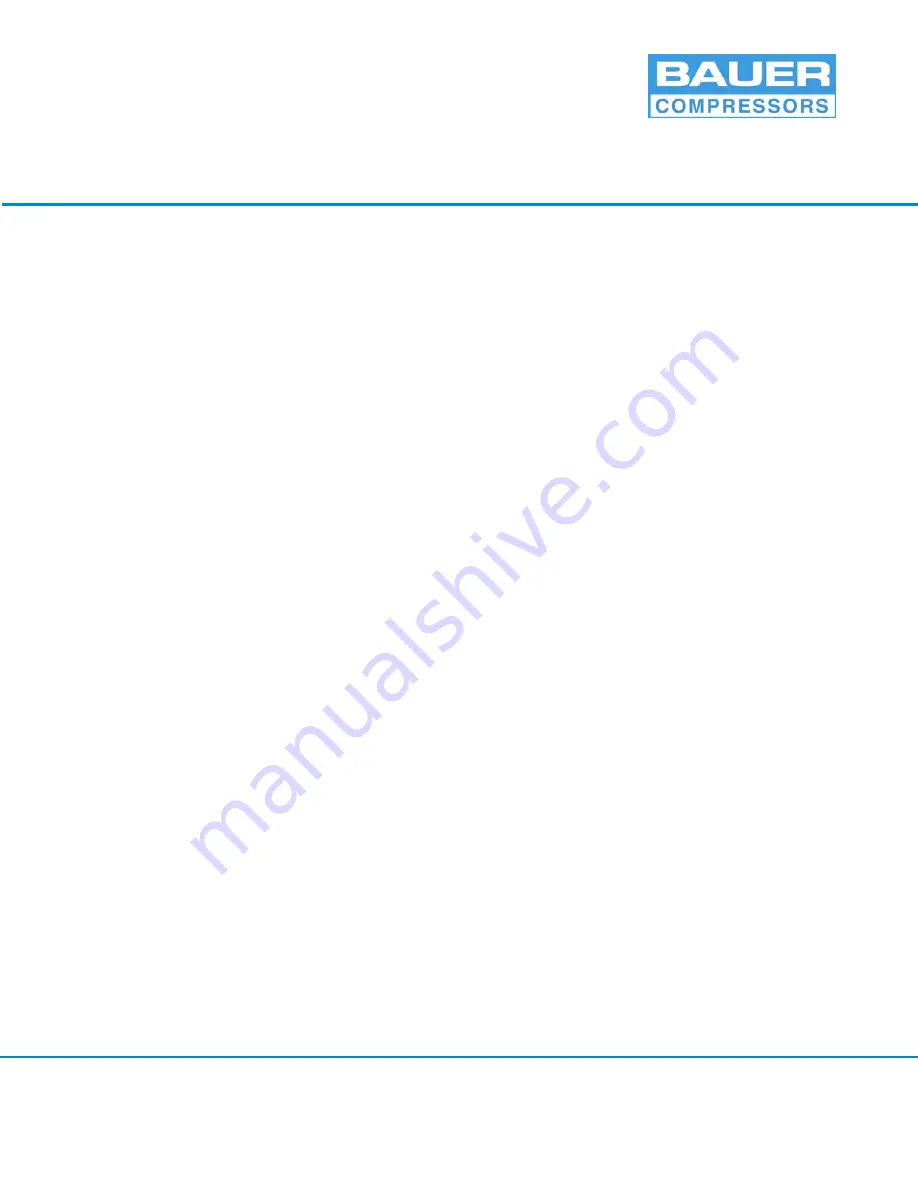
Instruction Manual and Replacement Parts List
BAUER Compressors, Inc.
Phone: (757) 855-6006
1328 Azalea Garden Road
Fax: (757) 855-6224
Norfolk, Virginia 23502-1944
www.bauercomp.com
April 17, 2013
3rd Edition, Rev 0 Chg 6
MNL-0096
© Bauer Compressors, Inc.
Breathing Air Purification Systems
and
Industrial Air Purification Systems
Breathing Air Purification Models
P0
P1
P2
P4
P5
P10
P31
P41
P42
P43
with Securus
®
Electronic Moisture Monitor System
P2S
P5S
P10S
P14S
P42S
P43S
P12
P14
Industrial Air Purification Models
IP41
IP42
IP43
with Securus
®
Moisture Monitoring System
IP2S
IP5S
IP10S
IP41S
IP42S
IP43S