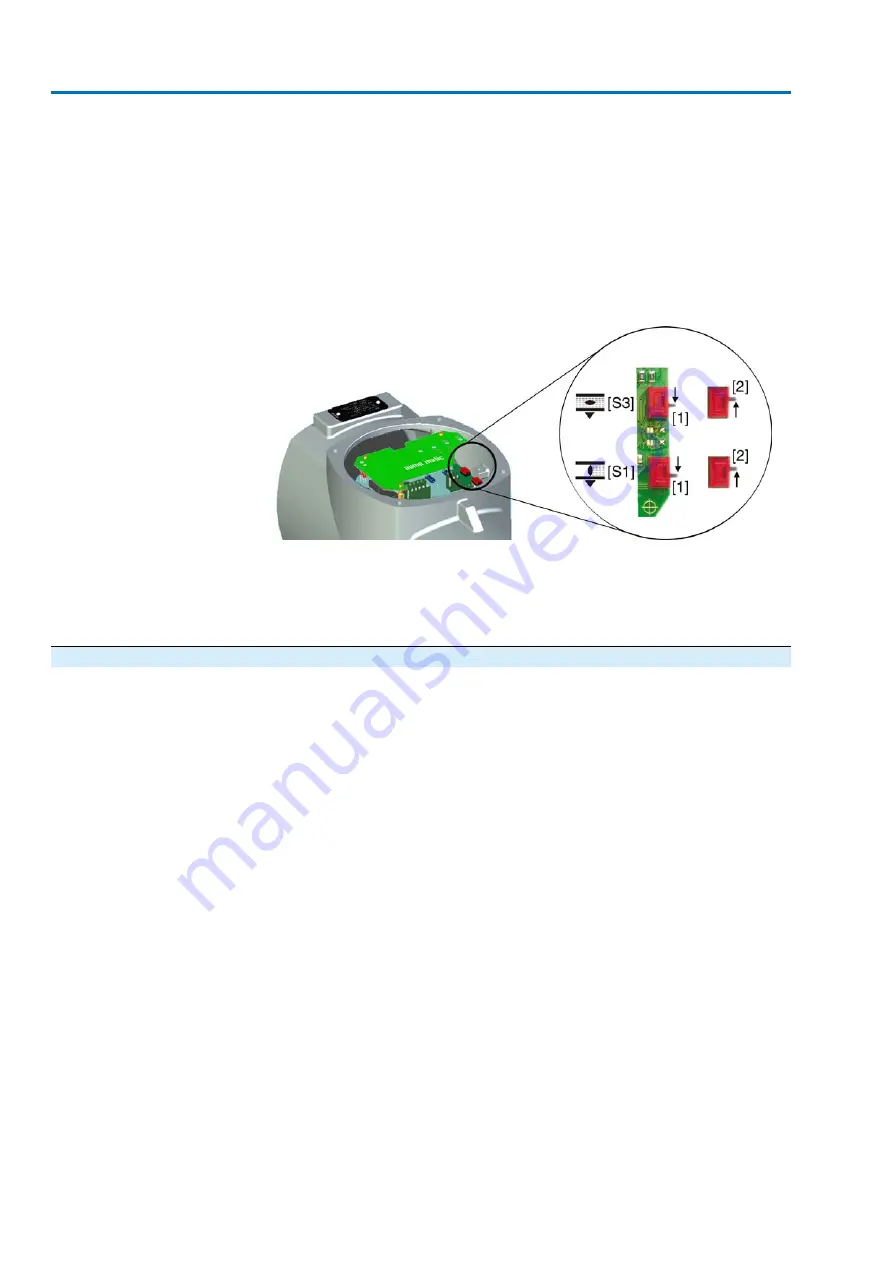
Limit seating
The limit switching is set in such a way that the actuator switches off at the desired
switching points. The torque switching acts as overload protection for the valve.
Torque seating
The torque switching is set to the desired tripping torque. After reaching the tripping
torque, the actuator is turned off.
The limit seating is used to signal that the limit switching will trip shortly before
reaching the set tripping torque. If this is not the case, either the indication light on
the local controls or the alarm contact K9 (collective fault signal) will signal a fault.
→
Set type of seating for end positions via DIP switches [S1] and [S3].
Figure 52:
DIP switches on logic board
[S1]
DIP switch for end position CLOSED
[S3]
DIP switch for end position OPEN
[1]
Position [1] = limit seating
[2]
Position [2] = torque seating
10.3
Push-to-run operation or self-retaining: set
Push-to-run operation or self-retaining is set via a DIP switch on the logic board.
Push-to-run operation
Actuator only runs in direction OPEN or CLOSE while an operation command is
being received. The actuator stops if the operation command is cancelled.
Self-retaining
After receiving an operation command, the actuator continues to run in direction
OPEN or CLOSE, even if the operation command is cancelled (self-retaining). The
actuator is either stopped by the STOP command or if an end position or intermediate
position has been reached.
42
SAExC 07.1 – SAExC 16.1/SARExC 07.1 – SARExC 16.1
Commissioning – controls settings
AMExB 01.1