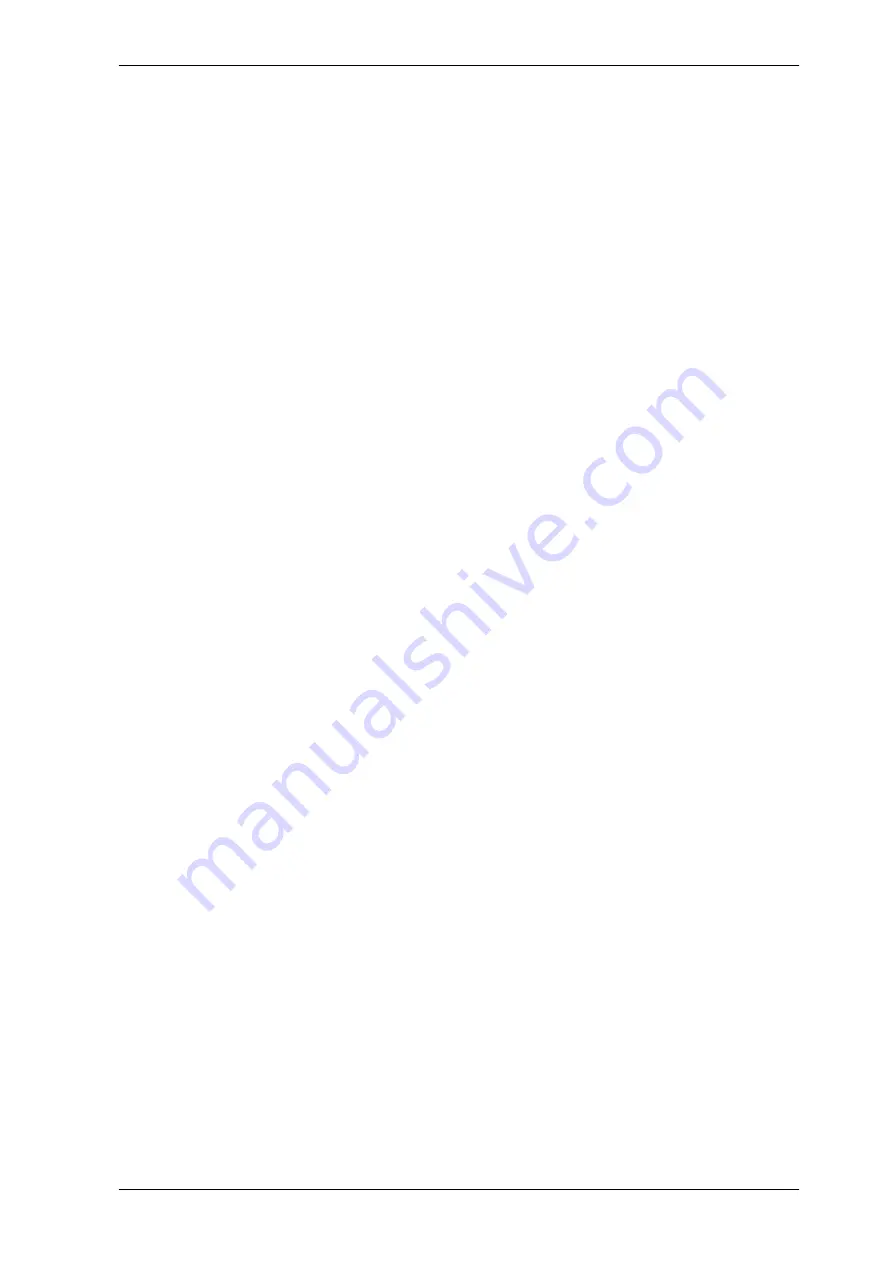
Installation
Mono Power Unit BUM 62 T
33
Baumüller Nürnberg GmbH
5.99009.03
6.4
Safety relay
In this chapter we describe the safety relay.
6.4.1 Methods to avoid an unexpected starting
In order to avoid hazards against persons, for example operators, service- and maintenance technics,
the machine has to be kept in a secure condition (safe stop), while interfering in the hazardous area of
the machine. That is why a reliable prevention of an unexpected starting is demanded (amongst other
things Machine directive 89/392/EWG, appendix I, 1.6.3, last passage; EN 292-2, 4.1.4; EN 60204-1,
5.4). Under unexpected starting is to be understood every starting that can cause a risk when appearing
unexpected for persons (EN 292-1). Moreover, besides the transition of the release- to the operating
condition of the machine also the unexpected ramp-up of the machine, this means the transition from
the safe stop into an unsafe moving has to be considered. This is necessary, because the unexpected
ramp-up usually is to be led back to an interruption of the control loop of the machine. In this case the
drive is, because of its control system, anxious to achieve highest speed at maximal acceleration. If an
unexpected starting occurs, the operator therefore doesn’t have the possibility anymore to remove him-
self or his hand from the hazard area. This is why the drive has to be stopped and has to be kept safe
in its ’off-position’, when having opened, electrical interlocked safety devices. The motor may not have
torque and thus cannot generate a dangerous movement.
