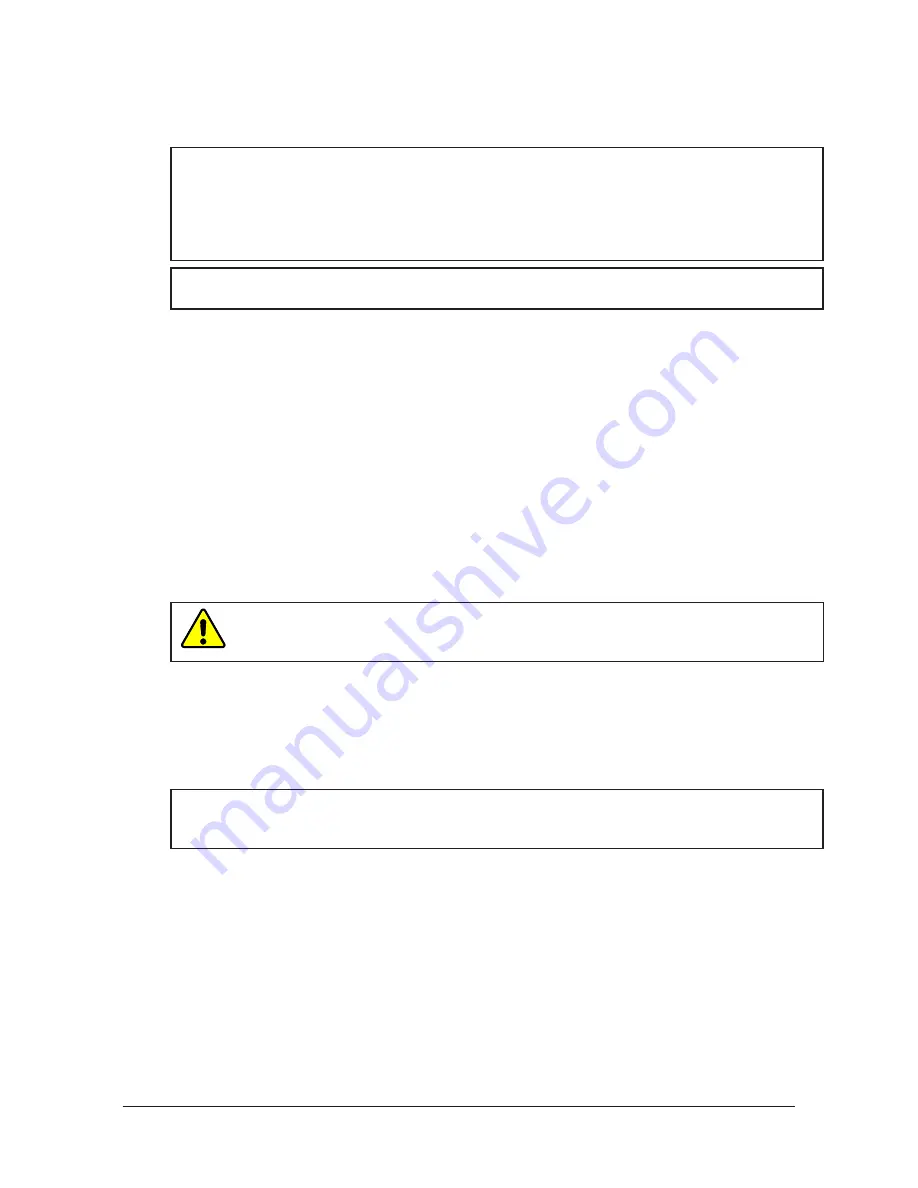
Manual, Robotic Tool Changer, QC‑24Z1
Document #9610‑20‑3727‑03
Pinnacle Park • 1041 Goodworth Drive • Apex, NC 27539 • Tel: 919.772.0115 • Fax: 919.772.8259 •
19
5. A sufficient delay must be programmed between locking valve actuation and robot motion so that the
locking process is complete before moving the robot. If equipped with lock and unlock sensors, the lock
signal should read “ON” (true) and the unlock signal should read “OFF” (false).
NOTICE:
If the locking mechanism has been actuated and both the lock and unlock signals are
OFF, then a “missed tool” condition has occurred (for example, the Tool is not in the stand or is
not positioned properly).
in this case an error should be generated and the robot program
halted.
The situation requires manual inspection to determine the cause of the problem. Some
configurations will require a manual unlock of the Master plate before attempting coupling, refer
to the Control/Signal Module Manual for instructions.
NOTICE:
The locking mechanism must be in the unlock state before another attempt is made to
couple or damage could occur to the robot and/or the Tool Changer.
4.2 Fail-Safe Operation
A fail‑safe condition occurs when there is an unintended loss of lock air pressure to the Master plate. When
air pressure is lost, the Tool Changer relaxes and there may be a slight separation between the Master
and Tool plates. The lock sensor may indicate that the unit is not locked. ATI’s patented fail‑safe feature
utilizes a multi‑tapered cam to trap the ball bearings and prevent an unintended release of the Tool plate.
Positional accuracy of the tooling is not maintained during this fail‑safe condition. Do not operate the Tool
Changer in the fail‑safe condition. If the source air is lost to the unit, movement should be halted until air
pressure is restored.
After air pressure is re‑established to the Master plate, the locking mechanism will energize and securely
lock the Master and Tool plates together. in some cases when the load on the tool changer is significantly off
center, it may be necessary to position load underneath the tool changer or return the tool to the tool storage
location to ensure a secure lock condition. If equipped, make sure the lock sensor indicates the Tool Changer
is in the locked position before resuming normal operations. Consult your Control/Signal Module Manual
for specific error recovery information.
CAUTION:
Do not use the Tool Changer in a fail‑safe condition. Damage to the locking
mechanism could occur. Re‑establish air pressure and ensure the Tool Changer is in a
secure lock position before returning to normal operations.
4.3 Conditions for Uncoupling
1. Position Tool plate in the tool stand so that there is little or no contact force between the Tool plate
and tool stand.
2.
Release air on the Lock port and apply air to the Unlock Port (If equipped, the Unlock sensor will
indicate the Tool Changer is in the Unlocked position).
NOTICE:
The air will cause the locking mechanism to be released and the weight of the Tool
plate and attached tooling will assist in its removal. The Tool weight assists in the uncoupling If
the Tool is released in the vertical position only.
3.
A sufficient delay must be programmed between unlocking valve actuation and robot motion, so that
unlocking process is complete and the Tool plate is fully released before moving the robot.
4.
Move the Master plate axially away from the Tool plate.
5.
In automated Tool change applications, it is recommended that a Tool presence sensor(s) be used in the
tool stand to verify that the Tool is present and that the Tool remains in place as the robot moves away
after unlocking process.
4.4
Tool Identification
When using multiple Tools, it is good practice to implement a Tool‑ID system that identifies each Tool
with a unique code. Tool‑ID can be used to verify that the robot has picked up the proper Tool. Modules
with Tool‑ID are available for purchase through the ATI website. Go to
http://www.ati‑ia.com/products/
toolchanger/tool_changer_modules.aspx
for products available or contact ATI for assistance.