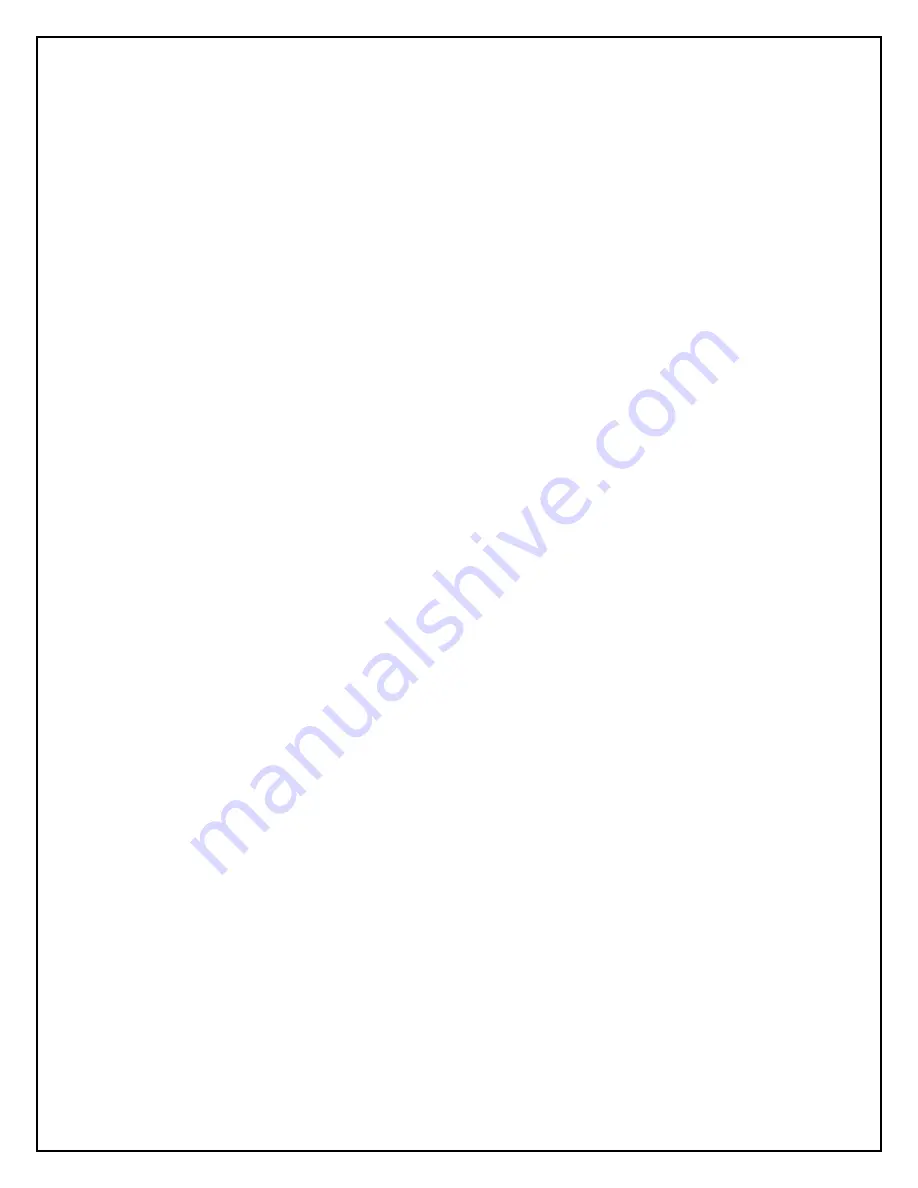
Microseparator™ Coolant Systems Transport, Installation, & Initial Startup
M000005_A - V Twin Ultra Transport & Installation 5.2-EN TM
63/78
20
Chip Separator with Tank – Short 6SIGD001
20.1
Principles of Operation
The Chip Separator with Tank is designed to separate large milling chips
from process coolant, discharge the chips automatically, and transfer the
process coolant and remaining small debris to the Microseparator™
system positioned remotely. One pneumatically activated scraping
armature periodically scrapes the internal screen conveying the chips
upwardly through the draining chamber. Chips are ultimately discharged
from the end of the assembly by following chip debris. Mounted to the
deck of the tank is a vertical centrifugal pump assembly that is activated
by a level control mechanism while maintaining a liquid level sufficient to
maintain submersion of the pump impeller housing and prime.
20.2
Limits of Operation
The Chip Separator with Tank has the capacity for one wet cut lens
generator processing organic lens materials – mineral glass is not
recommended.
The distance from the Chip Separator to the remote Microseparator™
coolant system is limited by the specifications contained in the Piping
Installation Diagram provided with the equipment – typically the
limitation is piping overhead at a maximum of 15’ (4.5m) of elevation and
a maximum lateral, downwardly sloping piping run of 50’ (15.25m).
The Chip Separator was developed primarily for conventional process
generators using milling cutters. Generators utilizing lathe tools for the
surfacing step cannot be serviced by the Chip Separator due to the length
and geometry of the waste material.
The more modern generators performing both milling and turning steps
(cut to to polish or free-form) utilize a milling cutter for the surfacing step
and lathe tools to finish the lens. In the case of polycarbonate and some
high-index lenses finished in this manner, a long strand (as much as 140’
/(42m) of hair like debris is created. This material can occasionally
become entangled with the pneumatic armature requiring operators to
manually clear the material to avoid clogging of the assembly. Timer
settings controlling actuation of the armature can be optimized to limit
the effect of this condition. The Pump Station described in this document
is a product ideally suited to generators of this type due to the ability of
the device to alter the characteristics of the long strands making them
easier to process in installations of the Microseparator™ systems.
Performance of the Chip Separator with Tank can be adversely affected
by failure to follow the instructions contained in the Installation Piping
Diagrams.