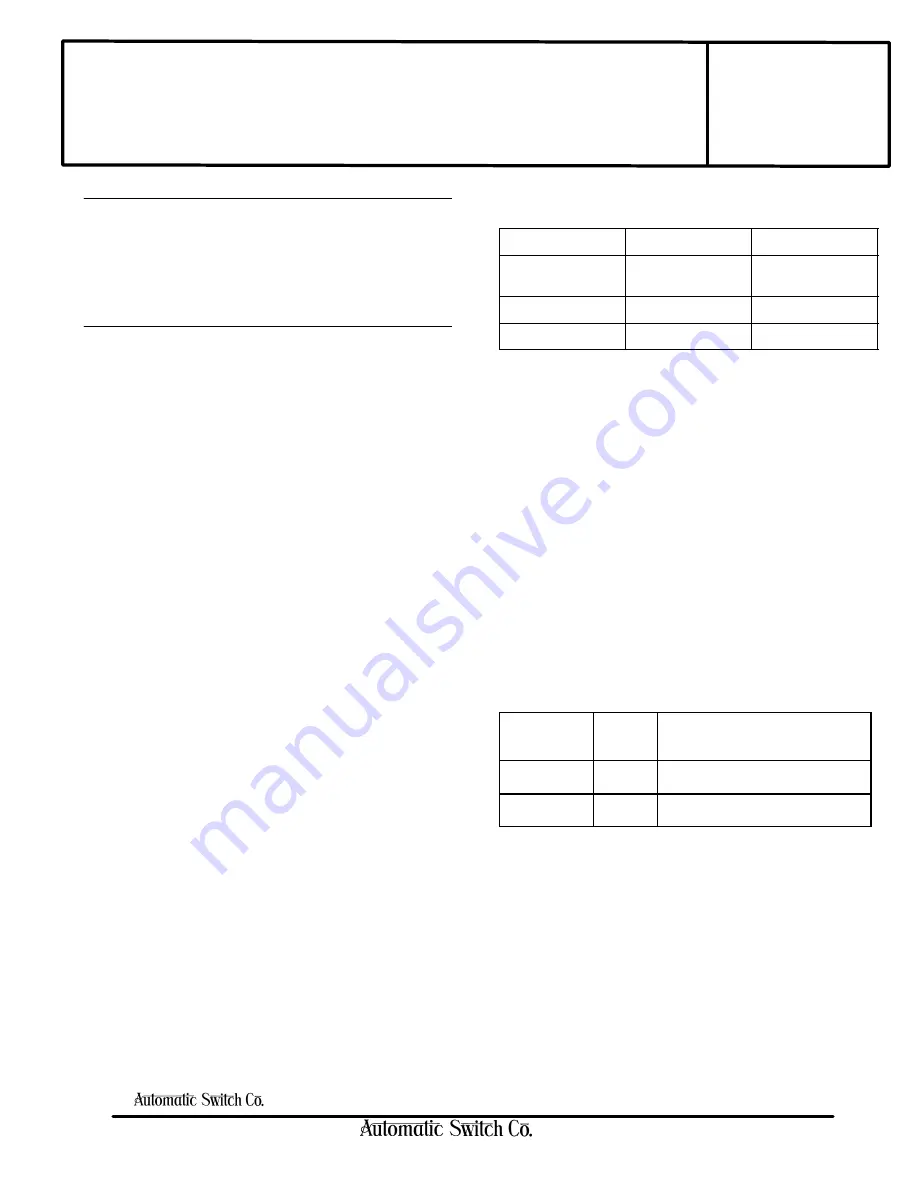
Page 1 of 8 (Section 1 of 2)
50-60 Hanover Road, Florham Park, New Jersey 07932
ASCO Valves
MCMXCVI All Rights Reserved.
Printed in U.S.A.
Installation & Maintenance Instructions
SERIES
Form No.V6371R2-Sec.1
2-WAY FREE HANDLE" MANUAL RESET SHUT-OFF VALVES
8044
WITH VISUAL POSITION INDICATOR
3/4
, 1
, 1 1/4
, 1 1/2
, 2
, 2 1/2
OR 3
NPT
(Section 1 of 2)
NORMALLY CLOSED OPERATION
NOTICE: See separate solenoid installation and
maintenance instructions for information on: Wiring,
Solenoid Temperature, Causes of Improper Operation, and
Coil Replacement.
For exploded views, see Form No. V6371 - Section 2 of 2.
DESCRIPTION
Series 8044 valves are 2-way normally closed,
free handle
manual reset shut-off valves. The
free handle
lever will not
open the valve until the solenoid is energized which allows
the lever to engage. Only then can the lever be manually
rotated to the latched position opening the valve. The valve
will trip closed (shut) instantly when the solenoid is
de-energized or when lever is rotated to the closed
position. Visual indication of
open
and
shut
positions is
accomplished by a highly visual position indicator in the side
of the operating movement. An orange indicating bar aligns
itself with the words
open
or
shut
. Standard valves are
supplied with a general purpose junction box solenoid
enclosure. The valves may also be provided with a
watertight/explosionproof solenoid enclosure.
Provisions for Pressure and Seat Leakage Testing
(See Figure 1.)
Series 8044 valves are provided with four 1/8
āNPT tapped
and plugged holes, two on either side of valve body. Two
upstream for pressure testing; two downstream for seat
leakage testing. Leakage testing frequency shall be at least
annually in accordance with NFPA-86 or original
equipment manufacturer recommendations. Testing is also
required after valve disassembly and reassembly for
inspection, cleaning or rebuilding.
OPERATION
The valve can be manually set to the open position only
when the solenoid is energized. When the solenoid is
de-energized, the valve will close and cannot be opened or
held open manually until electrical power is restored to the
solenoid.
To Open
: Energize the solenoid, rotate lever to closed
position and rotate back to open position.
To Close
: De-energize solenoid or rotate lever to close
position.
Operating Pressure Differential (psi)
Pipe Size
Minimum
Maximum
3/4
, 1
, 1 1/4
and 1 1/2
0
25 psi
2
0
20 psi
2 1/2
and 3
0
10 psi
INSTALLATION
Check nameplate for correct catalog number, pressure,
voltage, frequency, and service. Never apply incompatible
fluids or exceed pressure rating of the valve. Installation and
valve maintenance to be performed by qualified personnel.
Future Service Considerations
Provision should be made for performing seat leakage,
external leakage, and operational tests on the valve with a
nonhazardous, noncombustible fluid after disassembly and
reassembly.
Temperature Limitations
For maximum valve ambient and fluid temperatures, refer
to chart below. Check wattage rating on nameplate to
determine temperature.
Watt
Rating
Coil
Class
Ambient and Fluid
Temperature
20
F
-20
F (31
C) to + 125
F (52
C)
36.2
H
-20
F (31
C) to + 77
F (25
C)
Positioning
Valve must be mounted with operator assembly vertical and
upright.
Piping
Connect piping to valve according to markings on valve
body. Apply pipe compound sparingly to male pipe threads
only. If applied to valve threads the compound may enter
the valve and cause operational difficulty. Avoid pipe strain
by properly supporting and aligning piping.