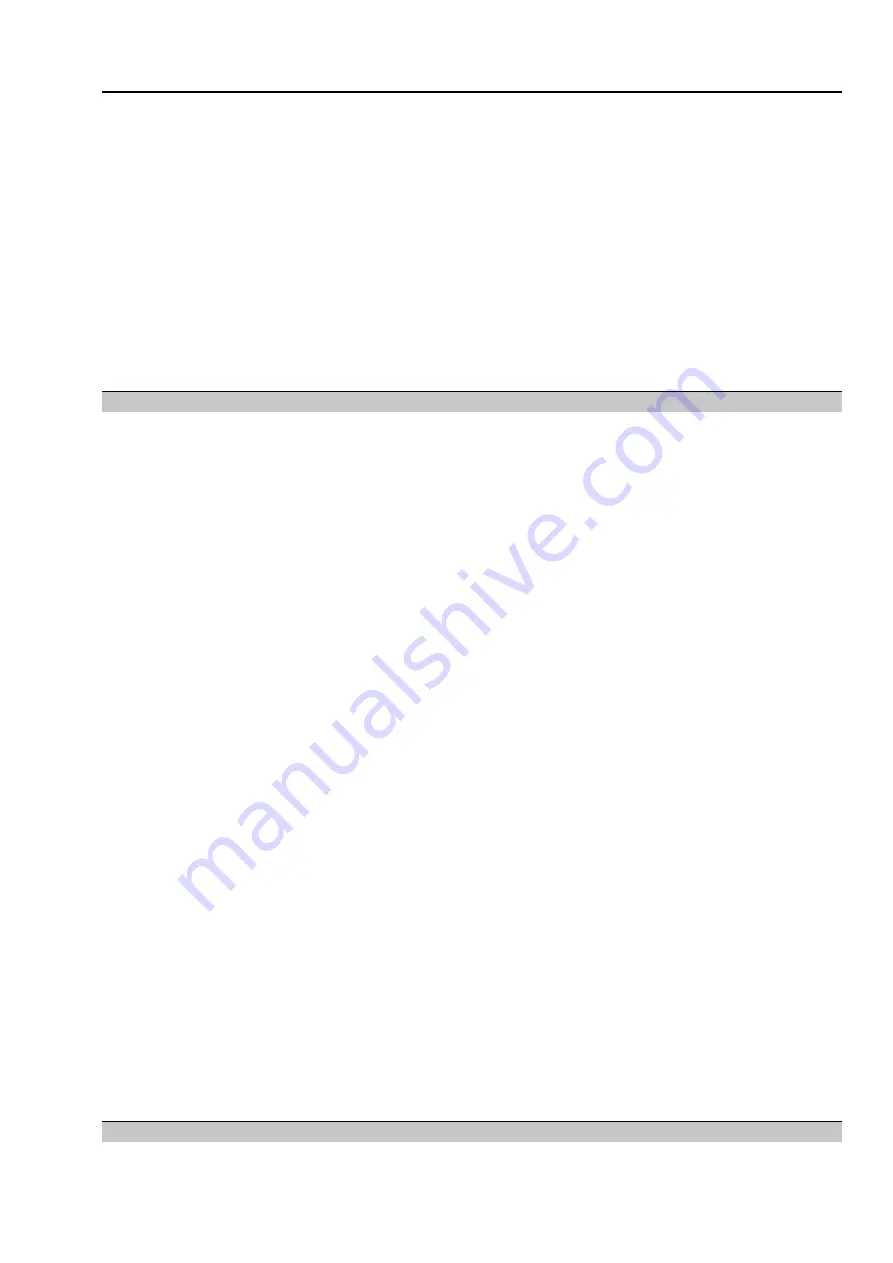
7.
Operate torque switches:
→
For “Safe CLOSING” (Safe ESD in direction CLOSE) configuration:
Turn test button [1] in direction of the TSC arrow.
→
For "“Safe OPENING” (Safe ESD in direction OPEN) configuration:
Turn test button [2] in direction of the TSO arrow:
➥
The safety function reaction to the torque switch signals is correct if:
-
Safety operation is not stopped.
-
A SIL fault signal is issued via the
SIL failure
output.
-
Display is illuminated in red.
8.
Once the test is complete, set
Safe ESDa
and
Safe ESDb
input signals to
+24 V DC (high) before reaching the end position.
9.
Acknowledge torque fault of standard controls.
10. Close switch compartment.
8.4.10.
Check Safe STOP function
Configuration
The test applies to the “SIL function” = “Safe STOP OPEN/CLOSE” (Safe STOP)
configuration. The seating configuration is not relevant to the test as it has no impact
on the Safe STOP function.
Test procedure
If the
Safe STOP CLOSE
or
Safe STOP OPEN
signals are switched accordingly,
the actuator must stop.
Test sequence
1.
Operate actuator in mid-position or at sufficient distance from the end positions.
2.
Start operation command in direction OPEN.
Information: For the test, operation commands (in directions OPEN or CLOSE)
can be executed both from remote (via DCS) and from Local at the controls
(via the push buttons of the local controls).
3.
Cancel release signals for directions CLOSE and OPEN one after the other:
3.1 First set
Safe STOP CLOSE
input signal to 0 V (low).
➥
Actuator must continue its operation
➥
No SIL fault signal may be issued.
3.2 Then set
Safe STOP OPEN
input signal to 0 V (low).
➥
The safety function is correct if the actuator stops.
➥
No SIL fault signal may be issued.
4.
Set
Safe STOP CLOSE
and
Safe STOP OPEN
to +24 V DC (high) again.
Information: If operation command OPEN from REMOTE issued via the control
room is still present, the actuator may start its operation!
5.
Start operation command in direction CLOSE
6.
Cancel release signals for directions OPEN and CLOSE one after the other:
6.1 First set
Safe STOP OPEN
input signal to 0 V (low).
➥
Actuator must continue its operation
➥
No SIL fault signal may be issued.
6.2 Then set
Safe STOP CLOSE
input signal to 0 V (low).
➥
The safety function is correct if the actuator stops.
➥
No SIL fault signal may be issued.
7.
Set
Safe STOP CLOSE
and
Safe STOP OPEN
to +24 V DC (high) again.
Information: If operation command OPEN from REMOTE issued via the control
room is still present, the actuator may start its operation!
8.4.11.
Check combination of Safe ESD and Safe STOP function
Configuration
This test is required for the following versions or configurations:
37
Part-turn actuators
with AC 01.2-SIL/ACExC 01.2-SIL
Tests and maintenance