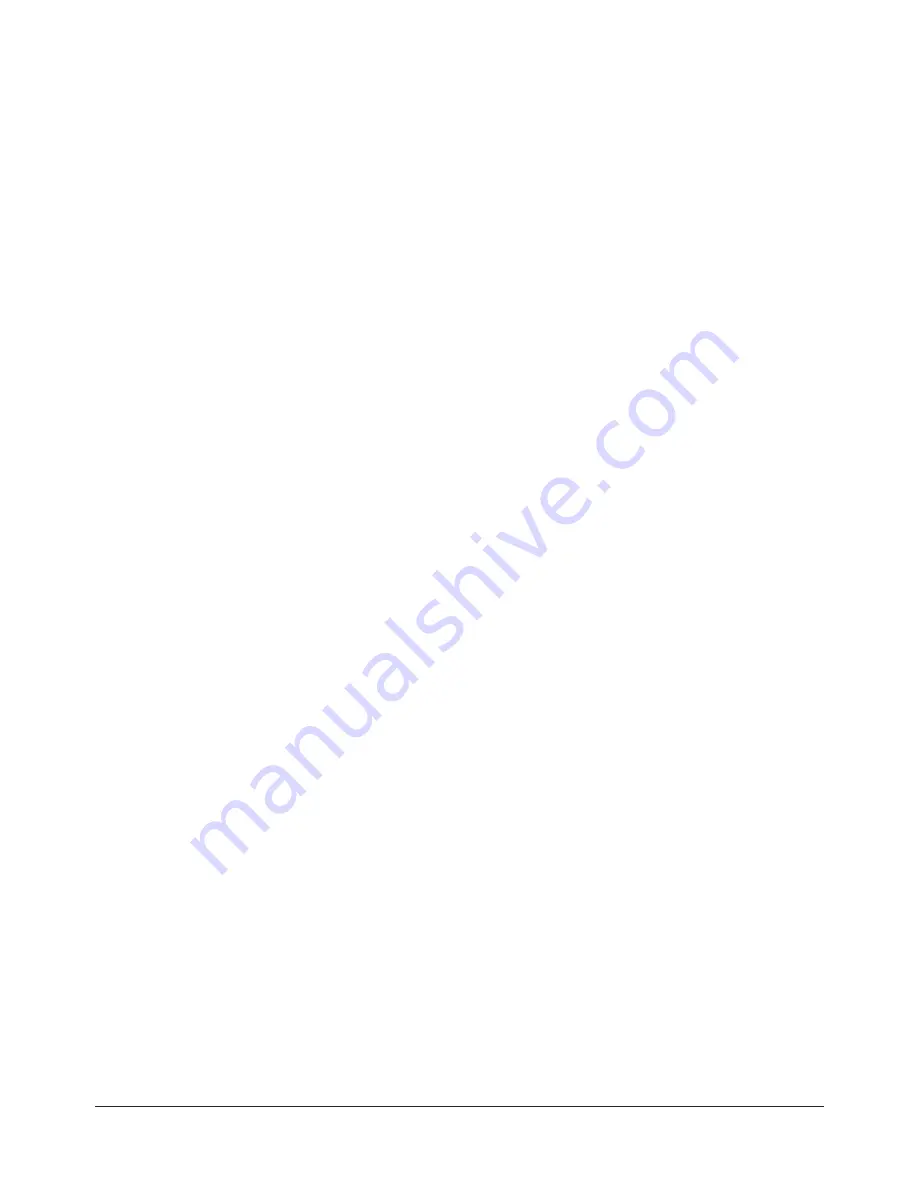
Manual, Flexdeburr, RC‑660 Series
Document #9610‑50‑1017‑10
Pinnacle Park • 1031 Goodworth Drive • Apex, NC 27539 USA • Tel: +1.919.772.0115 • Fax: +1.919.772.8259 • www.ati‑ia.com
19
4.3 Flexdeburr Working Environment
As described in previous sections, the RC deburring tool should only be used in conjunction with a robot in
a secured work cell/chamber.
The work cell must be secured by means of barriers to prohibit personnel from entering the cell. A lockable
door should be included as a part of the barrier in order to facilitate access to the cell for authorized
personnel only. The barrier could consist partly or fully of Plexiglas to facilitate observation of the
deburring operations.
During system or deburring tool maintenance, make sure the RC deburring tool and robot are stopped
before entering the robot cell. When installing and testing, Never be present in the cell when the Deburring
tool is running.
Be aware of rotating parts. Use eye‑protection while working around the deburring tool.
Be aware of high sound levels. While the Flexdeburr air motor is not loud, the cutting action associated
with deburring frequently is loud. Always use hearing protection while working in the neighborhood of the
deburring cell.
The deburring tool should not be used to deburr materials that are prone to fracture. A fracturing work
piece may result in pieces of material damaging surrounding working environment and personnel. Material
removed correctly should be in the form of chips.
4.4 Tool Center Point (TCP) Position and Programming
shows the RC deburring tool dimensions. The Flexdeburr provides radial compliance and
performs best when the cuts taken are not excessively deep. The deburring tool spindle must Never be
running while programming the robot. During teaching, the compliance air must be on and supplied above a
minimum of 0.35 bar (5 psi).
Two programming methods are suggested but others are possible. In the first method, a dowel pin of suitable
diameter is inserted in place of a cutting tool (simulating the cutter shank diameter) when teaching the robot
path. For example, 6 mm collets require a 6 mm diameter pin of suitable length. The dowel pin should
extend sufficiently from the collet to reach the surface on the bur where cutting is desired (see
The diameter of the cutter should not exceed that of the dowel pin by more than the compliance of the RC
deburring tool.