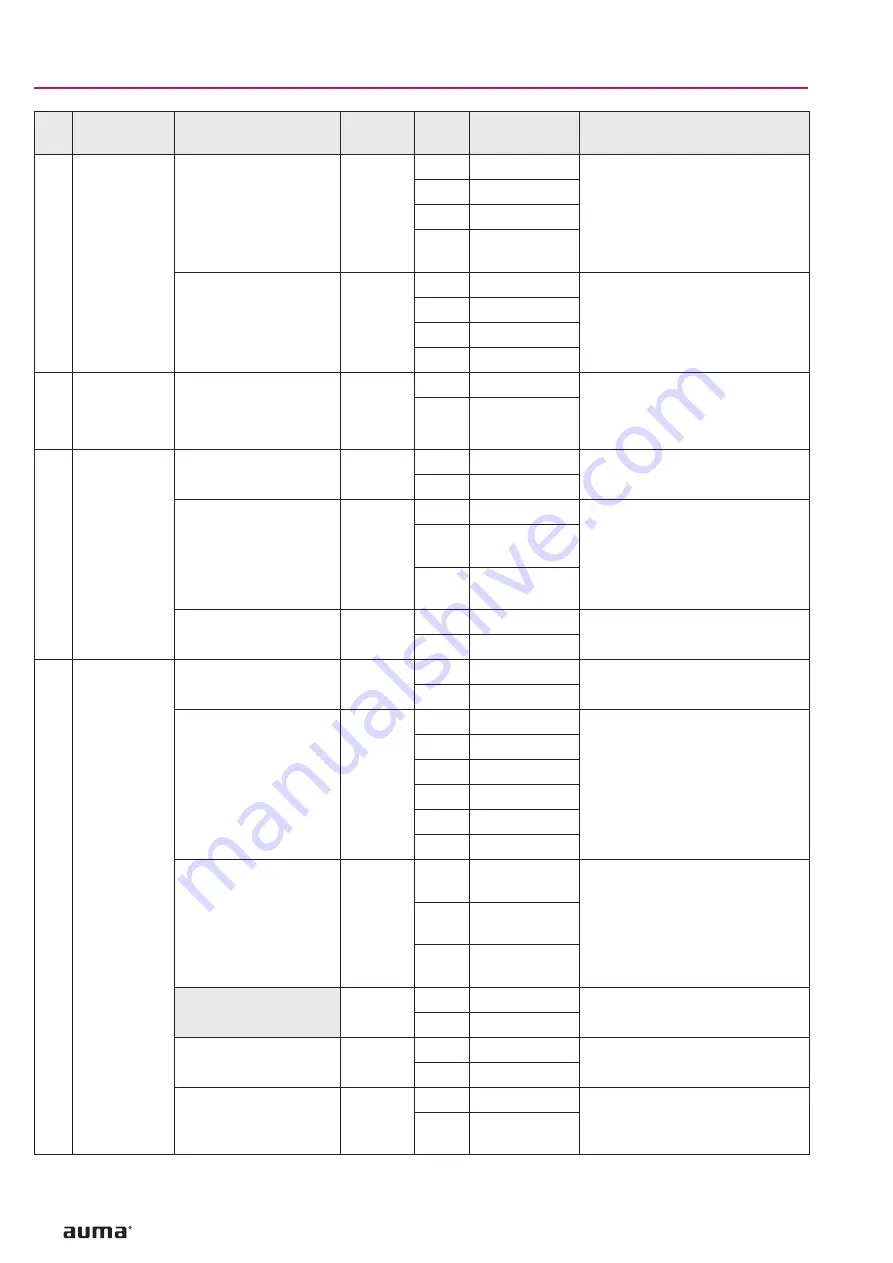
36
Part-turn actuators SG 03.3 – SG 04.3
with AUMATIC AC 01.1
Operation instructions
1) Only for actuators with Profibus DP 2) Only for actuators with Modbus
Subgroup
Parameter
name
Sub-
menu
Standard
value
Min/M
ax
Valuetext
Note
M1C
INTERMED.
POSITIONS
POS4:
SELECTOR SW.
M1CXE
0
0
OFF
Switch off intermediate position 4
or assign it to a specific operati-
on mode.
1
REMOTE ONLY
2
LOCAL ONLY
3
REMOTE AND
LOCAL
POS4:
CONTROL
M1CXF
0
0
NOT USED
Signal behaviour in intermediate
position 4 (see also page 56,
subclause 16.11)
1
C
_ _ _
POS¯¯¯O
2
C
_ _ _
POS¯¯¯O
3
C
_ _ _
POS¯¯¯O
M1D
CHANGE
PASSWORD
PASSWORD
M1DX0
0
0
Password (see also page 22);
can only be viewed and changed
after having entered the currently
valid password
1999
M1E
PROFIBUS
DP2
1)
SLAVE ADDRESS M1EX0
2
0
Slave address of the
DP2 sub-assembly
125
REDUNDANCY
M1EX1
0
0
OFF
DP2 bus redundancy
1
ON,TX:ACTIVE
CHANNEL
2
ON,TX:BOTH
CHANNELS
CHANNEL CHECK
TIME
M1EX2
5,0
5,0
DP2 channel check time (in s)
600.0
M1F
MODBUS 1
2)
BAUD RATE
M1FX1
5
0
300 BAUD
Modbus 1: Baud rate selection
1
600 BAUD
BAUD RATE
M1FX1
5
2
1200 BAUD
Modbus 1: Baud rate selection
3
2400 BAUD
4
4800 BAUD
5
9600 BAUD
6
19200 BAUD
7
38400 BAUD
PARITY
M1FX2
1
0
NO, 2 STOP-
BITS
Modbus 1: Parity selection
1
EVEN, 1 STOP-
BIT
2
ODD, 1 STOP-
BIT
CONNECT-
CONTROL TIME
M1F03
3,0
1,0
Modbus 1: connection control
time (in s)
25,5
SLAVE ADDRESS M1FX4
247
1
Modbus 1: Slave address
247
REDUNDANCY
M1FX5
0
0
OFF
Modbus 1: Redundancy behav-
iour
1
ON,TX:ACTIVE
CHANNEL