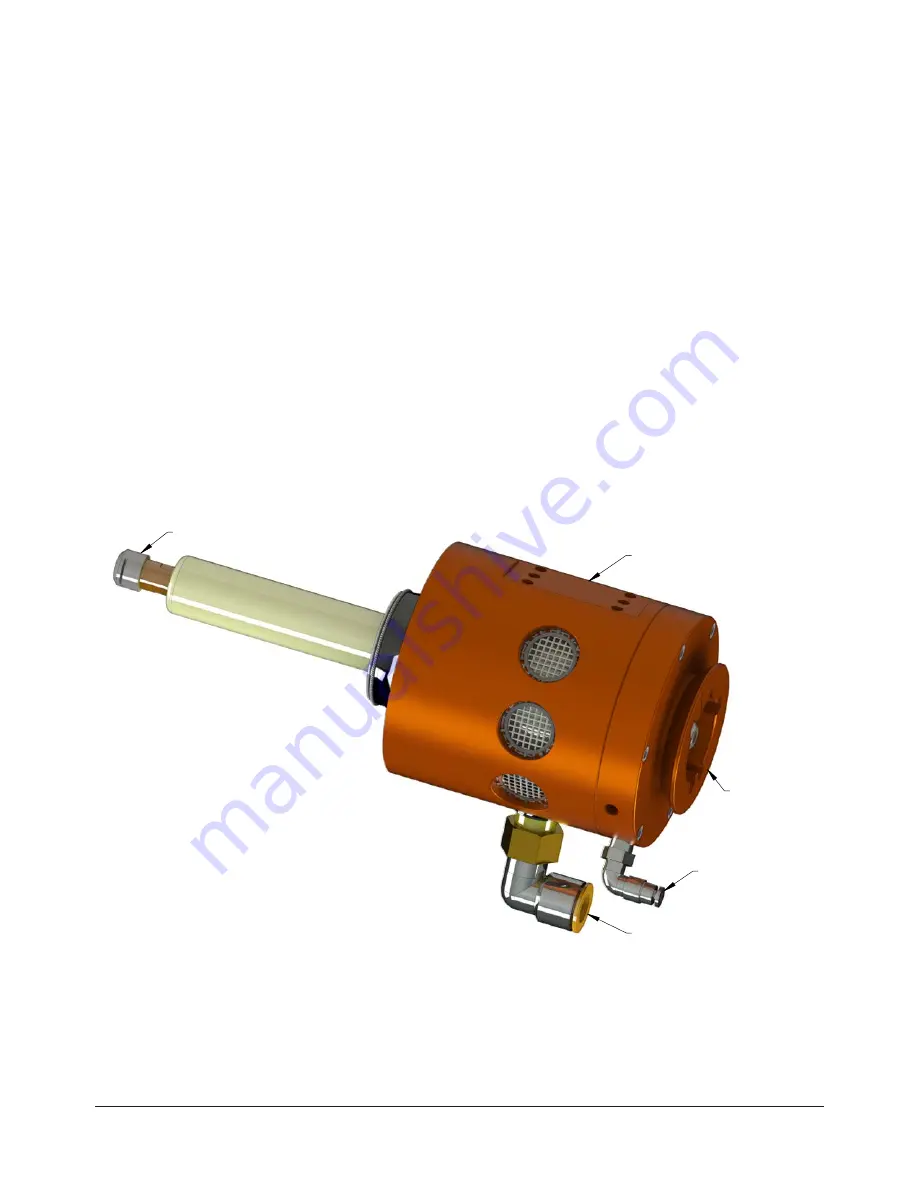
Manual, Flexdeburr, RC‑660 Series
Document #9610‑50‑1017‑10
Pinnacle Park • 1031 Goodworth Drive • Apex, NC 27539 USA • Tel: +1.919.772.0115 • Fax: +1.919.772.8259 • www.ati‑ia.com
8
2. Product Overview
The Radially‑Compliant (RC) deburring tool, also known as Flexdeburr, is a turbine‑driven deburring unit for
deburring aluminum, plastic, steel, etc. with a robot or CNC machine. The RC Deburring Tool is especially suited
for removal of parting lines and flash from parts. However, its flexible design allows it to be used in a wide variety
of applications.
The RC deburring tool’s pneumatically controlled, articulated design allows the cutting bur to follow the part
profile and compensate for surface irregularities while maintaining a constant, settable force. This allows high feed
rates with uniform quality in any orientation. The tool also requires no oil, allowing clean exhaust air to be vented
directly into the work environment.
Compliance is supported by air pressure applied to the shaft of the unit. The RC deburring tool also utilizes
standard industrial tungsten‑carbide bits which allows for adaptation to changing assembly lines and
part requirements.
The RC‑660‑ER provides for (2) mounting types; a side mounting and an axial mounting. The side mounting
provides (2) locating dowel pins and (4) threaded holes. The axial mounting utilizes a tapered flange that requires
an adapter plate. Custom adapter plates for both side and axial mounting are available from ATI. Refer to
for more information.
The RC‑660‑ER is equipped with a 1/2" Push‑to Connect fitting to supply the motor air and a 5/32" [4 mm] Push‑to
Connect fitting to supply the compliance air.
A tool collet system secures the bur. Many collet sizes are available to accommodate a wide variety of applications.
Figure 2.1—RC‑660‑ER Deburring Tool
Compliance Air
Connection
Motor Air Connection
Tool Collet
Side Mounting
Axial
Mounting
2.1 Tool Collet Systems
All Flexdeburr products utilize removable collets to grip customer‑supplied cutting tools. Different collet
diameters may be substituted to retain numerous cutter shank diameters. The collet retaining nut is loosened
to open the collet allowing cutting tools to be removed and inserted. Once the tool is set to the desired depth,
spanner wrenches are used to tighten the collet nut causing the collet to collapse and secure the cutting
tool. The turbine motor design does not allow the installation of spindle brakes or Quick Change (drawbar)
collet systems.