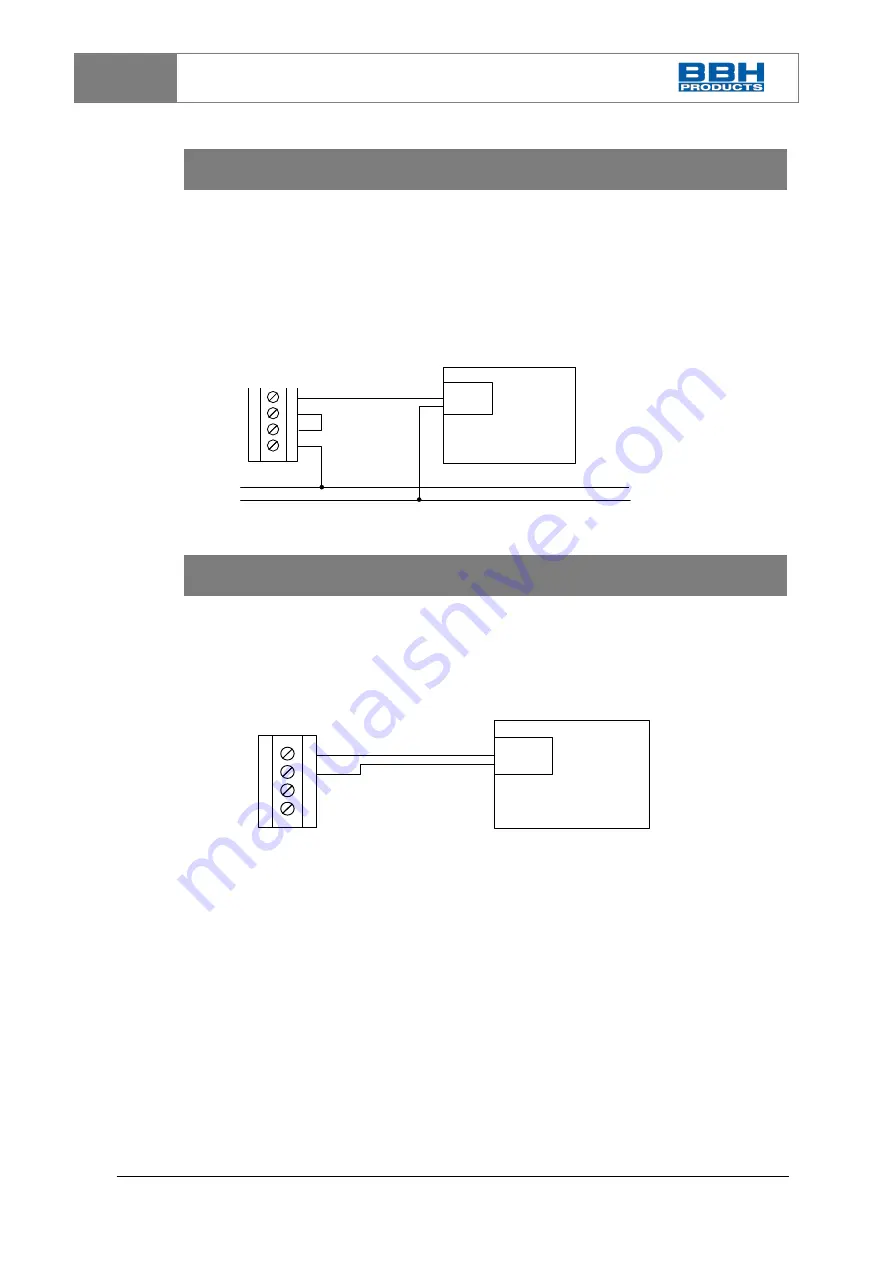
10
Safety-related characteristics
HB-37500-810-11-16F-EN SCU Installation Manual - Master and Slaves - SARC
Page 126 of 303
Status: 09.06.2022
10.3.4.2.6.
Dual-channel output with relay output and external control
circuit in PL e
For safety applications from PL d and higher acc. to EN ISO 13849-1. The
external circuit is controlled in dual-channel mode via the relay outputs. For
PL e acc. to EN ISO 13849-1 a sufficiently high testing rate and PL e is
demanded for the external circuit.
Fig. 31: Dual-channel output with relay output
–
external control circuit in PL e
L +
L -
Q5.1
X22
Q5.2
Q6.1
Q6.2
STO
Pl e
10.3.4.2.7.
