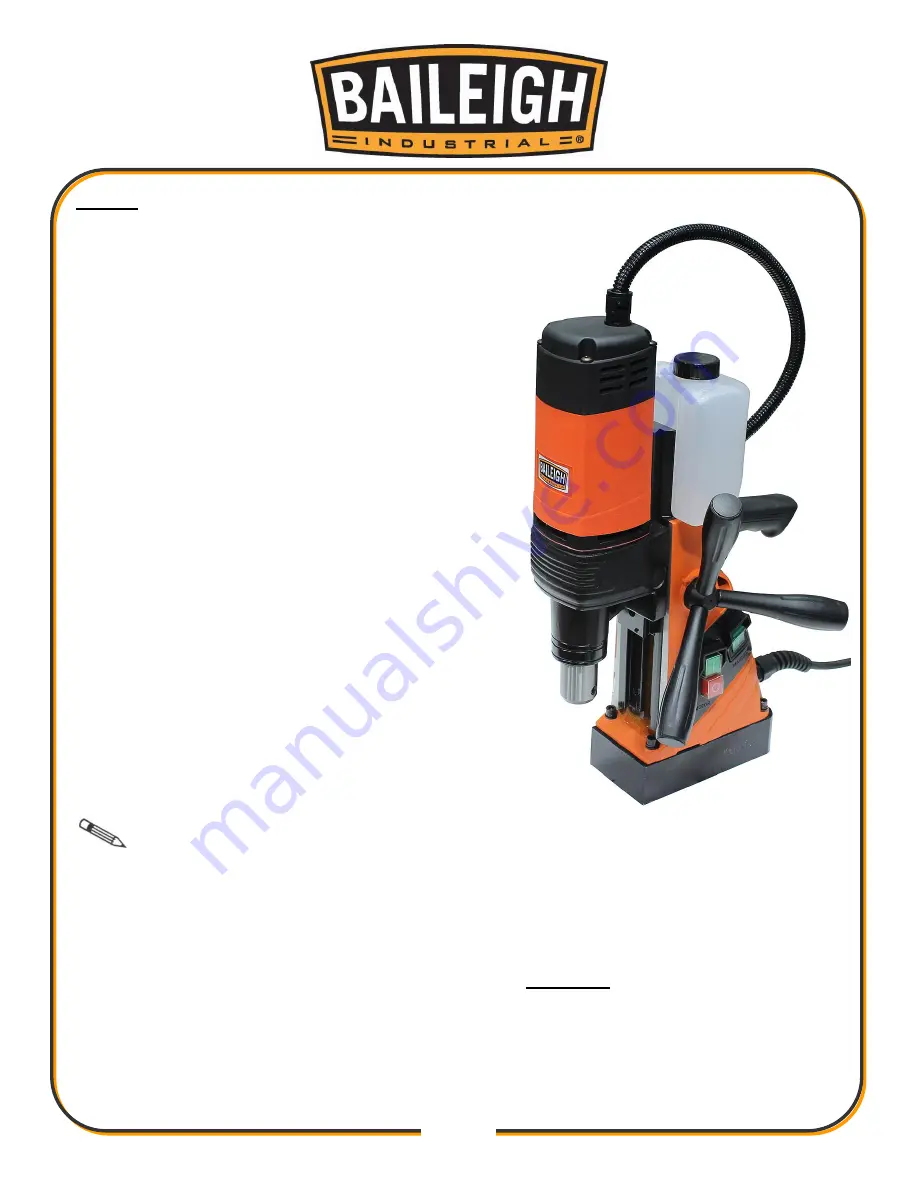
19
19
Drilling
This machine is designed specifically for drilling holes
in mild steel using the appropriate cutters and
accessories. It should not be modified or used for any
application other than for which it was intended,
including powering other equipment.
Ensure that the total work area can be viewed from the
operating position. Use barriers to keep people away.
•
Check that the coolant level and the feed rate are
sufficient to complete the hole to be drilled.
a. It is recommended to always use coolant.
However;
b. Coolant from the feed bottle should not be
used if the drill is being used on any
application where the drill chuck is horizontal
or in any upward angle. The coolant will
drain back into the drill body and damage
the drill. This is not covered under warranty.
In these applications it is recommended to
use a separated spray mist coolant rather
than a flood coolant.
Install the desired bit or cutter for the operation.
Verify that the magnet is clean and free of metal chips
and other dirt and debris. These will seriously reduce
the magnetic adhesion.
IMPORTANT:
The drill’s magnetic adhesion depends on the thickness of the work
piece.
0.5
9” – 1.96” (15 – 50mm)
is optimum thickness for safe operation. If the material is less
than 0.5
9” (15mm) thick, the material may not produce enough magnetic adhesion. In some
cases, adding a backer plate under the magnet on the back side of the work piece may
•
Position the drill to center the tool over the cut location.
•
Secure the drill from falling by using the safety strap.
ALWAYS!
•
Switch on the magnet and check that the cutter is still in the correct position and the machine
is securely held to the work piece.
Ensure that the magnet has adhered to the work piece firmly before switch on the drill.
Always use the supply safety strap.
Содержание MD-3510
Страница 13: ...11 11 GETTING TO KNOW YOUR MACHINE...
Страница 25: ...23 23 DRILL PARTS DIAGRAM...
Страница 26: ...24 24...
Страница 30: ...28 28 NOTES...
Страница 31: ...29 29 NOTES...