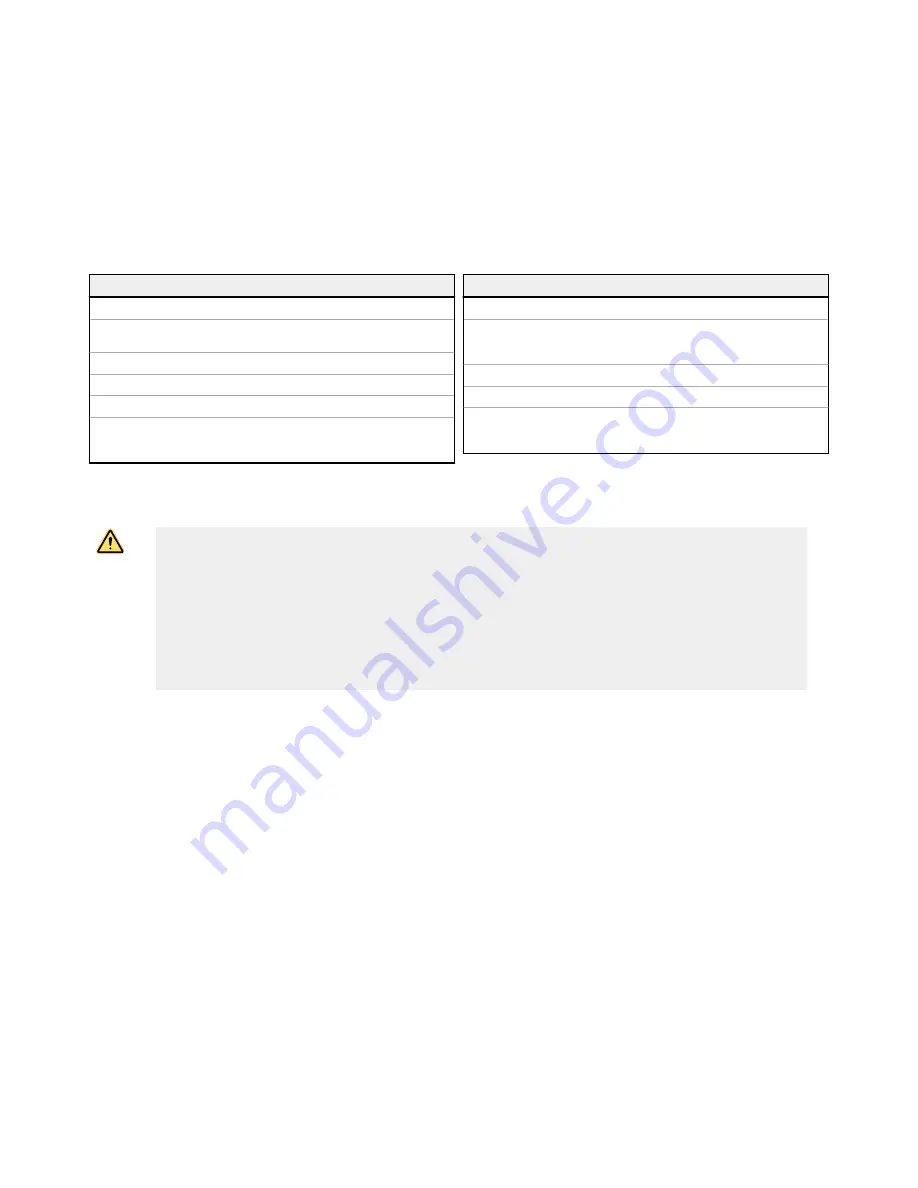
Notes:
1. The OSHA-recommended hand speed constant K has been determined by various studies and, although
these studies indicate speeds of 1600 mm/sec. (63 in/sec.) to more than 2500 mm/sec. (100 in/sec.), they
are not conclusive determinations. Consider all factors, including the physical ability of the operator, when
determining the value of K to be used.
