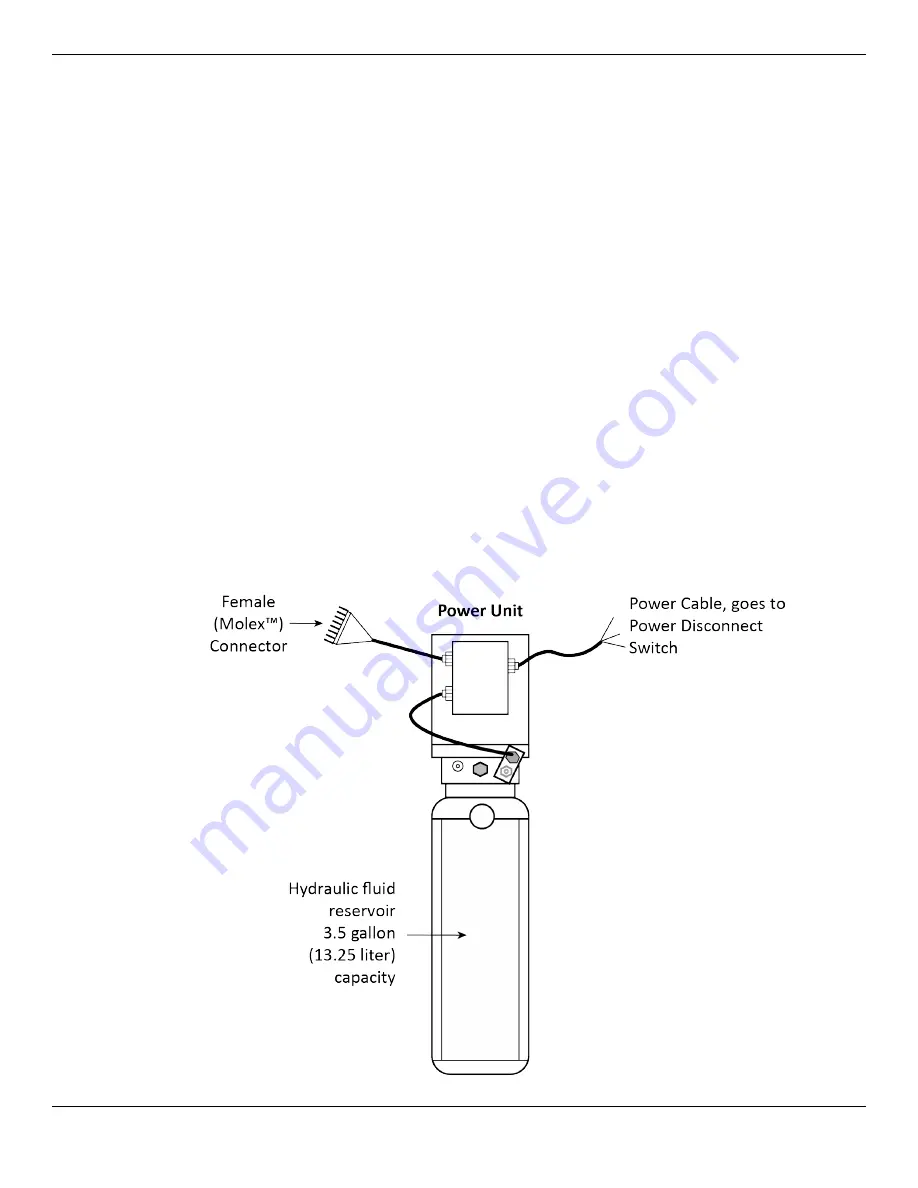
Autostacker™ Parking Lift
31
P/N 5900002 — Rev. D — August 2019
Connect the Power Unit
The Power Unit comes assembled from the factory. You need to attach it to the back of the Console
and then connect it properly, described in this section.
If you have a Multi-Lift setup, this procedure will be different for you
The Power Units that can be used with your Autostacker include either 110 VAC, 220 VAC at 50/60
Hz, 1 Ph or 380 VAC at 50 Hz, 3 Ph.
⚠
DANGER
All wiring
must
be performed by a licensed, certified Electrician.
Refer to
⚠
CAUTION
The Power Unit’s motor is
not
thermally protected.
The Power Unit has multiple connections:
•
Two Hydraulic Hoses and One Return Line
. Already in place and connected.
