(5.4)
shows the maximum possible robot acceleration
α
R
as a function of the distance from centroid
l
s
until the AIRSKIN® Safetyflange actuates. The characteristic curves refer to the freely configurable springs under
the maximum payload. The lower the center of gravity (or the higher the weight of the payload that is being
manipulated), the more easily the AIRSKIN® Safetyflange will actuate under acting robot acceleration
α
R
.
The AIRSKIN® Safetyflange is much more resilient against actuation due to robot acceleration if it is configured
with Spring 1 or Spring 2 with a low payload.
If one assumes that a payload of
10 kg
(without spring) with a very low center of gravity
l
s
=
200 mm
is being
manipulated, tilting would be actuated above acceleration of
α
R
=
1
.
35 m
/
s
2
(see following diagram). The accel-
eration of the robot should therefore be less than
α
R
=
1
.
35 m
/
s
2
so that unintentional actuation during operation
can be excluded.
For example, one obtains better characteristics with a payload of
2
.
5 kg
(with Spring 1) with a distance from cen-
troid of
l
s
=
100 mm
. Horizontal acceleration of
α
R
=
5
.
03 m
/
s
2
would be required to produce tilting and thus the
actuation of the AIRSKIN® Safetyflange.
If the payload that is being manipulated (with the same spring) becomes lower, it is possible to achieve improved
characteristics. With robot acceleration
α
R
, higher accelerations are possible with a lower payload.
shows the shift in the characteristic curve if the AIRSKIN® Safetyflange that is configured with Spring 2 manipu-
lates a payload of
2
.
5 kg
instead of the maximum
5 kg
.
Содержание AIRSKIN
Страница 1: ...SAFETYFLANGE OPERATING MANUAL 2020 06 30 v1 2 English Translation...
Страница 17: ...A A A A 135 5 1 63 13 0 5 82 5 89 0 5 Fig 3 3 Dimensions of the AIRSKIN Safety ange in mm 13 62...
Страница 25: ...1 2 3 Plain Bearing Washer 1 5 4 6 3 Plain Bearing Washer 2 7 Fig 4 4 Exchanging the spring 21 62...
Страница 57: ...1 2 3 Plain Bearing Washer 1 5 4 6 3 Plain Bearing Washer 2 7 Fig 10 2 53 62...
Страница 66: ...15 Declaration of Conformity and manufacturer 62 62...