2. The recommended hand speed constant K, derived from data on approach speeds of the body or parts of
the body as stated in ISO 13855.
3. Ts is usually measured by a stop-time measuring device. If the machine manufacturer's specified stop time
is used, at least 20% should be added to allow for possible clutch/ brake system deterioration. This
measurement must take into account the slower of the two MPCE channels, and the response time of all
devices or controls that react to stop the machine.
US Application example: Model SLLVP23-560
K = 63 in per second
Ts = 0.32 (0.250 seconds is specified by the machine manufacturer; plus
20% safety factor; plus 20 ms interface module IM-T-9A response)
Tr = 0.0116 second (the specified SLLVP23-560 response time)
Dpf = 2.14 in (for 23 mm resolution)
Ds = 63 × (0.32 + 0.0116) + 2.14 = 23 in
Mount the EZ-SCREEN LS Basic emitter and receiver so that no part of
the defined area is closer than 23 inches to the closest reachable hazard
point on the guarded machine.
European Application example: Model SLLVP23-560
K = 1600 mm per second
T = 0.3316 (0.250 seconds is specified by the machine manufacturer;
plus 20% safety factor; plus 20 ms interface module IM-T-9A response),
plus 0.0116 seconds (the specified SLLVP23-560 response time)
C = 8 × (23 - 14) = 72 mm (for 23 mm resolution)
S = (1600 × 0.3316) + 72 = 603 mm
Mount the EZ-SCREEN LS Basic emitter and receiver so that no part of
the defined area will be closer than 602 mm to the closest reachable
hazard point on the guarded machine.
WARNING: Determine Correct Stop Time
Stop time (Ts) must include the response time of all devices or controls that react to stop the machine. If
all devices are not included, the calculated safety distance (Ds or S) will be too short. Failure to follow
these instructions could result in serious injury or death. Be sure to include the stop time of all relevant
devices and controls in your calculations.
If required, each of the two Machine Primary Control Elements (MPCE1 and MPCE2) must be capable of
immediately stopping the dangerous machine motion, regardless of the state of the other. These two
channels of machine control need not be identical, but the stop time performance of the machine (Ts,
used to calculate the safety distance) must take into account the slower of the two channels.
5.1.2 Reducing or Eliminating Pass-Through Hazards
A
pass-through
hazard is associated with applications where personnel may pass through a safeguard, such as the EZ-
SCREEN LS Basic Safety Light Screen (which issues a stop command to remove the hazard), and then continues into the
guarded area. This is common in access and perimeter guarding applications. Subsequently, their presence is no longer
detected, and the related danger becomes the unexpected start or restart of the machine while personnel are within the
guarded area.
In the use of light screens, a pass-through hazard typically results from large safety distances calculated from long stopping
times, large minimum object sensitivities, reach-over, reach-through, or other installation considerations. A pass-through
hazard can be generated with as little as 75 mm (3 in) between the sensing field and the machine frame or hard (fixed)
guarding.
Eliminate or reduce pass-through hazards whenever possible. While it is recommended to eliminate the pass-through
hazard altogether, this may not be possible due to machine layout, machine capabilities, or other application
considerations.
One solution is to ensure that personnel are continually sensed while within the hazardous area. This can be accomplished
by using supplemental safeguarding, such as described by the safety requirements in ANSI B11.19 or other appropriate
standards.
An alternative method is to ensure that once the safeguarding device is tripped it will latch and will require a deliberate
manual action to reset. This method of safeguarding relies upon the location of the reset switch as well as safe work
practices and procedures to prevent an unexpected start or restart of the guarded machine. The EZ-SCREEN LS Basic
Safety Light Screen provides a configurable Manual Start/Restart (Latch Output) function for these applications.
EZ-SCREEN
®
LS Basic Safety Light Screen
22
www.bannerengineering.com - Tel: 763.544.3164