•
Power Cable
. The Power Cable on the Power Unit connects to the top of the Power Disconnect
Switch. A licensed, certified Electrician is required for this connection.
•
Power Source
. The Power Source connects to the bottom of the Power Disconnect Switch.
Also requires a licensed, certified Electrician.
•
Controls
. The Female (Molex™) Connector on the Power Unit connects to a Male Connector
coming down from the Controls in the Top of the Console.
The following diagram shows a sample Autostacker Power Unit.
Содержание Autostacker PL-6SR
Страница 68: ...Autostacker Parking Lift 68 P N 5900002 Rev D August 2019 Wiring Diagrams ...
Страница 69: ...Autostacker Parking Lift 69 P N 5900002 Rev D August 2019 ...
Страница 70: ...Autostacker Parking Lift 70 P N 5900002 Rev D August 2019 ...
Страница 72: ...Autostacker Parking Lift 72 P N 5900002 Rev D August 2019 ...
Страница 73: ...Autostacker Parking Lift 73 P N 5900002 Rev D August 2019 ...
Страница 74: ...Autostacker Parking Lift 74 P N 5900002 Rev D August 2019 Labels ...
Страница 75: ...Autostacker Parking Lift 75 P N 5900002 Rev D August 2019 ...
Страница 76: ...Autostacker Parking Lift 76 P N 5900002 Rev D August 2019 ...
Страница 77: ...Autostacker Parking Lift 77 P N 5900002 Rev D August 2019 ...
Страница 78: ...Autostacker Parking Lift 78 P N 5900002 Rev D August 2019 ...
Страница 79: ...Autostacker Parking Lift 79 P N 5900002 Rev D August 2019 ...
Страница 80: ...Autostacker Parking Lift 80 P N 5900002 Rev D August 2019 Parts Diagrams ...
Страница 81: ...Autostacker Parking Lift 81 P N 5900002 Rev D August 2019 ...
Страница 82: ...Autostacker Parking Lift 82 P N 5900002 Rev D August 2019 ...
Страница 83: ...Autostacker Parking Lift 83 P N 5900002 Rev D August 2019 ...
Страница 84: ...Autostacker Parking Lift 84 P N 5900002 Rev D August 2019 ...
Страница 85: ...Autostacker Parking Lift 85 P N 5900002 Rev D August 2019 ...
Страница 86: ...Autostacker Parking Lift 86 P N 5900002 Rev D August 2019 ...
Страница 87: ...Autostacker Parking Lift 87 P N 5900002 Rev D August 2019 ...
Страница 88: ...Autostacker Parking Lift 88 P N 5900002 Rev D August 2019 ...
Страница 89: ...Autostacker Parking Lift 89 P N 5900002 Rev D August 2019 ...
Страница 90: ...Autostacker Parking Lift 90 P N 5900002 Rev D August 2019 ...
Страница 91: ...Autostacker Parking Lift 91 P N 5900002 Rev D August 2019 ...
Страница 92: ...Autostacker Parking Lift 92 P N 5900002 Rev D August 2019 ...
Страница 93: ...Autostacker Parking Lift 93 P N 5900002 Rev D August 2019 ...
Страница 94: ...Autostacker Parking Lift 94 P N 5900002 Rev D August 2019 ...
Страница 95: ...Autostacker Parking Lift 95 P N 5900002 Rev D August 2019 ...
Страница 96: ...Autostacker Parking Lift 96 P N 5900002 Rev D August 2019 ...
Страница 97: ...Autostacker Parking Lift 97 P N 5900002 Rev D August 2019 ...
Страница 98: ...Autostacker Parking Lift 98 P N 5900002 Rev D August 2019 ...
Страница 99: ...Autostacker Parking Lift 99 P N 5900002 Rev D August 2019 ...
Страница 100: ...Autostacker Parking Lift 100 P N 5900002 Rev D August 2019 ...
Страница 101: ...Autostacker Parking Lift 101 P N 5900002 Rev D August 2019 ...
Страница 102: ...Autostacker Parking Lift 102 P N 5900002 Rev D August 2019 ...
Страница 103: ...Autostacker Parking Lift 103 P N 5900002 Rev D August 2019 ...
Страница 104: ...1645 Lemonwood Drive Santa Paula CA 93060 USA 2018 BendPak Inc All rights reserved bendpak com ...