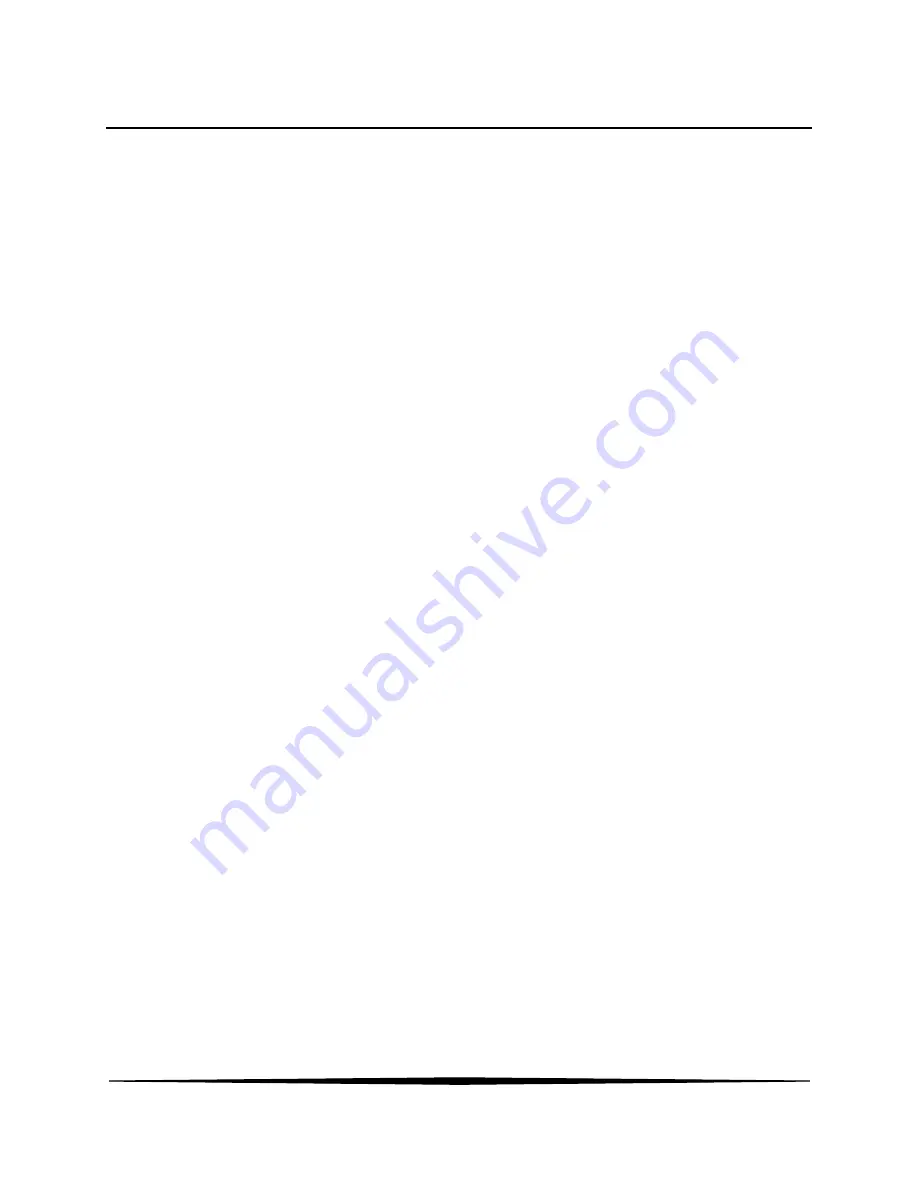
35
O&M Manual
Rev-H (6/19)
Part 6 - Control
The Control Menu contains all of the output control user settings:
Set PID 0%
If the PID is enabled, this function sets the minimum and
maximum
Set PID 100%
controller end points. Unlike the standard 4-20 mA output, the controller
[Iout1=PID]
does not “scale” output values across the endpoints. Rather, the
endpoints determine where the controller would normally force minimum
or maximum output in an attempt to recover the setpoint (even though the
controller can achieve 0% or 100% anywhere within the range.)
If the 0% point is lower than the 100% point, then the controller action will
be “reverse” acting. That is, the output of the controller will increase if the
measured value is less than the setpoint, and the output will decrease if
the measured value is larger than the setpoint. Flipping the stored values
in these points will reverse th
e action of the controller to “direct” mode.
The entry value is limited to a value within the range specified in “Set
Range”, and the 0% and the 100% point must be separated by at least 1%
of this range Use the LEFT arrow key to select the first digit to be modified.
Then use the UP and LEFT arrow keys to select the desired numerical
value. Press ENTER to store the new value.
PID Setpnt
The measured value which the controller is attempting to maintain by
[Iout1=PID]
adjusting output value. It is the nature of the PID controller that it never
actually gets to the exact value and stops. The controller is continually
making smaller and smaller adjustments as the measured value gets near
the setpoint.
PID Prop
Proportional gain factor. The proportional gain value is a multiplier on
[Iout1=PID]
the controller error (difference between measured value and setpoint
value.) Increasing this value will make the controller more responsive.
PID Int
Integral is the number of “repeats-per-minute” of the action of the
[Iout1=PID]
controller. It is the number of times per minute that the controller acts on
the input error. At a setting of 2.0 rpm, there are two repeats every minute.
If the integral is set to zero, a fixed offset value is added to the controller
(manual reset.) Increasing this value will make the controller more
responsive.
PID Deriv
Derivative is a second order implementation of Integral, used to suppress
[Iout1=PID]
“second-order” effects from process variables. These variables may
include items like pumps or mixers that may have minor impacts on the
measured value. The derivative factor is rarely used and therefore it is best
in most cases to leave it at the default value. Increasing this value will
make the controller more responsive.
Set 4 mA (#1)
These functions set the main 4 and 20 mA current loop output points for
Set 20 mA (#1)
the transmitter. The units displayed depend on the selection made in the
CONFIG menu for Iout #1 Mode. Typically, Iout #1 is used for
concentration.