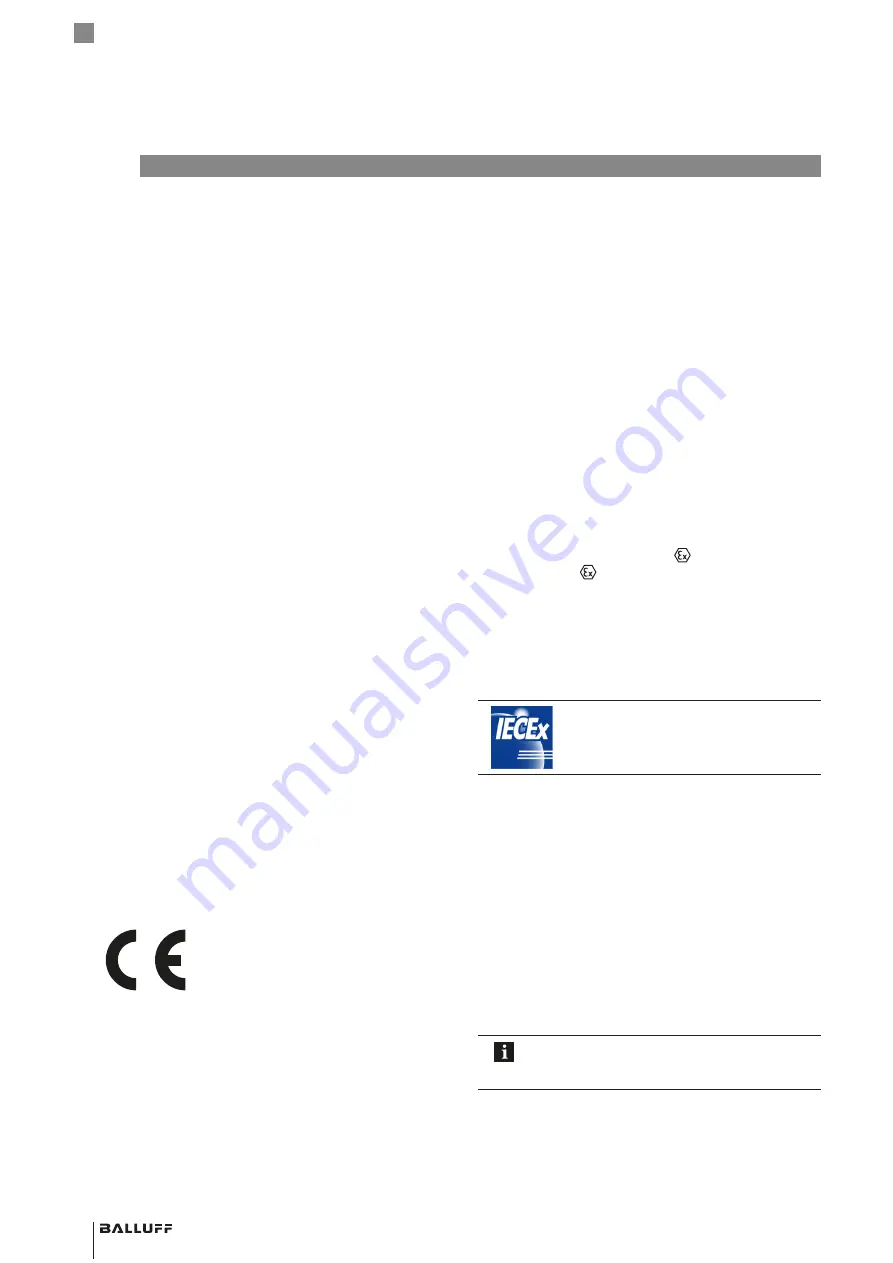
6
english
Ignition protection
“nA” and “tb”
2.1
Intended use
In line with its identification, this micropulse transducer is
suitable as electrical equipment for use in gas and dust
explosive areas. When installed in a machine or system,
the transducer forms a position measuring system in
conjunction with a controller or evaluation unit and may
only be used for this purpose.
When selecting the electrical equipment, the person
setting up the machine or system is responsible for
assessing its suitability for the planned area of application.
The information in the user’s guide and other applicable
safety regulations and provisions must be observed during
set-up. Flawless function is ensured only when using
original BALLUFF accessories. Use of any other
components will void the warranty.
The operator of the machine or system must ensure that
the transducer is applied under the permissible operating
conditions in line with the information in this user’s guide
and in compliance with the applicable safety regulations
and provisions.
Unauthorized interventions, non-permissible use, or
application outside the permissible operating conditions
will result in the loss of warranty and liability claims against
the manufacturer.
2.2
Safety measures
The persons setting up and operating the machine or
system must take steps to ensure that a malfunction in the
transducer will not result in hazards to persons or
equipment. If there are any indications of damage or
malfunctions, the transducer must be immediately taken
out of operation and secured against unauthorized use.
Even with correct explosion protection, residual risks
remain that could pose a hazard to persons and systems
when the device is correctly operated or if there are any
fault states.
2.3
Approvals, standards, and conformity
The CE Mark verifies that our products
meet the requirements of the current
EMC Directive as well as the ATEX
Directive. Compliance is confirmed with
the enclosed declaration of conformity
from the manufacturer.
The transducer meets the requirements of the following
product standard:
– EN 61326-2-3 (noise immunity and emission)
Emission tests:
– RF emission
EN 55011
Noise immunity tests:
– Static electricity (ESD)
EN 61000-4-2
Severity level 3
– Electromagnetic fields (RFI)
EN 61000-4-3
Severity level 3
– Electrical fast transients (burst)
EN 61000-4-4
Severity level 3
– Surge
EN 61000-4-5
Severity level 2
– Conducted interference induced
by high-frequency fields
EN 61000-4-6
Severity level 3
– Magnetic fields
EN 61000-4-8
Severity level 4
The transducer with identification
II 3 G Ex
nA IIC T4 X
and
II 2 D Ex tb IIIC T135 °C X IP6x
fulfills the requirements for electrical equipment for
explosive areas in accordance with the following
standards:
– EN 60079-0: General requirements
– EN 60079-15: Ignition protection “n”
– EN 60079-31: Ignition protection “t”
In addition to the ATEX requirements, the
transducer has been authenticated under
certificate number
IECEx EPS 13.0004 X
.
The current status of the certificate and further information
can be found under www.iecex.com in the “Certified
Equipment Scheme” section. The certificate number is
indicated on the part label.
Further applicable safety regulations and standard
requirements must be observed during selection, set-up,
and operation:
– Special conditions for safe operation (“X” symbol)
– Requirements for occupational safety
– Requirements for explosion protection
– Electrical installations erection in explosive
atmospheres (DIN EN 60079-14)
– Further regulations
More detailed information on the guidelines,
approvals, and standards is included in the
declaration of conformity.
2
ATEX safety notes
BTL7-A/C/E/G5 _ _ -M _ _ _ _ -K(8)-NEX-SR32/K_ _ _
Micropulse Transducer - Rod Style
Содержание BTL7-A5 Series
Страница 2: ...www balluff com ...