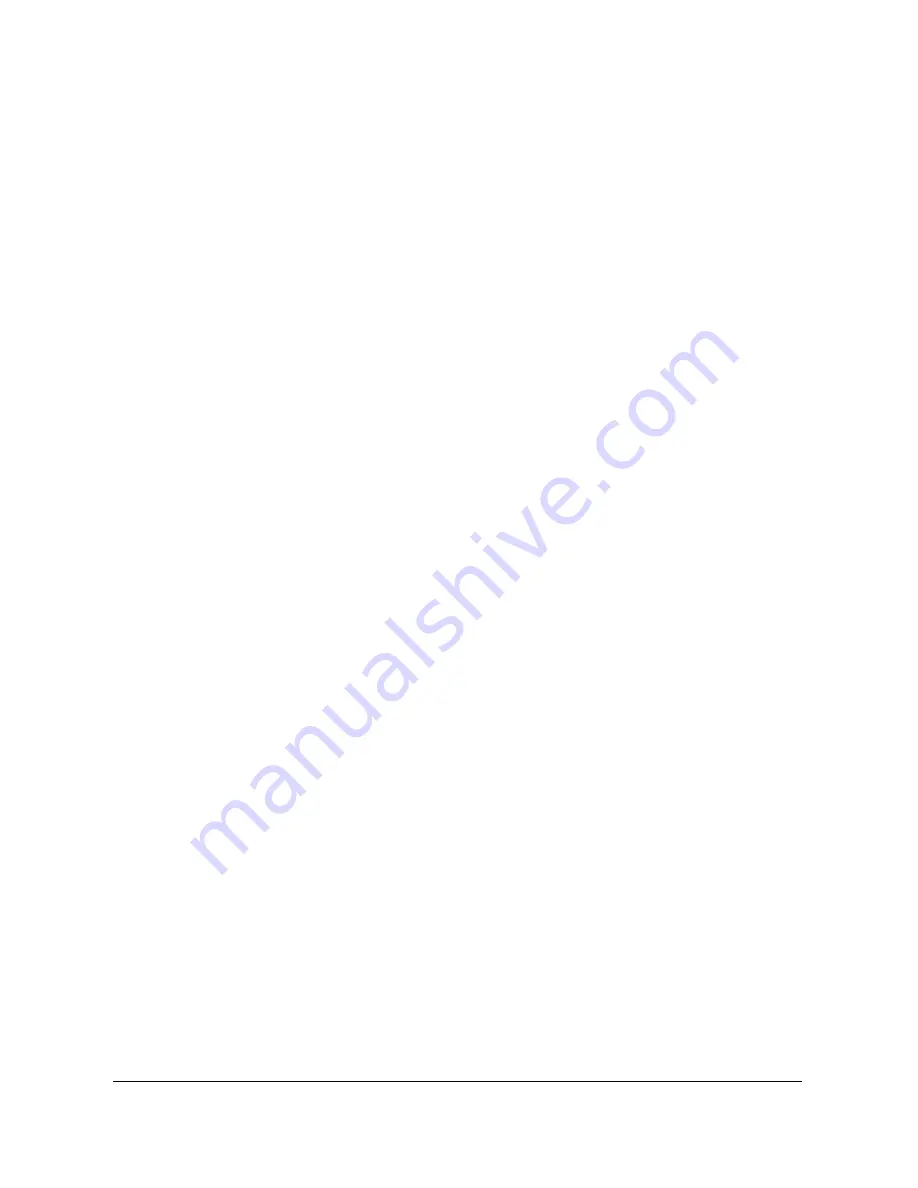
Quick-Change
Installation and Operation Manual
Document #9620-20-c-vb12m vb13m vb12t-05
Pinnacle Park
•
1031 Goodworth Drive
•
Apex, NC 27539
•
Tel: 919.772.0115
•
Fax: 919.772.8259
•
www.ati-ia.com
•
Email: [email protected]
C - 2
C. Control and Signal Modules
VB12-M, VB13-M, and VB12-T—Discrete Control Module
Supporting Integrated Valve
1. Product Overview
The Discrete Control modules are required to provide a means for the customer to communicate with and
control the Tool Changer.
Tool Changer I/O is provided to the customer through the MS-style Amphenol connector on the control/signal
Master module. Lock, Unlock, and Ready-to-Lock proximity sensor inputs (PNP sourcing-type) are provided
for confirmation of Tool Changer and locking mechanism positions. Other customer-assigned discrete I/O
points are also available through the connector. Note that 0 and 24 VDC supply lines are required to be on
certain pin locations of the customer interface connector. Reference drawings in Section 8 for pin out
information and location of the I/O signals.
Refer to the specific Tool Changer manual for details on the operation of the Tool Changer and recommended
procedure for coupling.
To avoid unintentional Tool release, the power for the unlatch valve is routed through a safety switch
connector. A safety switch must be connected to support this function. Refer to
for detailed information regarding the safety features of the discrete control modules.
1.1 Master Module
The Master module is equipped with a 36-Pin, MS-3122 style connector for interfacing with the Tool
Changer’s Lock, Unlock, and Ready-to-Lock sensors and for supplying signals and power to the end-of-
arm tooling (
Note: the Ready-to-Lock sensors in the Master are wired in series
). The Master is
designed to
support only PNP sensors
. Electrical schematics and connector details are provided in
Section 8—Drawings
Interface to the Tool Changers integrated RTL, Lock, and Unlock sensors are provided through four M8,
3-Pin connectors on the Master module. Refer to the specific Tool Changer manual for details on the
operation of RTL, Lock, and Unlock sensors. The Lock, Unlock, and RTL cables are provided as an
integrated part of the Tool Changer.
The safety switch is connected to the Master module via a 5-Pin, M12 connector mounted to the side of
the Master module. Refer to
Section 1.3—Master-side TSI with Safety Switch
regarding the safety features of the discrete control modules.
An electrical interface is provided on the Master module for support of a
double-solenoid
integrated
valve (DC Voltage, sourcing-type:
single-solenoid valve is not supported
). The integrated valve can be
supplied from ATI as part of the valve adapter block (such as 9121-JR2-M). Refer to the valve adapter
block manual for more information
(9620-20-C-Jxx Air and Valve Adapters with Valve Signal Pass
Thru
). Electrical interface drawings and connector details provided are in
Section 8—Drawings
1.2 Tool Module
The VB12 Tool module is equipped with a 36-Socket, MS-3122 style connector and provides the
interface for supplying signals and power to the end-of-arm tooling. When the Tool Changer is coupled,
the Master and Tool modules interface using a spring-loaded pin blocks. A flexible boot surrounds the
pin block to seal the connection from moisture and liquid while coupled.