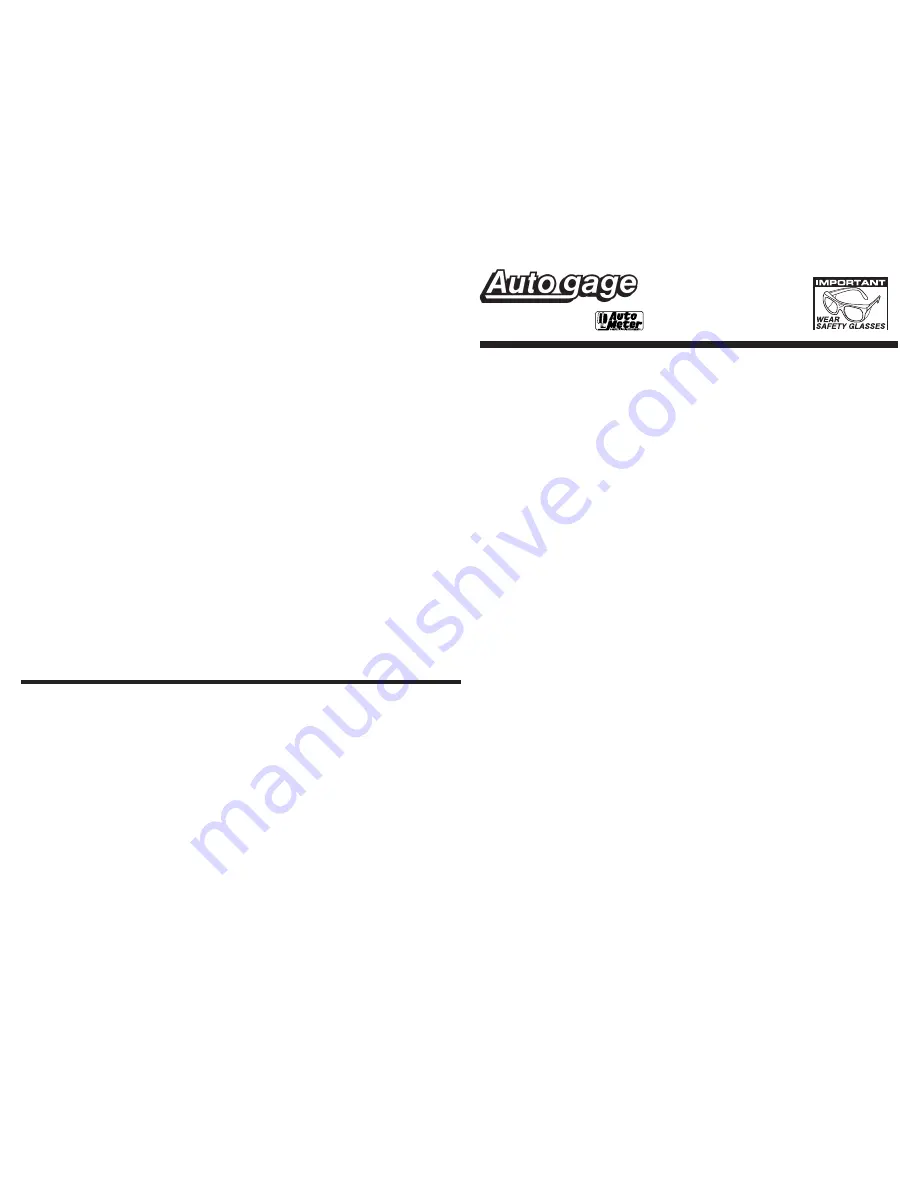
INSTALLATION
INSTRUCTIONS
by
2650-252X-10
®
2
5
⁄
8
"
Mechanical 3-Gauge Console
MODEL 2394, 2395
WARNING: Some late model vehicles use electronic sensors in their
pressure and temperature senders for engine control functions. Before
removing the original senders, we recommend that you contact your
automotive dealer to be sure no critical functions will be disrupted.
