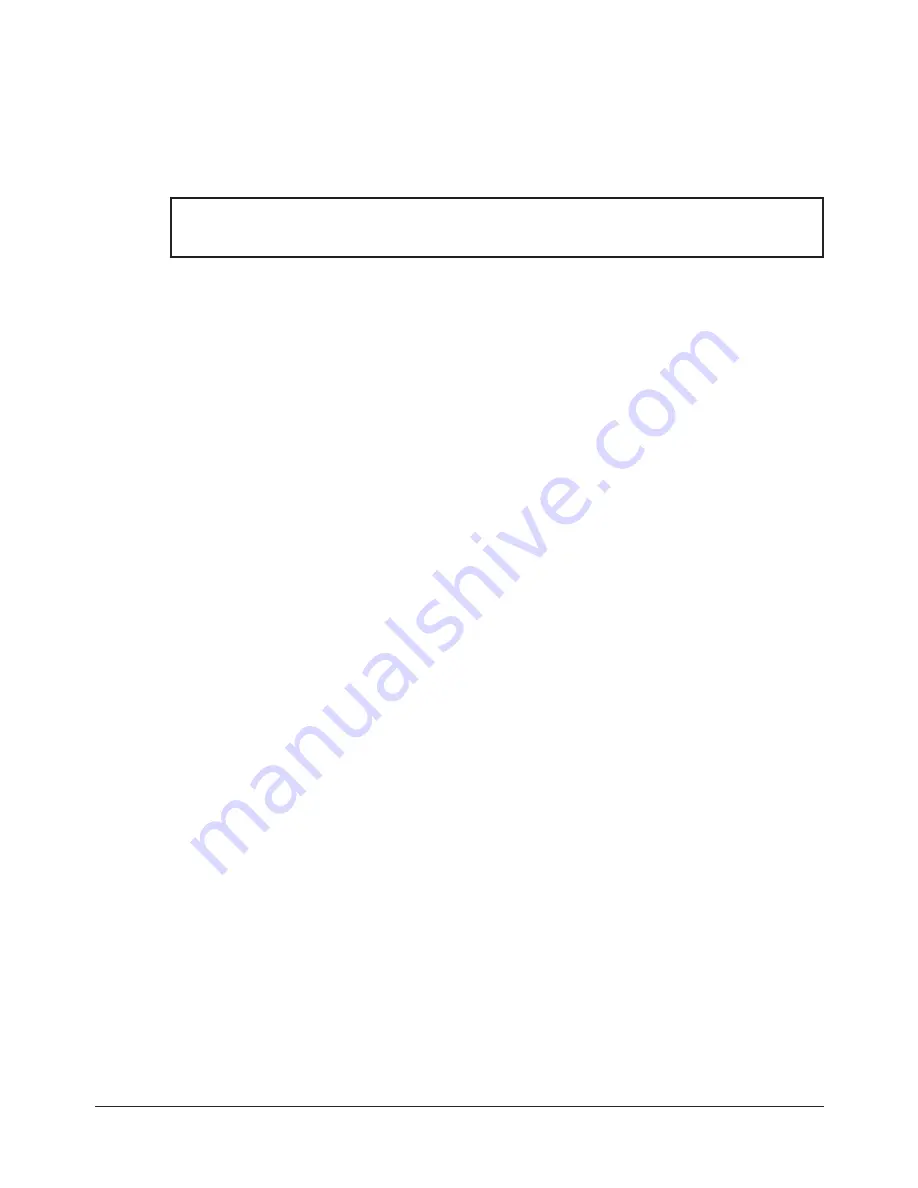
Manual, Robotic Tool Changer, QC-5 through QC-27
Document #9610-20-2254-09
Pinnacle Park • 1041 Goodworth Drive • Apex, NC 27539 USA • Tel: 919.772.0115 • Fax: 919.772.8259 •
www.ati-ia.com
38
4.3 Uncoupling Sequence
1. Position the Tool plate in the tool stand such that there is little or no contact force between the Tool plate
and tool stand.
2.
Release air on the Lock port and apply air to the Unlock Port (if equipped, the Unlock sensor will
indicate the Tool Changer is in the Unlocked position).
NOTICE:
The air will cause the locking mechanism to be released and the weight of the Tool
plate and attached tooling will assist in its removal. The Tool weight assists in uncoupling if the
Tool is released in the vertical position only.
3.
A sufficient delay must be programmed between unlocking valve actuation and robot motion so that the
unlocking process is complete and the Tool plate is fully released before moving the robot.
4.
Move the Master plate axially away from the Tool plate.
5.
In automated Tool change applications, it is recommended that a Tool presence sensor(s) be used in the
tool stand to verify that the Tool is present and that the Tool remains in place as the robot moves away
after the unlocking process.
4.4
Tool Identification
When using multiple Tools, it is good practice to implement a Tool-ID system that identifies each Tool with
a unique code. Tool-ID can be used to verify that the robot has picked up the proper Tool. Modules with
Tool-ID are available from ATI, refer to our Web site
http://www.ati-ia.com/products/toolchanger/tool_
for products available or contact ATI for assistance.