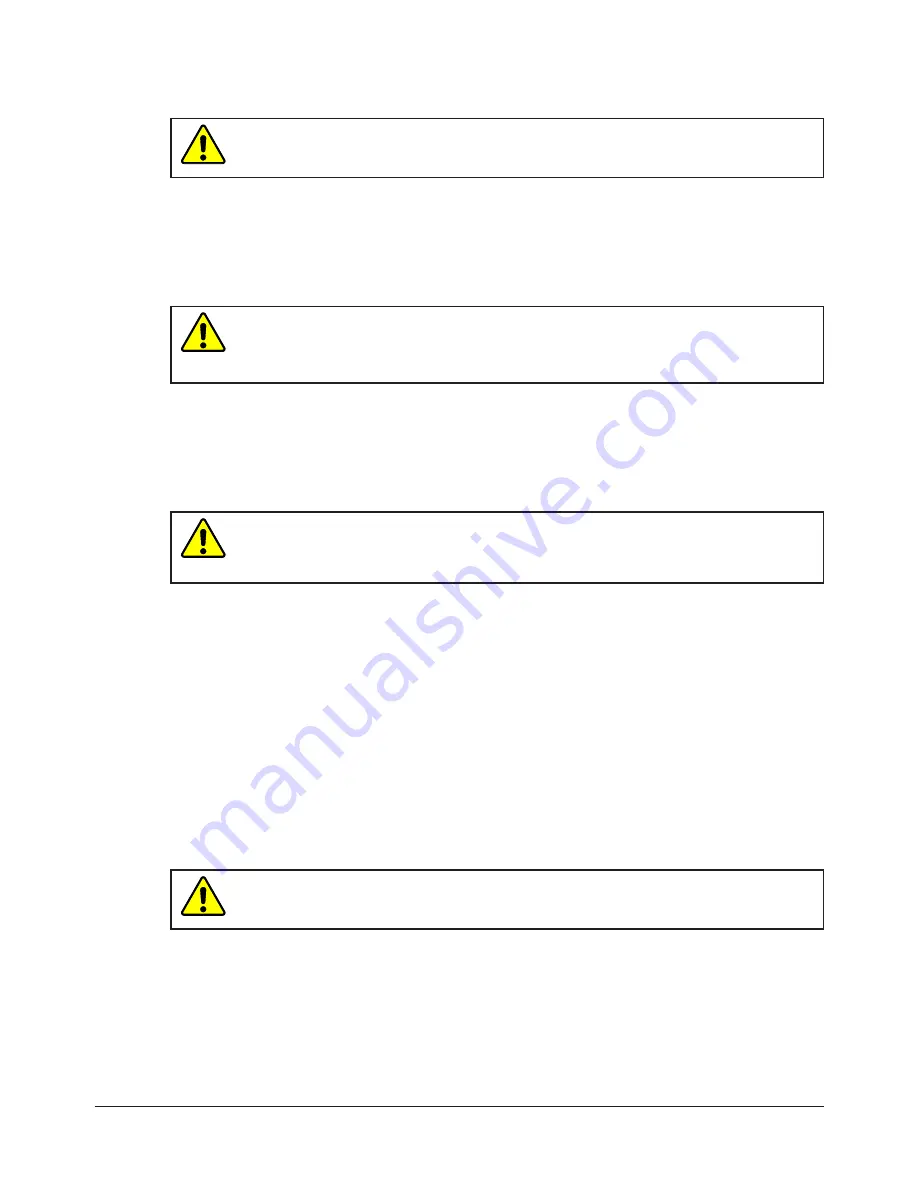
Manual, Robotic Tool Changer, QC-5 through QC-27
Document #9610-20-2254-09
Pinnacle Park • 1041 Goodworth Drive • Apex, NC 27539 USA • Tel: 919.772.0115 • Fax: 919.772.8259 •
www.ati-ia.com
37
4.1 Coupling Sequence
CAUTION:
The locking mechanism must be in the unlock position when attempting to
couple the Tool Changer. Failure to adhere to this condition may result in damage to
the unit and/or the robot.
1.
Position the Master plate above the Tool plate with the air supplied to the Unlock Port (if equipped, the
Unlock sensor will indicate the Tool Changer is Unlocked).
2.
Move the Master plate toward the Tool plate so that the (2) alignment pins enter the alignment holes on
the opposite plate. Program the robot so that the Master plate and Tool plate are aligned axially and are
parallel to each other as closely as possible
.
This will minimize Tool movement and subsequent wear
during lock-up.
CAUTION:
No-Touch™ locking technology allows the unit to couple with a separation
distance between the Master and Tool. Direct contact of the Master and Tool mating
surfaces is not suggested or required prior to coupling. Contact may result in damage
to the unit and/or the robot.
3.
When the (2) faces are within the specified No-Touch™ distance, release the pressure from the Unlock
port and supply air to the Lock port. The Tool plate is drawn toward the Master plate and coupled. Air
must be maintained on the Lock Port during operation to assure rigid coupling (if equipped, the Lock
sensor will indicate the Tool Changer is in the Locked position).
4.
A sufficient delay must be programmed between locking valve actuation and robot motion so that the
locking process is complete before moving the robot.
CAUTION:
If air pressure is lost during operation, ATI’s patented fail-safe design
prevents the Tool plate from being released.
Do not use the Tool Changer in a fail-safe
condition. Re-establish air pressure and ensure the Tool Changer is in a secure lock
position before returning to normal operations.
4.2 Fail-Safe Operation
A fail-safe condition occurs when there is an unintended loss of lock air pressure to the Master plate. When
air pressure is lost, the Tool Changer relaxes and there may be a slight separation between the Master and
Tool plates. The lock sensor may indicate that the unit is not locked. ATI’s patented fail-safe feature utilizes
a multi-tapered cam to trap the ball bearings and prevent an unintended release of the Tool plate. Positional
accuracy of the tooling is not maintained during this fail-safe condition. Do not operate the Tool Changer
in the fail-safe condition. If source air is lost to the unit, movement should be halted until air pressure is
restored.
After air pressure is re-established to the Master plate, the locking mechanism will energize and securely
lock the Master and Tool plates together. In some cases when the load on the tool changer is significantly
off center, it may be necessary to position the load underneath the tool changer or return the tool to the tool
storage location to ensure a secure lock condition. If equipped, make sure the lock sensor indicates the Tool
Changer is in the locked position before resuming normal operations. Consult your Control/Signal Module
Manual for specific error recovery information.
CAUTION:
Do not use the Tool Changer in a fail-safe condition. Damage to the locking
mechanism could occur. Re-establish air pressure and ensure the Tool Changer is in a
secure lock position before returning to normal operations.