The prevention of an unexpected starting of the machine can be reached by electrical separated safety
devices, e.g. contactors. By some machine types it has to be done without the isolation of the electrical
connection of the drive to the mains, if e. g. a drive supplied by a power converter is often stopped and
started again. The constant dis- and re-charging of the DC-link represents a big stress for the concerned
parts and often leads to disturbing delays and failures of these parts.
The requirement for the starting of a three-phase a. c. motor is the generation of a rotating field, which
drives the inductor of the motor. When having variable-speed three-phase current drives, usually in the
micro-processors a complex pulse pattern is generated, then the pulses are amplified and are used for
the switching of the power semiconductors. If either no defined pulse pattern is available or the amplify-
ing connection is interrupted, e. g. by switching off of the power supply with a relay (safety relay), no
rotary field can be generated. An error by the pulse pattern generation therefore cannot lead to a starting
of the motor, as long as the second condition, namely the interruption of the amplifying power supply is
available and contrary. The protection against unexpected starting is reached by an electromechanical
method which is superior to the electronics. It is reached by a safe isolation - elsewhere than in the load
circuit.
The power supply to the windings of the motor is reached at a stoppage by inhibiting the power semi-
conductor. As semiconductors possibly can fail or be started, because of electromagnetic disturbances,
the behavior of the shut down drive has to be considered if such a fault scenario arises. The fail or "ac-
cidental" turning on of a single or of more power semiconductors at the same DC-link pole does not lead
to an uncontrolled starting, as no current flow is accomplished. Not until additionally a further power
semiconductor is enabled at another DC-link pole, current is able to flow through the motor. If, thereby
the DC-link is directly short-circuited, the fuses which are upstreamed to the converter are tripped, the
motor doesn’t start. If the DC-link is "short-circuited" over a winding of the motor, a magnetic field can be
set up in the motor. If it is an asynchronous motor, then the generated d. c. magnetic properties cannot
cause a lurch of the inductor. By the permanent-magnetic synchronous motor the inductor will rotate into
a notch position. The therewith angular movement which is covered is dependable of the inductor’s po-
sition and the number of pole pairs of the motor. It amounts to maximal 180°/number of pole pairs. Sub-
sequently the enabled DC-link operates like a brake, this means after the ending of the lurching
movement the drive is in a blocked condition. A starting of the drive is impossible. If a machine with a
synchronous motor is planned, the possible sudden movement must be considered, because it can lead
to a dangerous movement. Therefore the machinist must carry out a safety evaluation for the residual
movement.
Содержание BUM 62 T
Страница 1: ...E 5 99009 03 Manual BUM 62 T Mono Power Unit ...
Страница 6: ...6 Mono Power Unit BUM 62 T 5 99009 03 Baumüller Nürnberg GmbH ...
Страница 10: ...Safety notes 10 Mono Power Unit BUM 62 T 5 99009 03 Baumüller Nürnberg GmbH ...
Страница 16: ...Technical data 16 Mono Power Unit BUM 62 T 5 99009 03 Baumüller Nürnberg GmbH 3 3 Block diagram ...
Страница 18: ...Transportation Unpacking 18 Mono Power Unit BUM 62 T 5 99009 03 Baumüller Nürnberg GmbH ...
Страница 21: ...Assembly Mono Power Unit BUM 62 T 21 Baumüller Nürnberg GmbH 5 99009 03 Installation Dismantling ...
Страница 22: ...Assembly 22 Mono Power Unit BUM 62 T 5 99009 03 Baumüller Nürnberg GmbH ...
Страница 39: ...Installation Mono Power Unit BUM 62 T 39 Baumüller Nürnberg GmbH 5 99009 03 6 5 Connection diagram ...
Страница 48: ...Installation 48 Mono Power Unit BUM 62 T 5 99009 03 Baumüller Nürnberg GmbH ...
Страница 62: ...Commissioning 62 Mono Power Unit BUM 62 T 5 99009 03 Baumüller Nürnberg GmbH ...
Страница 66: ...Maintenance 66 Mono Power Unit BUM 62 T 5 99009 03 Baumüller Nürnberg GmbH ...
Страница 73: ......