Dual-channel output with semi-conductor output and external
control circuit in PL e
For safety applications from PL d and higher acc. to EN ISO 13849-1. The
external circuit is controlled in dual-channel mode via the semi-conductor
outputs. For PL e acc. to EN ISO 13849-1 PL e is demanded for the external
circuit
STO
Pl e
Q1_PP
X21
Q2_PN
Q3_PP
Q4_PN
Fig. 32: Dual-channel output with semi-conductor output and external
control circuit in PL e
X22 / X44
QR0L
QR0
QR1L
QR1
X21 / X43
QX00_PP
QX01_PN
QX02_PP
QX03_PN
Содержание SCU Series
Страница 178: ...Appendix data sheets SCU Master ...
Страница 179: ...Appendix data sheets SCU Master ...
Страница 180: ...Appendix data sheets SCU Master ...
Страница 181: ...Appendix data sheets SCU Master ...
Страница 182: ...Appendix data sheets SCU Master ...
Страница 183: ...Appendix data sheets SCU Master ...
Страница 184: ...Appendix data sheets SCU Master ...
Страница 185: ...Appendix data sheets SCU Master ...
Страница 186: ...Appendix data sheets SCU Master ...
Страница 187: ...Appendix data sheets SCU Master ...
Страница 188: ...Appendix data sheets SCU Master ...
Страница 189: ...Appendix data sheets SCU Master ...
Страница 190: ...Appendix data sheets SCU Master ...
Страница 191: ...Appendix data sheets SCU Master ...
Страница 192: ...Appendix data sheets SCU Master ...
Страница 193: ...Appendix data sheets SCU Master ...
Страница 194: ...Appendix data sheets SCU Master ...
Страница 195: ...Appendix data sheets SCU Master ...
Страница 196: ...Appendix data sheets SCU Master ...
Страница 197: ...Appendix data sheets SCU Master ...
Страница 198: ...Appendix data sheets SCU Master ...
Страница 199: ...Appendix data sheets SCU Slaves ...
Страница 200: ...Appendix data sheets SCU Slaves ...
Страница 201: ...Appendix data sheets SCU Slaves ...
Страница 202: ...Appendix data sheets SCU Slaves ...
Страница 203: ...Appendix data sheets SCU Slaves ...
Страница 204: ...Appendix data sheets SCU Slaves ...
Страница 205: ...Appendix data sheets SCU Slaves ...
Страница 206: ...Appendix data sheets SCU Slaves ...
Страница 207: ...Appendix data sheets SCU Slaves ...
Страница 208: ...Appendix data sheets SCU Slaves ...
Страница 209: ...Appendix data sheets SCU Slaves ...
Страница 210: ...Appendix data sheets SCU Slaves ...
Страница 211: ...Appendix data sheets SCU Slaves ...
Страница 212: ...Appendix data sheets SCU Slaves ...
Страница 213: ...Appendix data sheets SCU Slaves ...
Страница 214: ...Appendix data sheets SCU Slaves ...
Страница 215: ...Appendix data sheets SCU Slaves ...
Страница 216: ...Appendix data sheets SCU Slaves ...
Страница 217: ...Appendix data sheets SCU Slaves ...
Страница 218: ...Appendix data sheets SCU Slaves ...
Страница 219: ...Appendix data sheets SCU Slaves ...
Страница 220: ...Appendix data sheets SCU Slaves ...
Страница 221: ...Appendix data sheets SCU Slaves ...
Страница 222: ...Appendix data sheets SCU Slaves ...
Страница 223: ...Appendix data sheets SCU Slaves ...
Страница 224: ...Appendix data sheets SCU Slaves ...
Страница 225: ...Appendix data sheets SCU Slaves ...
Страница 226: ...Appendix data sheets SCU Slaves ...
Страница 227: ...Appendix data sheets SCU Slaves ...
Страница 228: ...Appendix data sheets SCU Slaves ...
Страница 229: ...Appendix data sheets SCU Slaves ...
Страница 230: ...Appendix data sheets SCU Slaves ...
Страница 231: ...Appendix data sheets SCU Slaves ...
Страница 232: ...Appendix data sheets SCU Slaves ...
Страница 233: ...Appendix data sheets SCU Slaves ...
Страница 234: ...Appendix data sheets SCU Slaves ...
Страница 235: ...Appendix data sheets SCU Slaves ...
Страница 236: ...Appendix data sheets SCU Slaves ...
