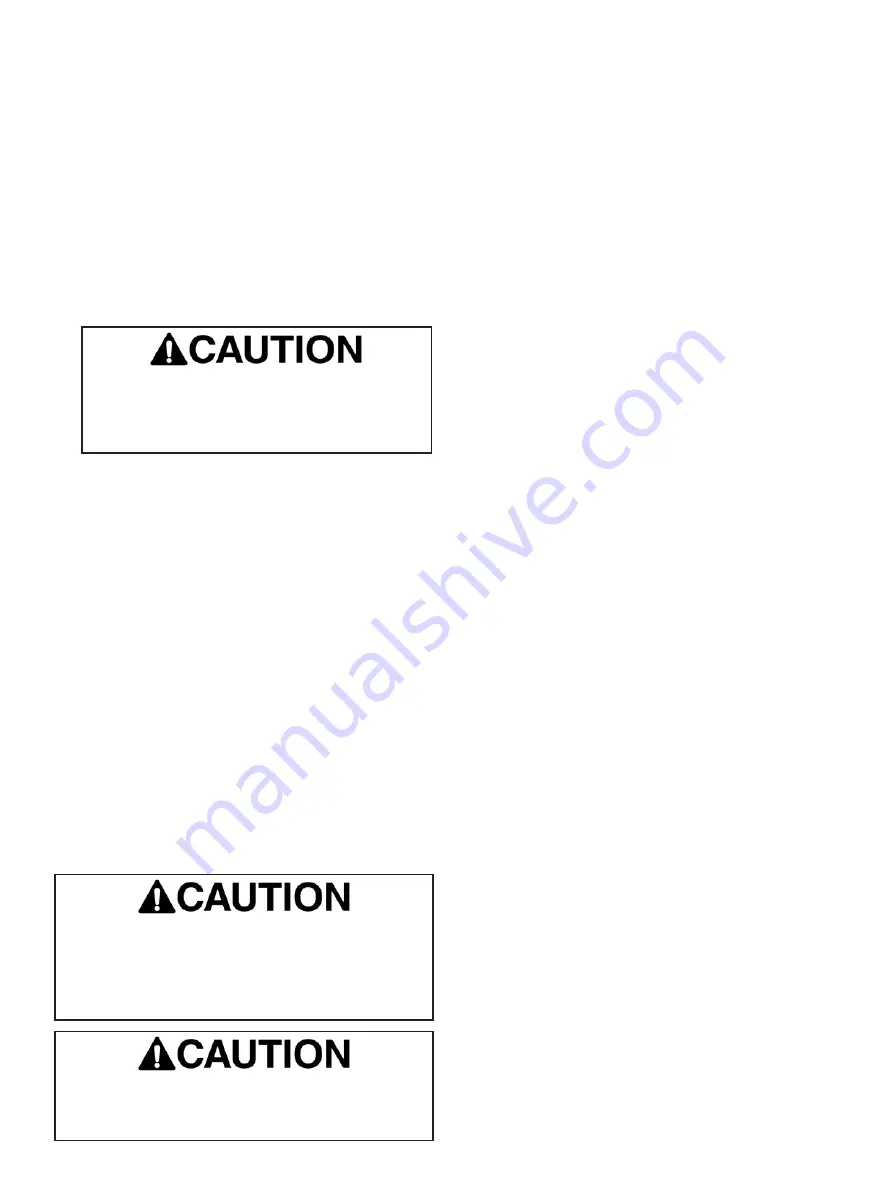
Masoneilan 77000 Series Control Valves Instruction Manual | 5
Copyright 2021 Baker Hughes Company. All rights reserved.
10. Remove the bonnet nuts (10) and pressing down on the
stem remove the top entry bonnet (2) from the valve body
(1). While removing the bonnet the old packing set (11) and
lantern ring (12) may also pull away from the stem. These
parts should be removed at this time.
Note: Lantern ring is applicable only for units with the
optional leak detector option.