• For temperature gauges, Auto Meter temperature manifolds can be
plumbed directly into the cooling system in any convenient location.
Temperature sensing bulb can then be threaded into the temp.
manifold for accurate cooling system temperature readings.
• With pressure gauges, it is beneficial to add a T-fitting to install your
new gauge and to keep the warning light operational. This allows you
to monitor the pressure and still have a warning light to indicate
emergency conditions.
1. Read instructions thoroughly. Please consult a qualified mechanic if you have
not had training on the proper installation of instruments.
2. Consult your vehicle's repair manual to locate:
A) oil pressure port,
B) 12V ignition switch or fuse box, and
C) water temperature port
3. Determine ideal mounting location. Choose a location that will not obstruct
visibility or impair driving movement.
4. Determine the best route for tubing to follow. Choose a path free of hazards of
moving parts or hot engine components.
5. Assemble tools and parts required for installation.
6. Remove gauges from metal panel. Notice their placement to make
reassembly easier.
7. Disconnect negative (-) battery cable.
8. Hold panel in desired mounting location. Use panel as template and mark
holes to be drilled for mounting. (For mini consoles, use mounting brackets as
templates.)
9. Drill holes with a 9/64" drill bit and attach metal panel with self-tapping screws
provided.
For actual gauge installation, see further instructions inside.
Preliminary Steps
Final Procedures (For All Gauges)
1. Insert light bulb and socket assembly into back of each gauge. Connect all red lighting wires to 12V
power source in dash lighting circuit. This allows the gauge lights to be dimmed with normal dash
lighting and only used at night. Connect the black wires to good engine ground. (Body frame bolt is a
good engine ground.)
2. Reconnect negative (-) battery cable.
3.
For ammeters, turn on lights when engine is off. Ammeter indicator should read negative (-). If it
reads positive (+), reverse the red, 10-gauge wires on back of meter.
Before starting car, double check
that all connections are tight. After starting engine, check wiring connections for hot spots. Be
prepared to shut off
immediately if hot spots are detected.
4. Inspect all connections for leaks. Wrap a clean rag around fittings on back of oil pressure gauge and
place a pan on floor under them to protect vehicle interior from potential oil leaking. Start engine and
run for 30 seconds. Shut engine off and check rag for leaks. If none appear, start engine again and
visually check all connections for leaks.
1. Drill a 3/8" dia. hole in firewall. Install small
rubber grommet in firewall to insulate nylon
tubing where it passes through sheet metal.
2. Remove existing oil pressure sender (for
computerized vehicles, see warning on pg. 1).
Install 1/8" NPT adapter (with 7/16" open-end
wrench) in this location using sealing compound
on pipe threads. If 1/4" NPT adapter is needed,
install it first instead ( with 9/16" open-end
wrench). Be sure to hold 1/4" NPT adapter while
tightening 1/8" NPT adapter firm (with 7/16"
open-end wrench).
3. To help prevent leaks, be sure the end of nylon
tubing is cut cleanly and straight. Slide
compression nut onto tubing with threads
toward end of tubing. Slide ferrule onto end of
tubing, leaving 3/16" between ferrule and end of
tube. Insert end of tubing into 1/8" NPT adapter.
Apply pressure to maintain constant bond
between end of tubing and inside of adapter.
Slide ferrule into the adapter then compression
nut. Tighten compression nut (with 3/8" open-
end wrench) while holding 1/8" NPT adapter
firm (with 7/16" open-end wrench). To make
sure it is a snug fit, tug lightly on nylon tubing to
make sure it doesn't come out.
4. Route tubing through small grommet in firewall
and cut to meet mounted panel (leave one foot
of extra length before cutting). Be sure to avoid
potential hazard of moving parts or hot engine
components.
5. Secure gauge in mounted panel using non-
insulated mounting bracket.
6. Slide sealing nut and ferrule on this end of
tubing and tighten in the same manner
described in Step 4 (use 9/16" and 3/8" open-
ended wrenches).
Oil Pressure