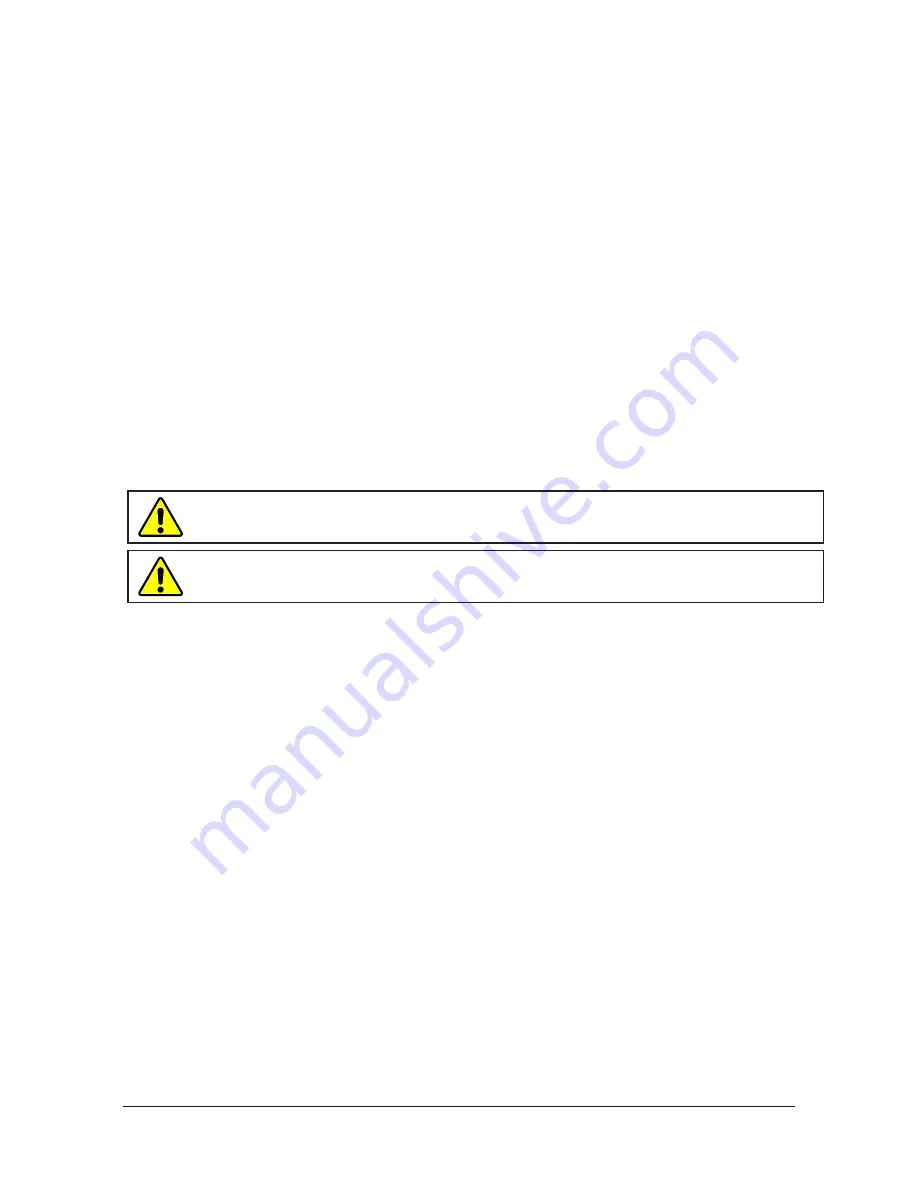
Manual, Fluid/Air, FS2
Document #9620-20-D-FS2-04
Pinnacle Park • 1031 Goodworth Drive • Apex, NC 27539 • Tel: 919.772.0115 • Fax: 919.772.8259 •
D-5
3. Operation
The fluid/air modules are designed to pass fluid/air utilities from the Master to the Tool for use by the customer’s
tooling.
Four (4) self‑sealing valves are provided on the Master side so that the fluid/air circuits do not discharge during tool
changes.
Typically, self‑sealing valves are specified on the Tool for ports being used for fluid service.
The compressibility of gasses makes it unnecessary to isolate and discharge lines during a tool change. However,
liquids are incompressible and therefore coupling lines while pressurized is to be avoided. Liquid displaced by
mating coupler components creates extremely high pressure spikes and fluid velocities potentially causing seal
damage. These problems become more pronounced as the operating pressure is increased.
In all liquid coupling applications, the customer is advised to take the following steps:
•
Plumb the ports on the fluid/air modules using flexible hoses, which are able to absorb pressure spikes and
pulses. Highly reinforced hoses and hard pipe must not be used.
•
Turn off the supply pump to the circuit and discharge pressure in the lines prior to a tool change.
•
Accumulators can be installed on both the Master and Tool side plumbing. This is particularly important on the
Tool side, even with the pump turned off and Master side pressure discharged.
•
During routine maintenance of the Tool Changer, the fluid/air modules should be inspected and re‑lubricated.
Water and most solvents will wash away lubricants necessary to prolong seal life.
CAUTION:
Failure to follow these steps will result in premature seal failure, jetting of fluid
from the couplers during tool changes, and significant pressure pulses in customer tooling.
CAUTION:
To maximize the life and performance of fluid/air components, read and follow the
steps in the Operations section of this manual.