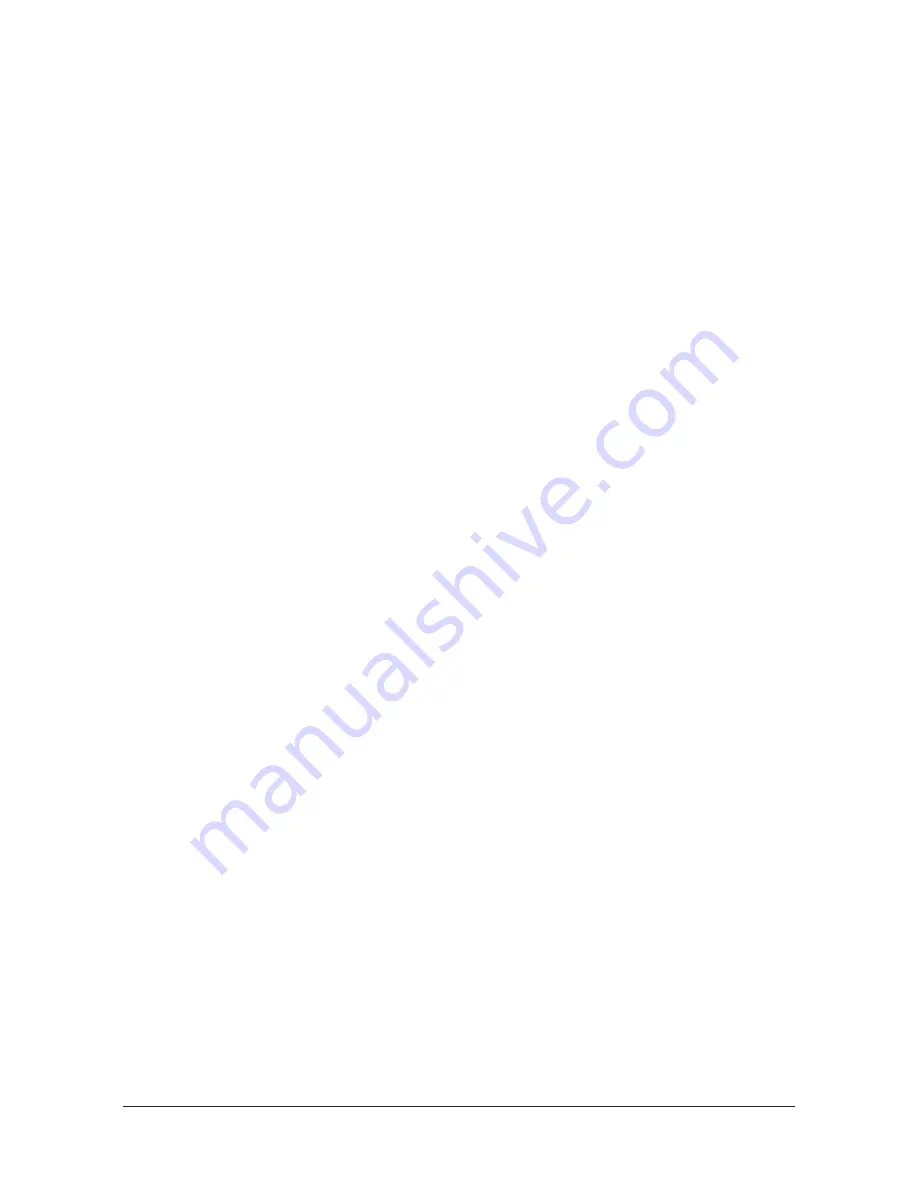
Manual, Control Module, PROFINET, DL10
Document #9620-20-C-DL10-04
Pinnacle Park • 1031 Goodworth Drive • Apex, NC 27539 • Tel: 919.772.0115 • Fax: 919.772.8259 •
C-6
C. Control and Signal Modules
DL10—PROFINET
®
Control/Signal Module
1. Product Overview
The modules enable the customer to control and communicate with the Tool Changer through a PROFINET
network. A PROFINET node is established on the Master only. Control of the Tool Changer is achieved through
the Master node along with the reporting of the various Tool Changer I/O. The Tool module supports Tool‑ID and
functions as a pass‑through for PROFINET network and power to the customer tooling.
A 3‑pin spring signal contact block is provided on the Master module for support of integrated single or double
solenoid valves. The integrated valve is supplied from ATI as part of the valve adapter block (9121‑Jxx). Refer to
the valve adapter block manual for more information (9620‑20‑C‑Jxx Air and Valve Adapters with Valve Signal
Pass Through). Electrical connector details are provided in drawings in
Because the Master module requires the use of a valve adapter, the Tool module must have a spacer module so that
the Master and Tool modules are aligned when coupled.
In addition to supporting the standard Tool Changer input signals (Locked, Unlocked, and Ready to Lock proximity
sensors) the modules also support advanced diagnostic and fault reporting. Refer to
Compliant spring pins are provided on the Master and fixed contact pins on the Tool. To avoid unintentional human
contact, the Master spring pins are recessed below an insulated surface on both the power and signal circuits. When
the modules are coupled, the V‑ring seal forms a water resistant but not waterproof seal around the pin block.
The Unlock signal to the integrated solenoid valve is routed through a “Tool Stand Interlock” (TSI) safety circuit
that prevents the robot from unlocking the Tool from the Master, when the Tool is not in the tool stand. Refer to
for additional information regarding TSI.
1.1 DL10 Master Module
The module has the following connections:
•
(1) 4‑pin male M12 D‑coded PROFINET connector.
•
(1) 5‑pin male auxiliary power connector.
•
(4) 3‑pin female M8 connectors for RTL1, RTL2, Lock, and Unlock sensor connections.
•
(1) M5 x 0.8 threaded hole for FE ground terminal connection that is accessed by removing the M5
set screw plug.
•
(1) 3‑pin internal valve connection
The Master module also incorporates ATI’s exclusive Arc Prevention Circuit which extends the life of all
electrical power contacts by eliminating arcing caused by inductive loads and high inrush current during
coupling/uncoupling. Refer to
Section 2.2—Arc Prevention Circuit
for additional information regarding the
Arc Prevention Circuit.
The module provides status LED’s to visually indicate its operation. A reset button provides the ability to
return to factory default settings. Refer to
Section 2.1.2—System Failure (SF) and Bus Failure (BF) LEDs
and
Section 2.1.3—Ethernet 1 and Ethernet 2 LEDs
.
PROFINET requires a FE ground, the Master module provides a M5 x 0.8 FE ground terminal that is passes
FE ground to the Tool Module through the 7‑Pin contact block.