Страница 237: ...Appendix data sheets SCU Slaves ...
Страница 238: ...Appendix data sheets SCU Slaves ...
Страница 239: ...Appendix data sheets SCU Slaves ...
Страница 240: ...Appendix data sheets SCU Slaves ...
Страница 241: ...Appendix data sheets SCU Slaves ...
Страница 242: ...Appendix data sheets SCU Slaves ...
Страница 243: ...Appendix data sheets SCU Slaves ...
Страница 244: ...Appendix data sheets SCU Slaves ...
Страница 245: ...Appendix data sheets SCU Slaves ...
Страница 246: ...Appendix data sheets SCU Slaves ...
Страница 247: ...Appendix data sheets SCU Slaves ...
Страница 248: ...Appendix data sheets SCU Slaves ...
Страница 249: ...Appendix data sheets SCU Slaves ...
Страница 250: ...Appendix data sheets SCU Slaves ...
Страница 251: ...Appendix data sheets SCU Slaves ...
Страница 252: ...Appendix data sheets SCU Slaves ...
Страница 253: ...Appendix data sheets SCU Slaves ...
Страница 254: ...Appendix data sheets SCU Slaves ...
Страница 255: ...Appendix data sheets SCU Slaves ...
Страница 256: ...Appendix data sheets SCU Slaves ...
Страница 257: ...Appendix data sheets SCU Slaves ...
Страница 258: ...Appendix data sheets SCU Slaves ...
Страница 259: ...Appendix data sheets SCU Slaves ...
Страница 260: ...Appendix data sheets SCU Slaves ...
Страница 261: ...Appendix data sheets SCU Slaves ...
Страница 262: ...Appendix data sheets SCU Slaves ...
Страница 263: ...Appendix data sheets SCU Slaves ...
Страница 264: ...Appendix data sheets SCU Slaves ...
Страница 265: ...Appendix data sheets SCU Slaves ...
Страница 266: ...Appendix data sheets SCU Slaves ...
Страница 267: ...Appendix data sheets SCU Slaves ...
Страница 268: ...Appendix data sheets SCU Slaves ...
Страница 269: ...Appendix data sheets SCU Slaves ...
Страница 270: ...Appendix data sheets SCU Slaves ...
Страница 271: ...Appendix data sheets SCU Slaves ...
Страница 272: ...Appendix data sheets SCU Slaves ...
Страница 273: ...Appendix data sheets SCU Slaves ...
Страница 274: ...Appendix data sheets SCU Slaves ...
Страница 275: ...Appendix data sheets SCU Slaves ...
Страница 276: ...Appendix data sheets SCU Slaves ...
Страница 277: ...Appendix data sheets SCU Slaves ...
Страница 278: ...Appendix data sheets SCU Slaves ...
Страница 279: ...Appendix data sheets SCU Slaves ...
Страница 280: ...Appendix data sheets SCU Slaves ...
Страница 281: ...Appendix data sheets SCU Slaves ...
Страница 282: ...Appendix data sheets SCU Slaves ...
Страница 283: ...Appendix data sheets SCU Slaves ...
Страница 284: ...Appendix data sheets SCU Slaves ...
Страница 285: ...Appendix data sheets SCU Slaves ...
Страница 286: ...Appendix data sheets SCU Slaves ...
Страница 287: ...Appendix data sheets SCU Slaves ...
Страница 288: ...Appendix data sheets SCU Slaves ...
Страница 289: ...Appendix data sheets SCU Slaves ...
Страница 290: ...Appendix data sheets SCU Slaves ...
Страница 291: ...Appendix data sheets SCU Slaves ...
Страница 292: ...Appendix data sheets SCU Slaves ...
Страница 293: ...Appendix data sheets SCU Slaves ...
Страница 294: ...Appendix data sheets SCU Slaves ...
Страница 295: ...Appendix data sheets SCU Slaves ...
Страница 296: ...Appendix data sheets SCU Slaves ...
Страница 297: ...Appendix technical data SCU series Dimension Drawing ...
Страница 298: ...Appendix technical data SCU series Dimension Drawing ...
Страница 299: ...Appendix technical data SCU series Dimension Drawing ...
Страница 300: ...Appendix technical data SCU series Dimension Drawing ...
Страница 301: ...Appendix technical data SCU series Dimension Drawing ...
Страница 302: ...Appendix technical data SCU series Dimension Drawing ...
Страница 303: ...Appendix technical data SCU series Dimension Drawing ...