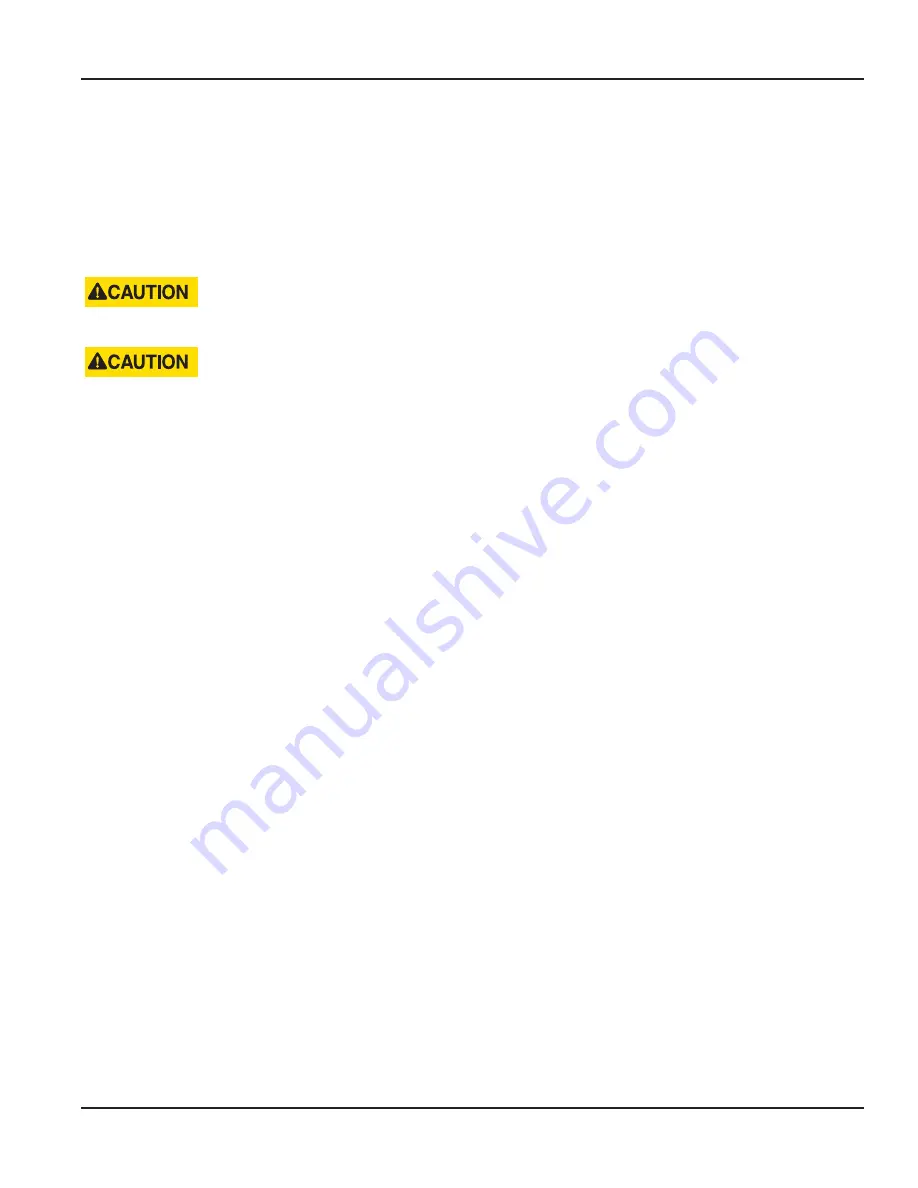
Line Installation
All flanged Gemini Cone meters require a gasket between the flange on the process line and the mating flange on the
meter itself Select gaskets that match the pressure and temperature ratings of the Gemini Cone flanges and resist corrosive
properties of the process fluid
Before completing the bolting process, make sure that the gaskets are properly centered so that protrusion into the pipe
opening is minimized Misalignment may cause added flow turbulence which can affect meter performance, although
such effects are typically minimal (depending upon the application) Bolt the element in line with suitable hardware using
recommended bolt torques for the type and class rating of the flanges
TORQUE ALL MODELS PER ANSI FLANGE RATINGS.
DO NOT EXCEED SPECIFIED TORQUE.
OTEE:
N
Tighten the flange bolts in a progressive star pattern to avoid localized stress on the gaskets
Differential Pressure Connections
The high pressure connection is always on the upstream side of the flow direction arrow and the low pressure connection on
the downstream side Fittings used must be able to withstand the process temperature and pressure conditions, as well as
provide proper corrosion resistance See the appropriate secondary instrument instructions for connections to the secondary
instrument high and low ports Coat all fitting threads with a process compliant thread sealant prior to tightening Once
tightened, torque mark all fittings for future reference
Transmitter Connection Tubing
Before connecting the Gemini Cone meter to the transmitter, consider the following tips for optimizing your system’s
measurement accuracy In a well-designed installation, fluids will drain freely from the process lines and gases will vent to
the atmosphere
Full Port Block Valves
Adding block valves to the pressure taps of the meter will simplify any type of calibration or maintenance to any upstream
components Select valves that are compatible to the pressures, temperatures and system media
Impulse Tubing Size Selection
Transmitter connection tubing, the tubing that connects the Gemini Cone meter taps to the transmitter, can vary in
diameter for different applications A minimum diameter of 3/8 inch (10 mm) for the internal diameter (ID) of the tubing is
recommended, and as a general rule it should be no smaller than 1/4 inch (6 mm) The tubing ID must not exceed 1 inch
(25 mm) at the maximum
In most applications, the primary concern is measurement reliability If the pressure taps or the connecting tubes become
plugged, the reliability of the flow measurement is lost creating a safety risk High reliability is required for any flow signals
used to manage safety processes A minimum tubing ID of 5/8 inch (16 mm) is recommended in industrial applications
For steam applications, the ID should be 3/8… 1 in (10…25 mm)
Straight Pipe Run Requirements
Page 11
June 2018
DPM-UM-00206-EN-03