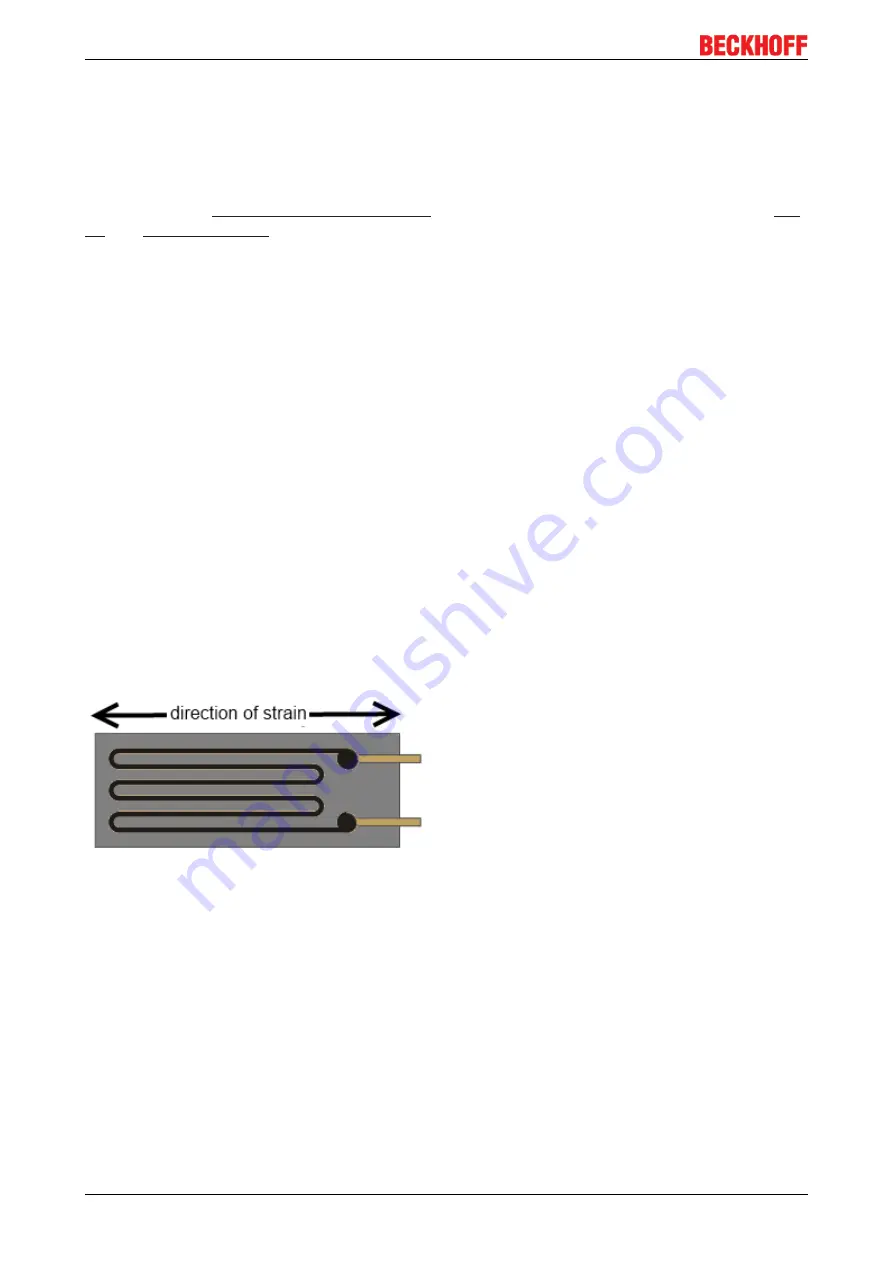
Basic function principles
ELX3351
26
Version: 1.3.1
4
Basic function principles
4.1
EtherCAT basics
Please refer to the
for the EtherCAT fieldbus basics, also available as
4.2
Basic principles of strain gauge technology
Basic information on the technological field of strain gauges/load cells as metrological instruments is to be
given below. The information is of general nature; it is up to the user to check the extent to which it applies to
his application.
• Strain gauges serve either to directly measure the static (0 to a few Hz) or dynamic (up to several KHz)
elongations, compressions or torsions of a body by being directly fixed to it, or to measure various
forces or movements as part of a sensor (e.g. load cells/force transducers, displacement sensor,
vibration sensors).
• In the case of the optical strain gauge (e.g. Bragg grating), an application of force causes a
proportional change in the optical characteristics of a fiber used as a sensor. Light with a certain
wavelength is fed into the sensor. Depending upon the deformation of the grating, which is laser-cut
into the sensor, due to the mechanical load, part of the light is reflected and evaluated using a suitable
measuring transducer (interrogator).
The commonest principle in the industrial environment is the electrical strain gauge. There are many
common terms for this type of sensor: load cell, weighbridge, etc.
Structure of electrical strain gauges
A strain gauge consists of a carrier material (e.g. stretchable plastic film) with an applied metal film from
which a lattice of electrically conductive resistive material is worked in very different geometrical forms,
depending on the requirements.
Fig. 19: Strain gauge
This utilizes a behavior whereby, for example in the case of strain, the length of a metallic resistance network
increases and its diameter decreases, as a result of which its electrical resistance increases proportionally.
ΔR/R = k*ε
ε = Δl/l thereby corresponds to the elongation; the strain sensitivity is called the k-factor. This also gives rise
to the typical track layout inside the strain gauge: the resistor track or course is laid in a meandering pattern
in order to expose the longest possible length to the strain.
Example
The elongation ε = 0.1% of a strain gauge with k-factor 2 causes an increase in the resistance of 0.2%.
Typical resistive materials are constantan (k~2) or platinum tungsten (92PT, 8W with k ~4). In the case of
semiconductor strain gauges a silicon structure is glued to a carrier material. The conductivity is changed
primarily by deformation of the crystal lattice (piezo-resistive effect). k-factors of up to 200 can be achieved.
Содержание ELX3351
Страница 2: ......
Страница 10: ...Foreword ELX3351 10 Version 1 3 1 Fig 2 ELX9012 with date code 32180005 and Ex marking...