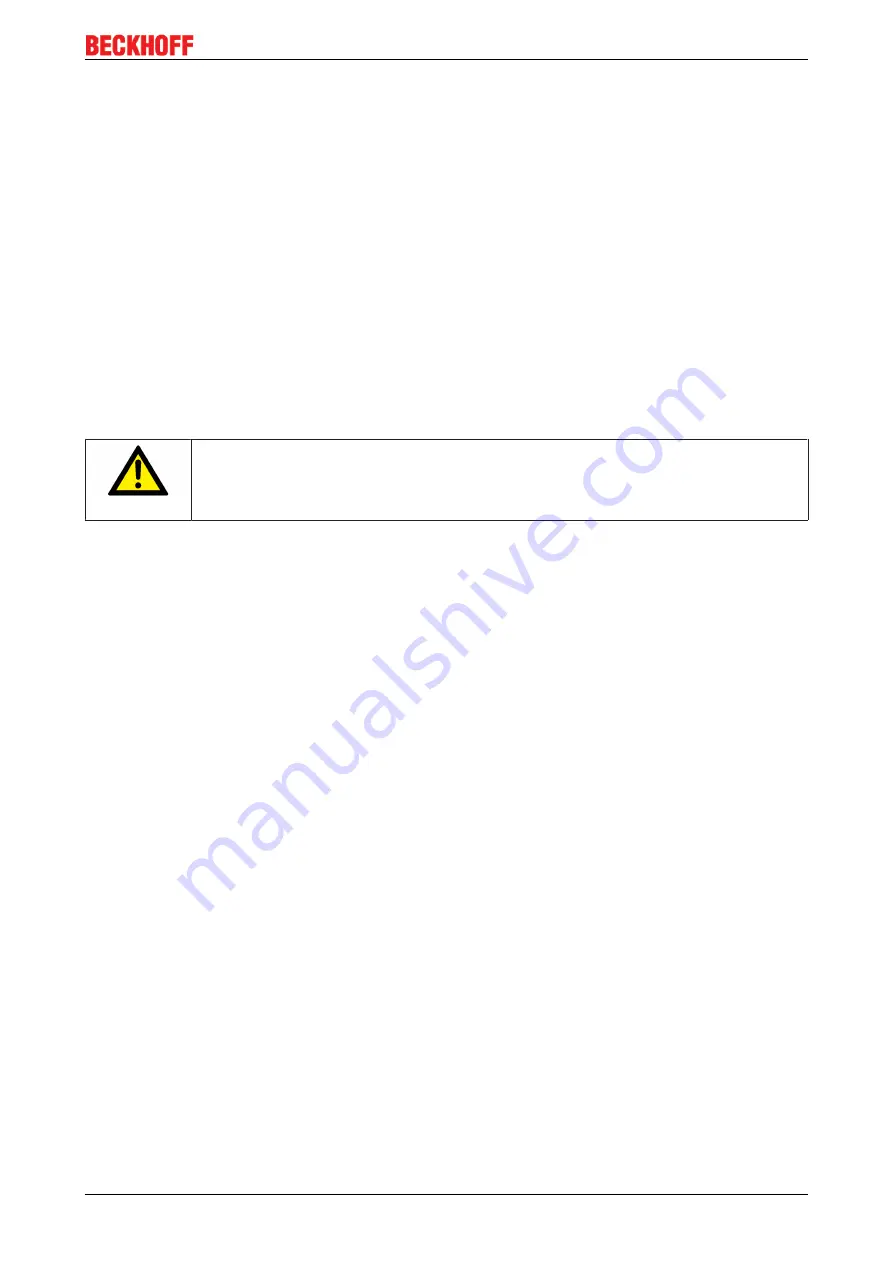
Parameterization and Commissioning
BC3150
27
Version: 2.1.0
4.2
Configuration
4.2.1
Overview
Configuration types
The Bus Terminal controllers of the BCxx50, BCxx20 and BXxx00 series can be configured in two different
ways: DEFAULT CONFIG or TwinCAT CONFIG.
DEFAULT-CONFIG
Bus Terminals are mapped in the order they are inserted, i.e. first the complex Bus Terminals followed by the
digital Bus Terminals.
The complex Bus Terminals are mapped as follows:
• Word Alignment
• complex representation
CAUTION
The process image depends on the connected terminals!
The process image changes when a terminal is added or removed!
The data of the fieldbus slaves interface are referred to as PLC variables. The PLC variables have
addresses from %QB1000 and %IB1000
The DEFAULT CONFIG (without PLC program) can also be used for writing and testing of the Connected
Bus Terminals. To this end, the Bus Terminal Controller must be scanned in the System Manager, and
FreeRun mode must be enabled (to use this function, no PLC program may be active on the Bus Terminal
Controller).
TWINCAT-CONFIG
In the TwinCAT CONFIG the Bus Terminals and PLC variables can be freely linked as required (TwinCAT
System Manager file required). The configuration is transferred to the coupler via the System Manager
and ADS.
The following is required for the TwinCAT configuration (TC file):
• Via the fieldbus (PROFIBUS, CANopen, Ethernet)
PROFIBUS: (BC3150, BX3100)
◦ PC with FC310x from version 2.0 and TwinCAT 2.9 build 1000
◦ BX3100 with CIF60 or CP5412
◦ TwinCAT 2.9 build 946
(
NOTE:
with PROFIBUS cards from Hilscher only one ADS communication is permitted, i.e.
either System Manager or PLC Control)
CANopen: (BC5150, BX5100)
◦ PC with FC510x from version 1.76 TwinCAT build 1030
DeviceNet: (BC5250, BX5200)
◦ on request
Ethernet: (BC9050, BC9020, BC9120, BX9000)
◦ PC with TwinCAT 2.10 build 1322
• Via the serial ADS TwinCAT 2.9 build 1010
◦ BX3100 version 1.00
◦ BX5100 version 1.00
◦ BX5200 version 1.10
◦ BX8000 version 1.00
Содержание BC3150
Страница 1: ...Documentation BC3150 Bus Terminal Controller for PROFIBUS DP 2 1 0 2017 07 11 Version Date...
Страница 2: ......
Страница 45: ...Parameterization and Commissioning BC3150 45 Version 2 1 0 Fig 41 Sample for entering associated bytes...
Страница 57: ...Programming BC3150 57 Version 2 1 0 Fig 55 Build...
Страница 87: ...PROFIBUS BC3150 87 Version 2 1 0 Fig 78 RS485 topology with 3 segments and 2 repeaters...