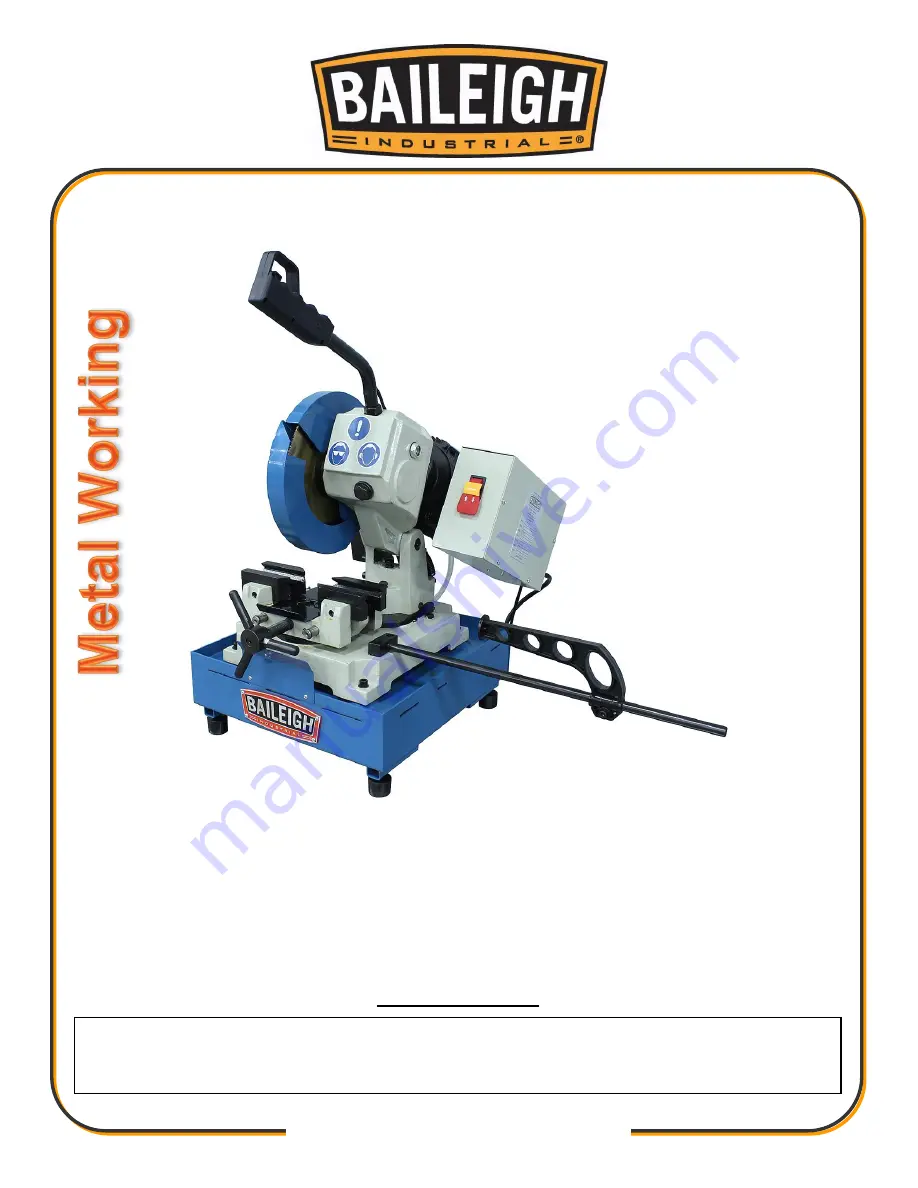
OPERATOR’S MANUAL
MANUAL COLD SAW
MODEL: CS-225M-V2
© 2020 Baileigh Industrial Holdings LLC
REPRODUCTION OF THIS MANUAL IN ANY FORM WITHOUT WRITTEN APPROVAL OF BAILEIGH INDUSTRIAL
HOLDINGS LLC IS PROHIBITED. Baileigh Industrial Holdings LLC, Inc. does not assume and hereby disclaims any
liability for any damage or loss caused by an omission or er
ror in this Operator’s Manual, resulting from accident,
negligence, or other occurrence.
Rev. 03/2020
Baileigh Industrial Holdings LLC
P.O. Box 531
Manitowoc, WI 54221-0531
Phone: 920.684.4990
Fax: 920.684.3944
Содержание CS-225M-V2
Страница 16: ...14 14 OVERALL DIMENSIONS Machine Dimensions when assembled 0 I REMOVE TO LOCK ...
Страница 28: ...26 26 BLADE SELECTION CHART ...
Страница 32: ...30 30 PARTS DIAGRAM ...
Страница 33: ...31 31 ...
Страница 43: ...41 41 NOTES ...