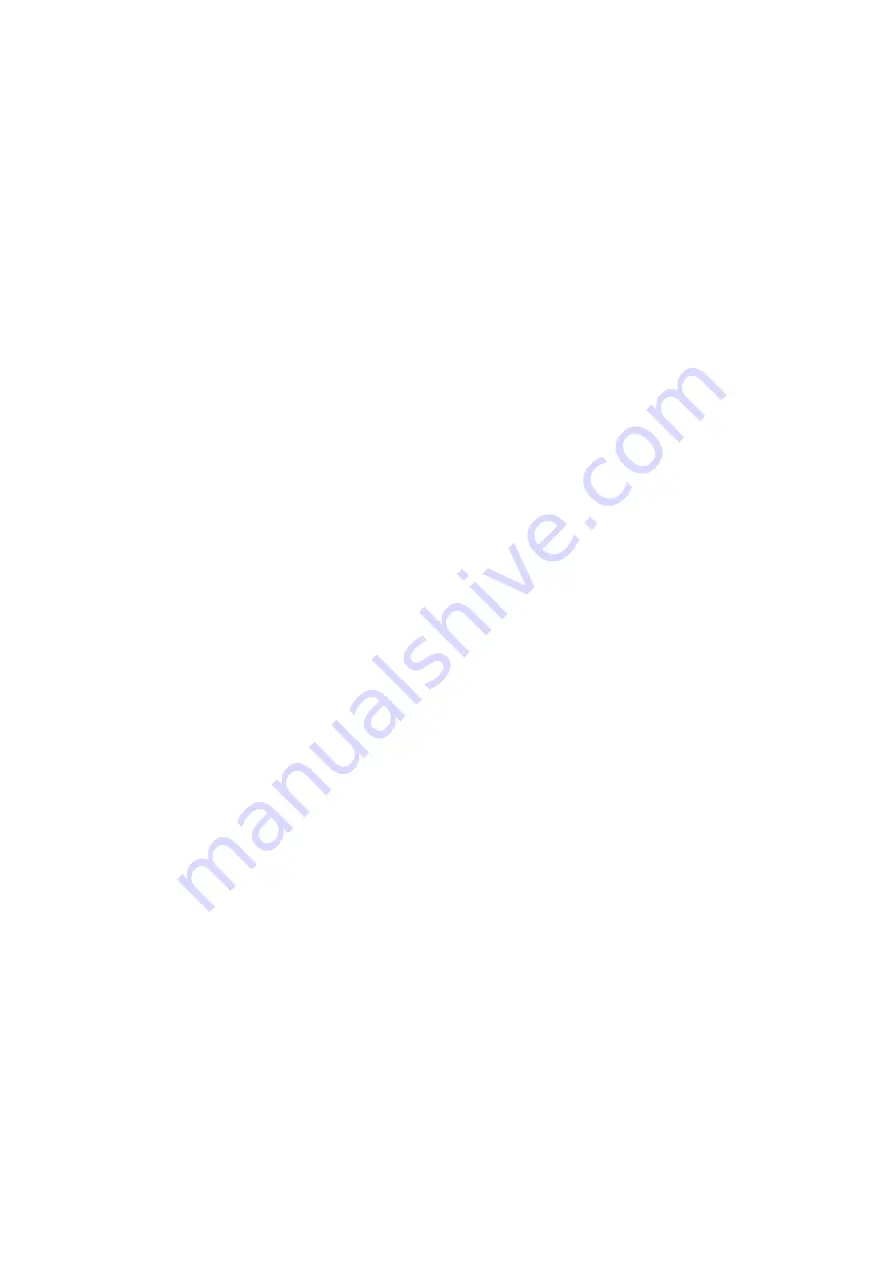
6
Star/Delta starting is used when the motor power is above 7.5 kW (10 HP ) only in case of frequent starts and short running
times, but always when the motor power is above 15kW (20 HP ). All this is also to safeguard the structure of the pump.
Protection level
The initials IP are followed by two numbers :
The first number indicates the level of protection against penetration of solid objects and in particular :
4 for solids whose dimension is greater than 1mm
5 for dust (eventual internal deposits will not harm operation)
6 for dust (no pentetration)
The second number indicates the protection against the penetration of liquids. In particular:
4 for water sprays from all directions
5 for jets of water from all directions
6 for tidal and sea waves.
According to the IP protection indicated on the identification plate of the motor and to the environmental conditions, arrange for
opportune extra protections allowing in any case correct ventilation and rapid drainage of rainwater.
6
PRESSURE SWITCH TO PREVENT DRY RUNNING
The principal cause of pump malfunctions is dry-running (being it caused by improper use or cavitation ). It is therefore
advisable to install a simple device that will stop the pump motor when the pressure falls below a preset level. This is just ified
by the fact that such a condition is normally caused to an inadequate flooding of the impeller due to various causes: absence of
liquid, suction valves closed at start-up, cavitation, clogged channels, dirty filters, etc.....
The pressure switch (pressure gauge with electrical contacts) must be fitted on the discharge side of the pump at approximately
20cm from the outlet. This device needs furthermore:
1) ) A fluid separator to transmit pressure to the instrument via a secondary fluid separated from the main one by a chemically
resistant diaphragm.
2) Remote-control switch to energize the motor (controlled by a pushbutton or auxiliary relay) having the normally closed
contact of the pressure switch in series with the latch circuit of said remote-control switch.
In order to obviate any pulsations of the pressure switch, it is necessary to set its setpoint to a pressure value equal to 65% of
the working pressure. It is obvious that this device cannot be used to control working pressure.
On start-up the pressure switch contact must be by-passed for a sufficient time to allow pressure to build up in the system. In
case of automatic start-up it is necessary to short circuit the latch with a timer for the pressure build-up time.
The system is not suitable for full capacity applications in which case it is advisable to install some control devices for the motor
power absorbtion.
All of the above must be adapted to the local safety rules and in particular when the classification of the environment requires
explosion-proof equipment.
7
INSTRUCTION ON INSTALLATION AND USE
7.1
TRANSPORT
- cover the hydraulic connections
- when lifting the unit do not exert force on the plastic fittings
- lay the pump on its base or fixing plate during transport
- if the road is particularly rough, protect the pump by means of adequate shock absorbing supports
- bumps and shocks may damage important working parts vital for safety and functionality of the machine
7.2
INSTALLATION
-
check that bolts and nuts are correctly screwed (cfr. 9.3 pag. 12 “Assembly” for the right bolts torque setting), thermoplastics
are dimensionally sensitive to sizeable temperature changes.
-
clean the plant before connecting the pump
-
make sure that no foreign bodies are left in the pump. Remove safety caps on the hydraulic connections.
-
follow the instructions indicated in the following diagram:
1)
Suction head varies according to flow in order to prevent windage (min. 0.5 m, max. 15% of pump head)
2)
YES: expansion joint (indispensable with long pipes or hot liquids) and/or anti-vibration facility during discharge and
suction; anchored near to pump
3)
YES: attachment for gauge or safety pressure switch
4)
YES: check value (especially for long vertical or horizontal pipes; compulsory with parallel pumps).
5)
YES: adjusting gate valve on outlet
6)
speed of delivered fluid: 3.,5 m/s max. .
7)
NO: elbow joints (and other parts) on the pump (discharge and suction lines)
8)
YES: drainage channel around base
Содержание ZMR 02.30
Страница 2: ...2 1 DISASSEMBLING SEQUENCE ...
Страница 16: ...16 ...
Страница 17: ...17 ...
Страница 18: ...18 ...
Страница 19: ...19 ...