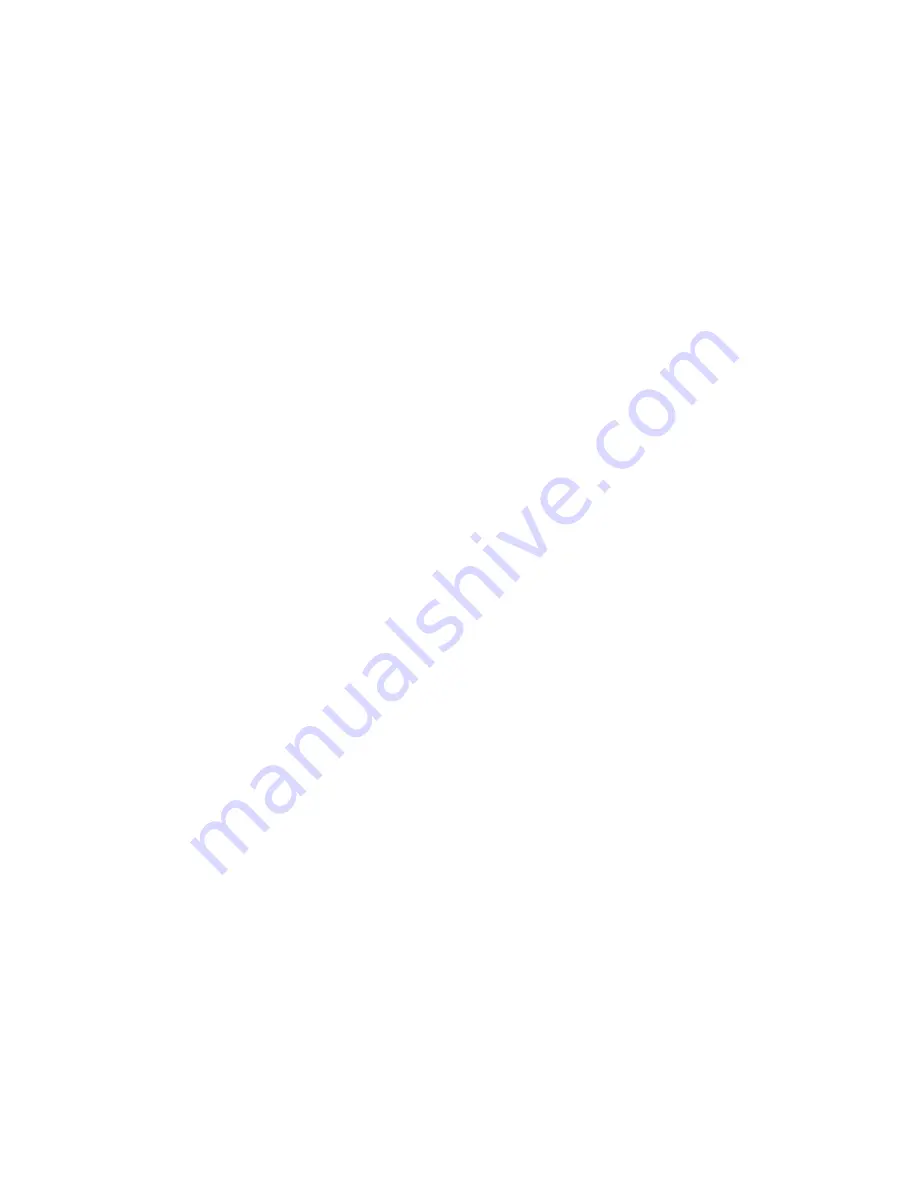
F
OR
M
ODELS
: JGI, JGM, JGN, JGP
AND
JGQ
S
ECTION
5 - M
AINTENANCE
PAGE 5-14
10. Be sure all tools are removed and install the cylinder head (or unloader) and
tighten fasteners to Table 1-12 on page 1-16.
11.
With the cylinder head or unloader (closed position) properly installed, rotate the
crankshaft to the exact outer dead center position of the throw.
NOTE: UTILIZE A DIAL INDICATOR WITH A MAGNETIC BASE TO INDICATE THE
LOCATION OF THE CROSSHEAD WHEN FINDING EXACT OUTER DEAD CEN-
TER POSITION.
12. Remove a top head end valve.
13. Determine the required piston head end clearance limits from the cylinder identi-
fication plate, refer to Figure 1-4 on page 1-6. Measure head end clearance at
the top of the head end. Using feeler gages through the open valve pocket,
check the head end clearance. Determine that the measured clearance is within
the required clearance limits. If clearance is out of limits, contact your packager
or Ariel.
14. Remove dial indicator and base.
15. Tighten the set screws in the crosshead-balance nut.
16. Install the valve assemblies and properly tighten fasteners, refer to “Valves -
Reassembly” on page 5-41 and “Bolt Tightening for Valve Caps” on page 5-42.
17. Check piston rod run out and crosshead clearances upon re-assembly, any time
a piston rod is removed, see “Piston Rod Run Out” on page 5-31, and Table 1-3
on page 1-10 for crosshead clearances and checking procedure. If clearances
are out of limits, contact your packager or Ariel.
18. Replace the crosshead guide side covers and gaskets, tighten all cover cap
screws hand wrench tight. Before installing a gasket, apply an antiseize lubri-
cant to both sides or to the metal seating surfaces. This will help to hold the gas-
ket in place during assembly and aid in easy of removal.
Crankshaft
Main Bearings - Checking Clearances
1.
Do not remove main bearing caps to check for bearing wear, if a cap is removed
it is recommended that a new bearing be installed, i.e.
DO NOT REUSE BEAR-
ING SHELLS.
2.
Determine main bearing wear by checking actual journal bearing vertical jack, at
each bearing, and crankshaft thrust clearances against the clearance limits
given in Table 1-3 on page 1-10, and last new bearing clearance values if avail-
able. High copper content in the oil analysis may be an indication of bearing
wear. Use calibrated dial indicators with 0.0005 inch (0.005 mm) increments and
magnetic stands to check clearances. Measure main bearing vertical jack clear-
ances:
a. As shown in Figure 5-10 on Page 5-15, turn an adjacent throw up to the high-
est position.
b. Place lifting strap completely around the crankshaft at the adjacent web and
attach strap to a crane or a long pry bar.
c. Install a magnetic stand on the top of the main bearing cap, with a needle
type dial indicator placed against the top of the crankshaft web of the adja-