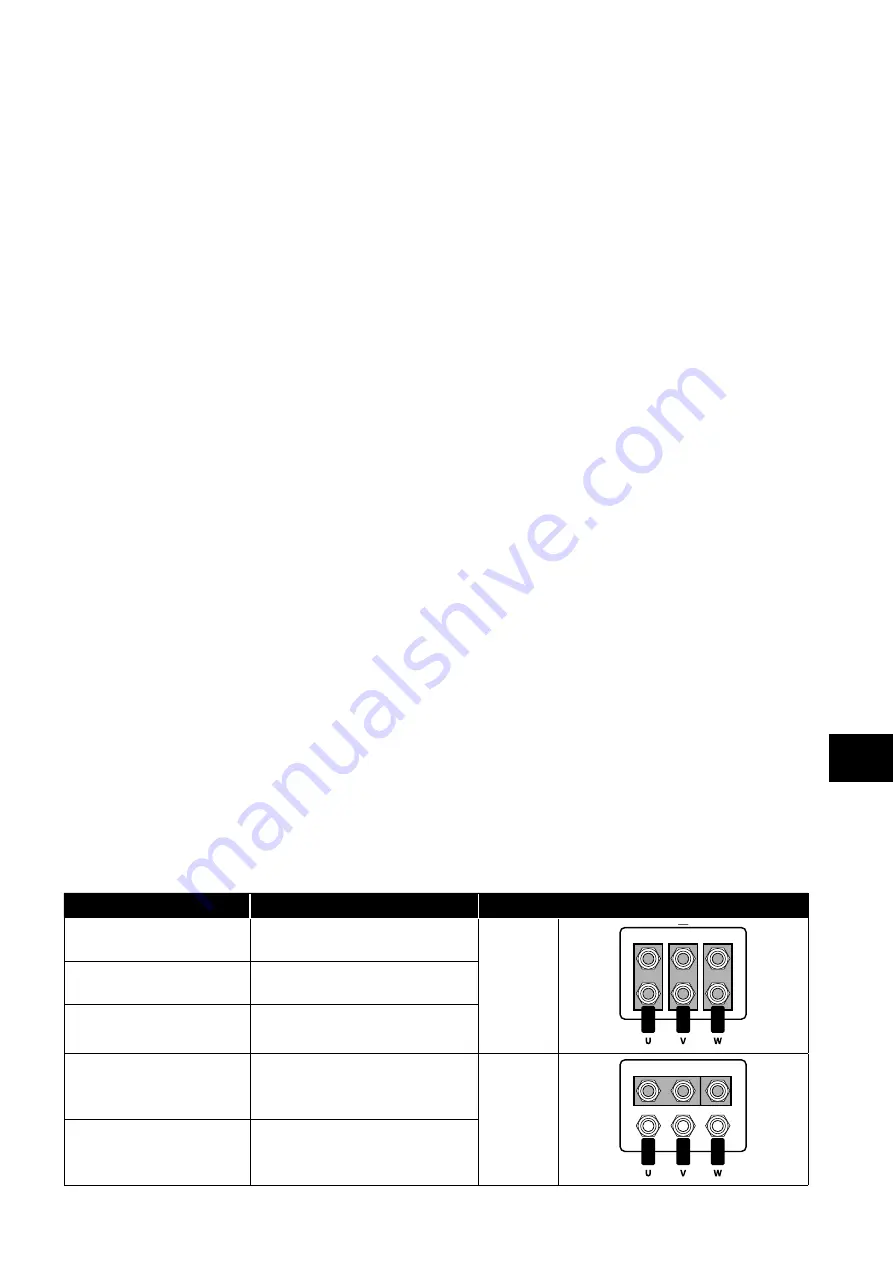
Version 3.04
| Beijer BFI-P2 User Guide |
23
www.beijerelectronics.com
4.3.4. Input Choke
An optional Input Choke is recommended to be installed in the supply line for drives where any of the following conditions occur:
The incoming supply impedance is low or the fault level / short circuit current is high.
NOTE
For IP20 Frame Size 8 the input current level will vary according to supply impedance. At minimum a 1% line choke must be
installed. Installing a 4% line choke further helps towards minimising harmonic current distortion and total current levels. 1% and 4% line
chokes are available.
The supply is prone to dips or brown outs.
An unbalanced supply system is used (3 phase drives) where the voltage levels during on load operation exceed the designed 3%
capacity of the BFI drive.
The power supply to the drive is via a busbar and brush gear system (typically overhead Cranes).
In all other installations, an input choke is recommended to ensure protection of the drive against power supply faults.
4.4. Operation of 3 Phase drives from a Single Phase Supply
A special function of Beijer BFI-P2 allows all drives designed for operation on 3 phase supplies to be operated on a single phase
supply of the correct rated voltage at up to 50% of the nominal capacity.
For Example, Model Number BFI-P2-64-0900-3F4N-TN can be operated on a single phase supply, 380 – 480 volts, with the
maximum output current limited to 45 Amps.
The supply must be connected to the L1 and L2 terminals of the drive.
4.5. Operation with DC Power Supply or Common DC Bus
Beijer BFI-P2 models provide terminals to directly connect to the DC Bus for applications which require this. For further information on
using the DC Bus connections, please contact Beijer Electronics.
4.6. Motor Connection
The drive inherently produces fast switching of the output voltage (PWM) to the motor compared with operation of the motor
directly from the mains supply. Most modern industrial motors are wound for operation with a variable speed drive and will have
insulation rated accordingly. However, on some motors the quality of insulation may be insufficient or unknown. In such cases the
motor manufacturer should be consulted and preventative measures may be required prior to operating with the drive.
The motor should be connected to the BFI drive U, V, and W terminals using a suitable 3 or 4 core cable. Where a 3 core cable
is utilised, with the shield operating as an earth conductor, the shield must have a cross sectional area at least equal to the phase
conductors when they are made from the same material. Where a 4 core cable is utilised, the earth conductor must be of at least
equal cross sectional area and manufactured from the same material as the phase conductors.
Automatic switchgear should not be installed between the drive output and the motor, opening and closing contacts in this circuit
whilst the drive is energised will inevitably reduce the lifetime of the drive and could cause product failure. If an isolator is required
to be placed between the drive and the motor in order to comply with local regulations, the device must not be operated when the
drive is running.
For compliance with the European EMC directive, a suitable screened (shielded) cable should be used. Braided or twisted type
screened cable where the screen covers at least 85% of the cable surface area, designed with low impedance to HF signals are
recommended as a minimum. Installation within a suitable steel or copper tube is generally also acceptable.
The motor earth must be connected to one of the BFI drive earth terminals to provide a low impedance path for common mode
leakage current to return to the drive. This is best achieved in practice by using a cable with suitable shielding which provides a low
impedance path at high frequencies, and ensuring correct, low impedance earth bonding of the motor cable at both ends. For further
information, refer to section
4.13. EMC Compliant Installation
4.7. Motor Terminal Box Connections
Most general purpose motors are wound for operation on dual voltage supplies. This is indicated on the nameplate of the motor. This
operational voltage is normally selected when installing the motor by selecting either STAR or DELTA connection. STAR always gives
the higher of the two voltage ratings.
Incoming Supply Voltage
Motor Nameplate Voltages
Connection
230
230 / 400
Delta
∆
400 / 460
400 / 690
575
575 / 1000
400
230 / 400
Star
⅄
575
330 / 575
4
Elec
trical Installation