11. Remove the bonnet gasket (34) and upper stem guide
bushing (6) from the valve body.
12. Using the threaded lifting holes and eye bolts remove the
seat ring retainer (33) from the valve body.
13. Using the threaded lifting holes and eye bolts carefully lift
the seat ring (3) from the valve body while paying close
attention to not damage the plug stem (5) or seat ring (3)
parts. Next remove the plug stem (5).
Be careful not to damage the plug stem (5) or the
seat ring (3) while removing these parts from the
body. Scratches or damage to these parts can
result in leakage and premature wear.
14. Remove the lower guide bushing (35), spider (4), upper
spider gasket (8), and lower spider gasket (7) from the valve
body.
15. Inspect the body (1), bonnet (2), seat ring (3), spider (4), and
plug stem (5) for any visual defects or damage. Carefully
inspect the dynamic sliding surfaces and seal interface
areas.
Ensure all parts are clean, particularly the seating surfaces
prior to reassembly.
Maintenance & Repair
The purpose of this section is to provide recommended
maintenance and repair procedures. These procedures assume
the availability of standard shop tools and equipment.
Packing Box
Packing box maintenance is one of the principal tasks during
routine service. Tightness of the packing set (11) is maintained
by proper compression. Compression is achieved by evenly
tightening the packing flange nuts (16) against the packing
flange (14). Periodic re-tightening of the packing flange nuts may
be required to maintain proper sealing,
Care must be taken to not over tighten, as this could
create unnecessary friction preventing smooth valve
operation. If packing leakage persists after applying
maximum compression, then the packing needs to be
replaced.
The valve must be isolated and the process pressure
vented prior to performing any packing box mainte
-
nance.
Packing Replacement
For top entry designs, disassembly of the valve bonnet from
the body is recommended before replacing the standard Teflon
V-Ring packing.
Other packing types can be replaced without removal of the
bonnet.
Use the following procedures to replace existing packing:
1. Loosen and remove the packing flange nuts (16).
2. Remove the packing flange (14) and packing follower (13).
3. Remove the old packing set (11) and lantern ring (12).
Note: Lantern ring is applicable only for units with the
optional leak detector option.
4. Replace packing (11) and lantern ring (12) if applicable,
referring to Figures 4 through 9 for correct number of packing
rings.
Note: For Teflon packing, assemble new packing with
the cuts in the rings 120° apart from the adjacent ring.
Press rings into the packing box one at a time.
5. Reassemble the packing follower (13) and the packing
flange (14).
6.
Tighten the packing flange nuts (16) without over
compressing the packing rings.
7. For graphite packing, open and close the valve several
times then retighten the packing as required.
8. Place the valve back into service and check for leakage.
Tighten packing flange nuts (16) as required.
Parts Repair
Carefully examine parts for any scratches, unusual wear, or
other visual damage prior to reassembly. Always clean trim parts
before reinstalling in the valve.
Guiding Surfaces
Guiding Surfaces including the upper stem guide bushing (6),
plug stem (5), and lower guide bushing (35) available on the top
entry design or spider guide (4) as shown on the bottom entry
design must be checked. If there is only slight wear indications,
then use a light abrasive to smooth out the specific guiding
surface areas. Parts with greater damage or wear on the guide
surfaces must be replaced.
Guiding surfaces are hard-coated and excessive removal of
surface material can expose base material.
Seating Surfaces
The seat ring (3) and plug stem (5) seating surfaces shown in
Figure 1 must be completely free of dents, scratches, wear,
or other visual damage. If the valve demonstrates excessive
leakage or shows signs of deterioration on the seating surfaces
the parts may be refurbished in accordance with the following
guidelines.
Seat Lapping
Seating surfaces may need to be lapped in order to restore the
necessary surface integrity to meet valve leakage requirements.
Prior to lapping ensure the plug and seat ring seating surfaces
are free from large scratches or dents. Remachining of these
surfaces may be necessary. If so a maximum of .015” (0.4mm)