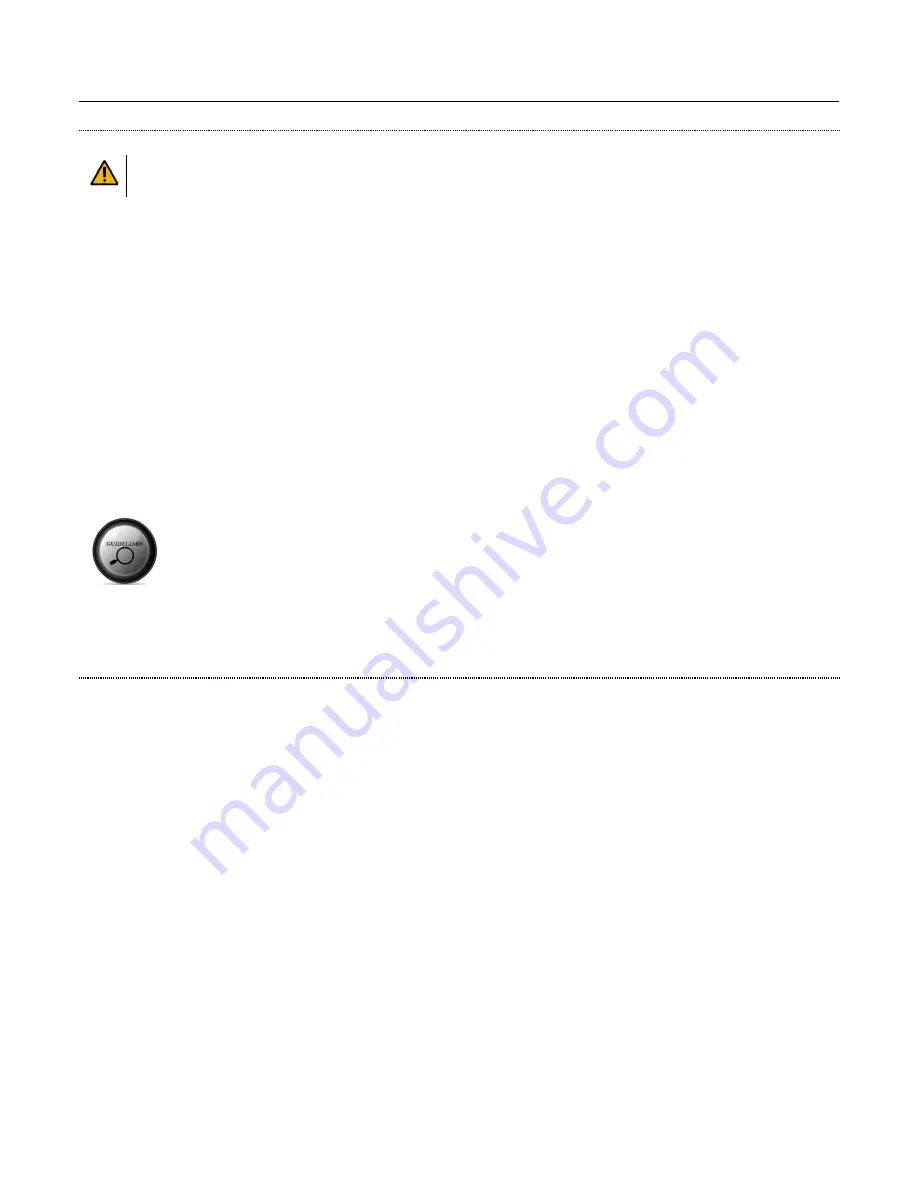
Installation
Bennett HF H35 Instruction Manual
19
PIPING/PLUMBING INSTRUCTIONS
GENERAL PIPING INFORMATION
WARNING: THESE NOTES ARE “MUST DO” REQUIREMENTS TO ENSURE A SUCCESSFUL INSTALLATION THAT MEETS BENNETT’S
LIMITED WARRANTY REQUIREMENTS.
1.
Use only piping, valves, and tubing that are intended for natural gas service. Refer to the
Hydrogen Footprint Drawing
s in
section.
2.
All piping must be clean of foreign debris, such as oil, grease, shavings, and other contaminants.
3.
All connections must be tight to prevent leaks.
4.
All piping systems must be marked in accordance with
ASME A13.1,
Scheme for the Identification of Piping Systems,
or other applicable
approved codes and standards.
•
At each critical process control valve.
•
At wall, floor, or ceiling penetrations.
•
At each change of direction.
•
At a minimum of every 20 ft. (6.1m) or fraction thereof through the piping run.
•
Do not bleed system by loosening fitting nut or fitting plug.
•
Do not assemble and tighten fittings when system is pressurized.
•
Make sure that the tubing rests firmly on the shoulder of the tube fitting body before tightening the nut.
•
Use the correct Swagelok gap inspection gauge to ensure sufficient pull-up upon initial installation.
•
Always use proper thread sealants on tapered pipe threads.
•
Do not mix materials or fitting components from various manufacturers
—
tubing, ferrules, nuts, and fitting bodies.
•
Never turn fitting body. Instead, hold fitting body and turn nut.
•
Avoid unnecessary disassembly of unused fittings.
•
Use only long reducers in female Swagelok end connections.
FIELD CONNECTIONS - HYDROGEN INLETS
A
9/16”
M/P (C&T) connection will be provided for each hydrogen inlet. Field Connection - Hydrogen Vent Outlet
A 1-inch (25 mm) Swagelok connection will be provided for hydrogen vent outlet field connection. The fitting must be installed per
applicable guidelines listed under
GENERAL PIPING INFORMATION
.
Содержание HIGH FLOW H35
Страница 12: ...Product Introduction Bennett HF H35 Instruction Manual 8 DISPENSER IDENTIFICATION NUMBER DIN...
Страница 84: ...Schematics Bennett HF H35 Instruction Manual 80 CHAPTER 8 SCHEMATICS...
Страница 85: ...Schematics Bennett HF H35 Instruction Manual 81...
Страница 86: ...Schematics Bennett HF H35 Instruction Manual 82...
Страница 87: ...Schematics Bennett HF H35 Instruction Manual 83...
Страница 88: ...Schematics Bennett HF H35 Instruction Manual 84...
Страница 89: ...Schematics Bennett HF H35 Instruction Manual 85...
Страница 90: ...Schematics Bennett HF H35 Instruction Manual 86...
Страница 91: ...Schematics Bennett HF H35 Instruction Manual 87...
Страница 92: ...Schematics Bennett HF H35 Instruction Manual 88...
Страница 93: ...Schematics Bennett HF H35 Instruction Manual 89...
Страница 94: ...Schematics Bennett HF H35 Instruction Manual 90...
Страница 95: ...Schematics Bennett HF H35 Instruction Manual 91...
Страница 96: ...Schematics Bennett HF H35 Instruction Manual 92...
Страница 97: ...Schematics Bennett HF H35 Instruction Manual 93...
Страница 98: ...Schematics Bennett HF H35 Instruction Manual 94...