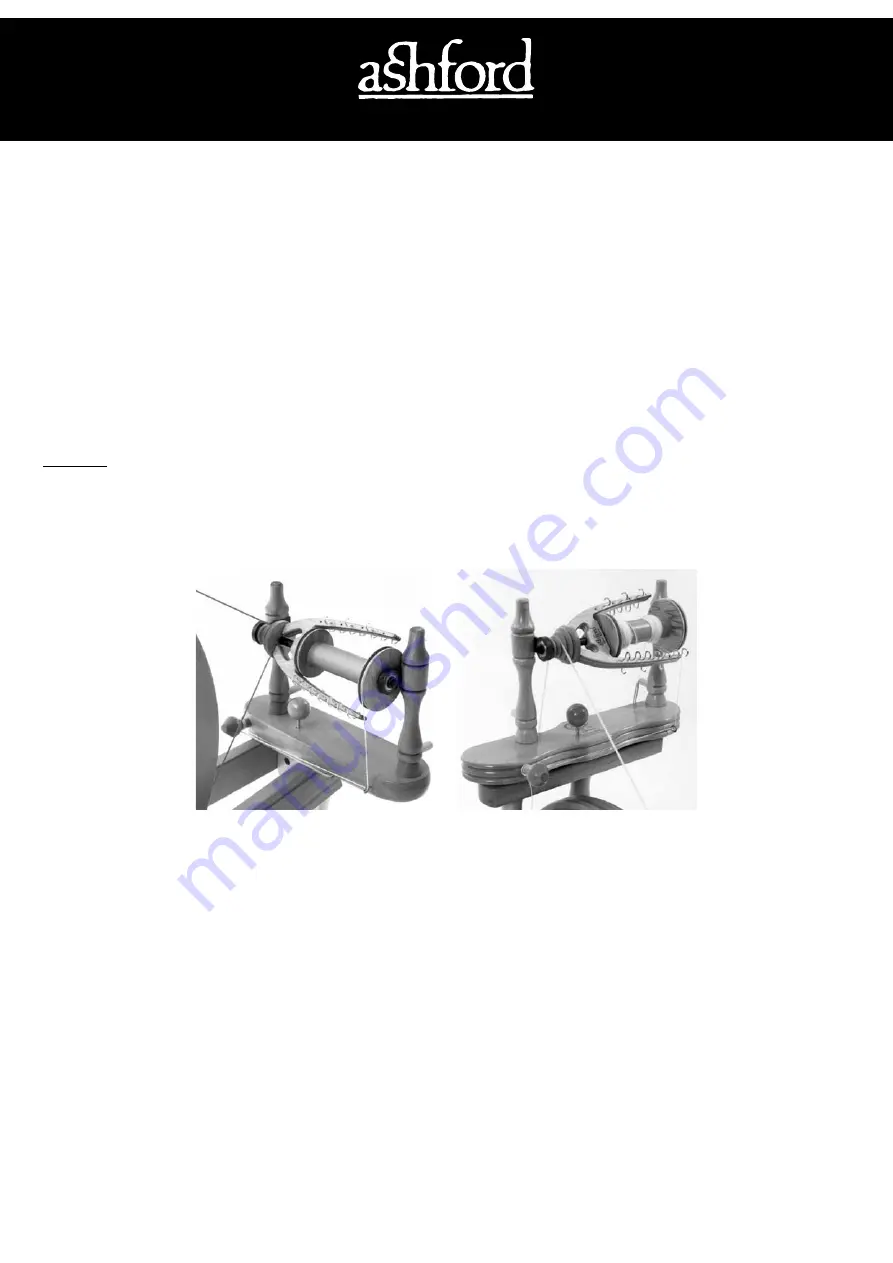
INSTRUCTIONS
LACE FLYER KIT FOR TRADITIONAL & TRAVELLER
SINGLE DRIVE SPINNING WHEELS
TOOLS REQUIRED
screwdriver, candlewax
BEFORE COMMENCING
Read the instructions carefully and indentify all parts. Note the assembly sequence.
FINISHING THE WOOD
We recommend the wood be waxed or oiled before assembly. This protects it from climatic changes and enhances it's natural beauty.
Use the sand paper supplied to smooth the flyer arms and bobbin ends to avoid your yarn catching. The groove in the large bobbin end
should also be carefully sanded to ensure the brake band provides a smooth even tension. After sanding either use a similar finish to
the rest of your spinning wheel or our natural Ashford Wax Finish.
PARTS LIST
1 Lace
Flyer 2 Fine
cotton
brake
band
3
Large Core Lace Bobbins
1
Lightweight rubber band
1
Maiden Upright with 3/8” ball bearing
2
Roundhead Screws
1
Maiden Upright with ¼” ball bearing
2
Washers
1
Polycord drive belt and fusing block
1
Threading hook and tape
1
Cotton drive belt
ASSEMBLY SEQUENCE
1. Use the screwdriver to remove the screws holding the existing maiden uprights to the maiden bar.
2. Remove the maiden uprights from the maiden bar.
3. Use the candlewax to wax the dowel ends of the new maiden uprights.
4. Insert the new maiden uprights into the maiden bar and secure with the round head screws and washers. Do not overtighten as
the maiden uprights have to be twisted to enable the bobbins to be changed.
5. Thread the flyer hooks into the pre-drilled holes in the flyer. Note the holes are drilled right through. This enables flyer hooks to be
used on both sides of the flyer. We recommend seven hooks on the orifice side and three on the opposite side but more may be
used if desired. The hooks on the opposite side enable the yarn to be wrapped back and forth to reduce the drag on the yarn as
illustrated. If the flyer is slightly out of balance, hooks may be added or removed to reduce any vibration.
6. Lubricate the flyer shaft with Ashford Spinning Oil or similar light machinery oil. Then locate a lace bobbin on the shaft. The
bobbins need to be free running and oiled regularly.
7. Twist both maiden uprights using the convenient pegs at the base. Slide the flyer and bobbin into position. Ensure the flyer
bearings are at right angles to the flyer shaft.
8. Adjust the drive belt tension knob so the maiden bar is in its lowest position.
9. Check the alignment of the drive wheel with the flyer pulley. If necessary loosen the horizontal adjustment screws, realign the
wheel and the groove in the pulley you are going to use and retighten.
10. Place the cotton drive belt around the wheel and largest pulley on the flyer. Then tie the ends with a flat or reef knot.
11. The cotton drive belt ensures the highest ratios are achieved. However if a slightly lower ratio is acceptable the alternative
polycord drive belt will result in easier treadling.
- to join the polycord drive belt place it around the wheel and largest pulley on the flyer.
- mark the polycord where it is just the right length without stretching it. Do not make it tight.
- cut off the excess polycord with a razor blade, sharp knife or scissors and save it for future repairs or adjustment.
- before joining place the cord back around the wheel.