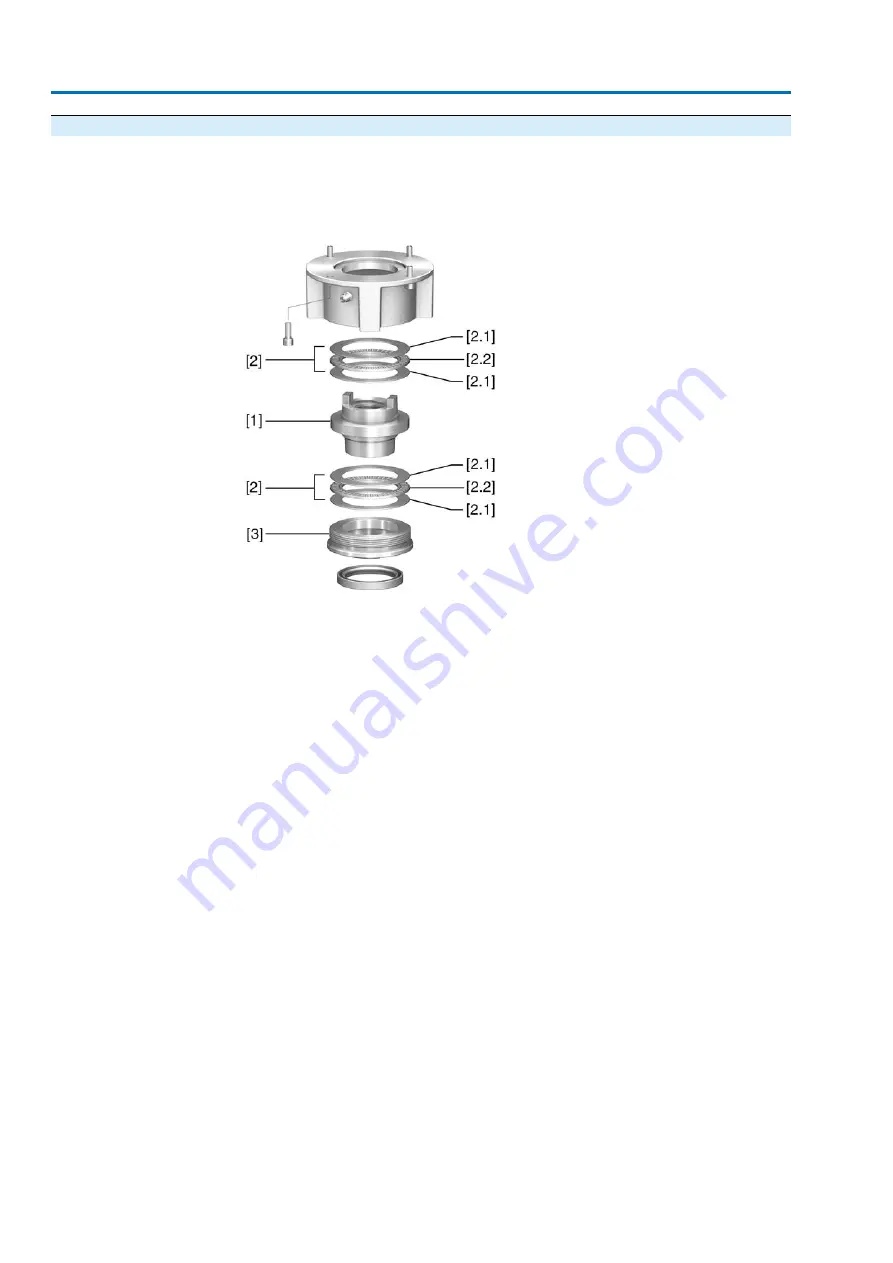
5.3.2.2. Stem nut for output drive type A: finish machining
This working step is only required if stem nut is supplied unbored or with pilot bore.
Information
For exact product version, please refer to the order-related technical data sheet or
the AUMA Assistant App.
Figure 17: Output drive type A
[1]
Stem nut
[2]
Axial needle roller bearing
[2.1] Axial bearing washer
[2.2] Axial needle roller and cage assembly
[3]
Spigot ring
Procedure
1.
Remove spigot ring [3] from output drive.
2.
Remove stem nut [1] together with axial needle roller bearings [2].
3.
Remove axial bearing washers [2.1] and axial needle roller and cage assemblies
[2.2] from stem nut [1].
4.
Drill and bore stem nut [1] and cut thread.
5.
Clean the machined stem nut [1].
6.
Apply sufficient Lithium soap EP multi-purpose grease to axial needle roller and
cage assemblies [2.2] and axial bearing washers [2.1], ensuring that all hollow
spaces are filled with grease.
7.
Place greased axial needle roller and cage assemblies [2.2] and axial bearing
washers [2.1] onto stem nut [1].
8.
Re-insert stem nut [1] with axial needle roller bearings [2] into output drive.
9.
Screw in spigot ring [3] until it is firm against the shoulder.
20
SAV 07.2 – SAV 16.2 / SARV 07.2 – SARV 16.2 Control unit: electronic (MWG)
Assembly
ACV 01.2 HART