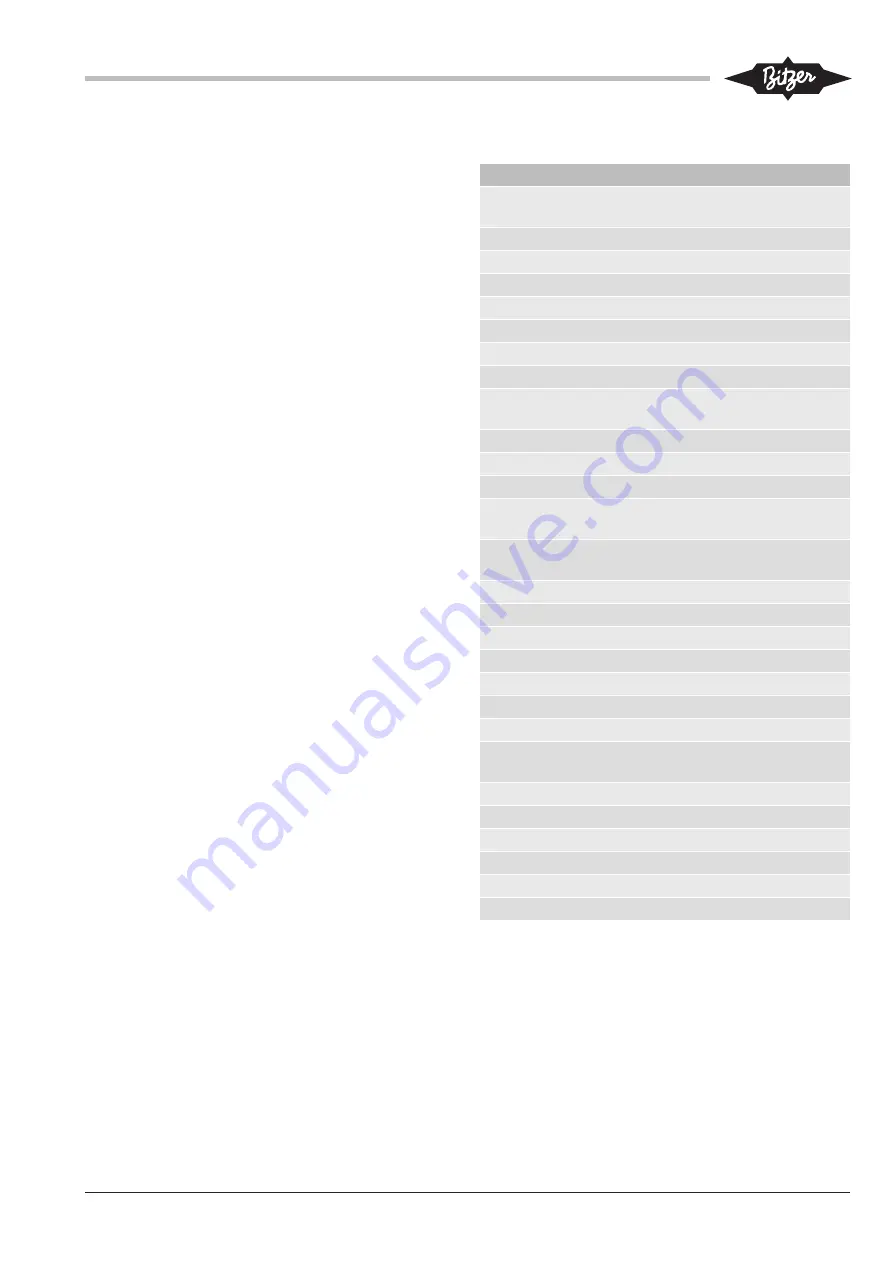
KT-102-1
9
6
Electrical connection
Keep the compressor module energized when the mo-
tor is not running. If necessary, the module activates
the oil heater, thus ensuring the lubricity of the oil even
after a long standstill period.
De-energize the module only if you plan a long stand-
still period of the compressor or for maintenance pur-
poses. For further information on the compressor mod-
ule CM-RC-01, see enclosed Technical Information
KT-230.
6.1
Motor connection
The line start permanent magnet motor (LSPM) of
the compressors for transcritical CO
2
ap-
plications is connected in direct on-line start and in star
wiring (mains frequency 400 V). Part windings or star/
delta start are not possible.
The schematic wiring diagram (see figure 8, page 10)
shows this direct star start. For details on the motor
connection, see adhesive label in the terminal box of
the compressor.
6.2
High pressure switch
According to EN378 directive, each compressor must
be provided with a high pressure switch (F5) for safety
cut-out in the safety chain. Depending on the displace-
ment and refrigerant charge, it must be designed as a
safety pressure cut-out and / or only as pressure cut-
out. The software-controlled monitoring of the com-
pressor module via the high pressure transmitter (B6)
does not sufficiently ensure the safety cut-out function.
The high pressure switch (F5) should preferably be
connected to terminal strip CN3 instead of the bridge.
The installation of a low pressure switch is not neces-
sary, depending on local regulations. The compressor
module is provided with an automatic low pressure cut-
out function.
6.3
Connecting operation monitoring via the BEST
SOFTWARE
The BEST SOFTWARE accesses the compressor
module via the Bluetooth interface, see chapter Com-
munication via BEST SOFTWARE, page 12. This in-
terface is deactivated in some non-European countries.
• If the Bluetooth interface should not be used:
• Connect the BEST interface converter to terminal
strip CN14 (Modbus).
In this case, the capacity control must be activated via
the analogue signal on terminal strip CN13.
6.4
Schematic wiring diagram
Abbr. Component
B1
Command for compressor start (release sig-
nal from system controller)
B6
High pressure transmitter (shortly available)
B7
Low pressure transmitter (shortly available)
F1
Main fuse
F2
Compressor fuse
F3
Control circuit fuse
F4
Oil monitoring: OLC-D1 or DP-1
F5
High pressure switch
F13
Overcurrent relay "motor" (1st part winding
and Y/Δ)
F14
Overcurrent relay "motor" (2nd part winding)
F17
Control transformer fuse
H3
Light "collective fault"
K1
Contactor "1st part winding" (PW) or main
contactor (Y/Δ)
K2
Contactor "2nd part winding" (PW) or delta
contactor (Y/Δ)
K3
Star contactor (Y/Δ)
M1
Compressor
M2
Additional fan
Q1
Main switch
R1..6 PTC sensor in motor winding
R7
Discharge gas temperature sensor
R8
Oil heater
R11
Optional temperature sensor (not included in
the scope of delivery)
S1
Control switch (on/off)
S2
Reset of CM-RC-01
T1
Control transformer (example for 230 V)
Y1
Solenoid valve "Start unloading SU"
Y3-1
Solenoid valve “1st capacity regulator CRII”
Y3-2
Solenoid valve “2nd capacity regulator CRII”
Tab. 3: Components of the schematic wiring diagram
Содержание 4CTEU-30LK
Страница 26: ...Notes...
Страница 27: ...Notes...