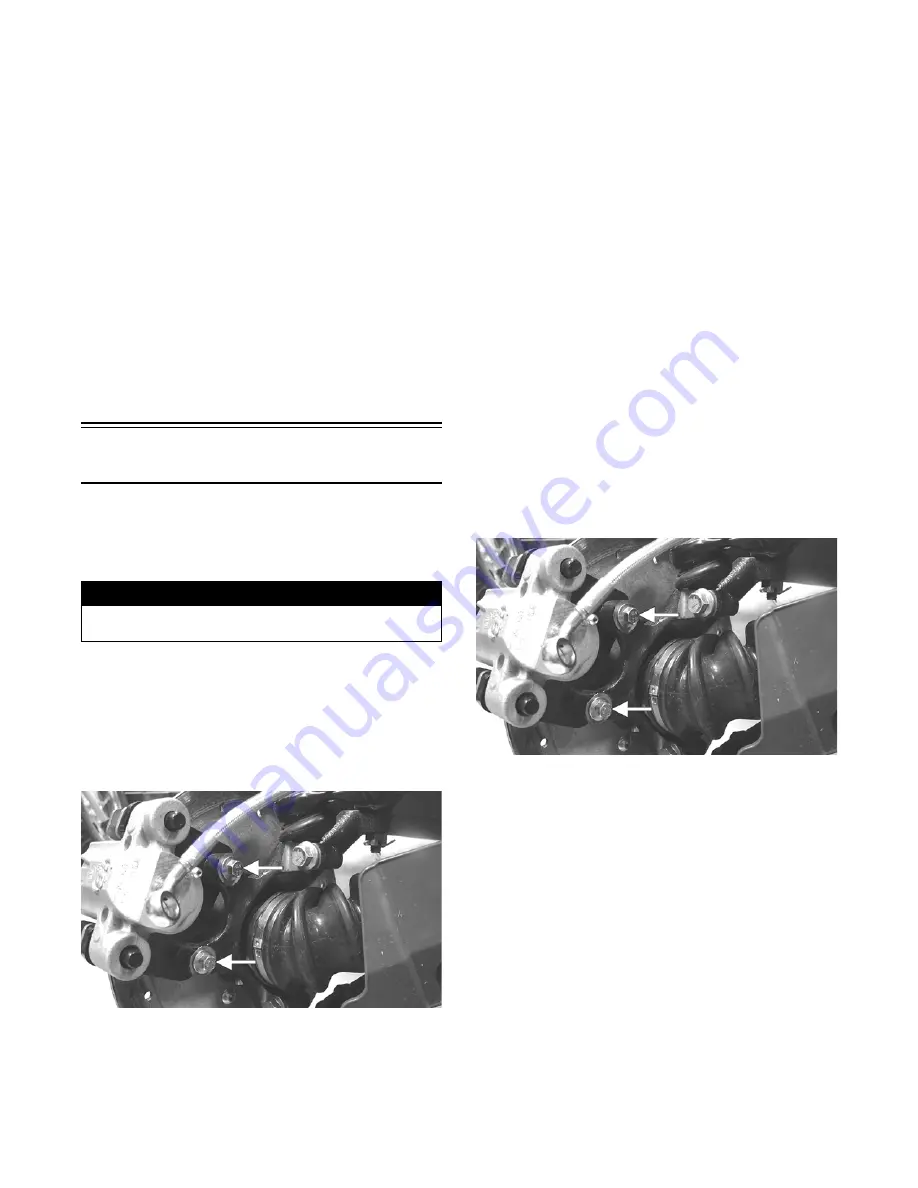
6-20
3. If clearance is as specified, remove the ring gear and
thrust button; then place a drop of red Loctite #271
on the threads and tighten to 8 ft-lb (left-hand
threads).
4. If clearance is not as specified, repeat steps 1 and 2
using thicker (clearance too great) or thinner (clear-
ance too small) until correct specification is reached.
INSTALLING
1. Slide the gear case into position through the left side
of the frame; then secure it to the frame with cap
screws and lock nuts. Tighten to 38 ft-lb.
2. Secure the engine output shaft to the rear gear case
input flange with four cap screws and lock nuts.
Tighten to 20 ft-lb.
3. Install the rear drive axles (see Drive Axles in this
section).
4. Install the left-side rear A-arms (see Rear A-Arms in
Section 7).
Hub
REMOVING
1. Secure the ATV on a support stand to elevate the
wheel; then remove the wheel.
2. Remove the cotter pin from the nut.
NOTE: During assembly, new cotter pins should be
installed.
3. Remove the flange nut securing the hub.
4. Remove the brake caliper.
PR243A
5. Remove the hub assembly.
6. Remove the four cap screws securing the brake disc.
CLEANING AND INSPECTING
NOTE: Whenever a part is worn excessively,
cracked, or damaged in any way, replacement is nec-
essary.
1. Clean all hub components.
2. Inspect all threads for stripping or damage.
3. Inspect the brake disc for cracks or warping.
4. Inspect the hub for pits, cracks, loose studs, or spline
wear.
INSTALLING
1. Secure the brake disc to the hub with the four cap
screws coated with blue Loctite #243. Tighten to 15
ft-lb.
2. Apply grease to the splines in the hub.
3. Install the hub assembly onto the shaft.
4. Secure the hub assembly with the nut. Tighten only
until snug.
5. Secure the brake caliper to the knuckle with two new
“patch-lock” cap screws. Tighten the auxiliary cali-
per to 20 ft-lb. Tighten the hydraulic caliper to 20
ft-lb.
PR243A
6. Tighten the hub nut (from step 4) to 200 ft-lb; then
install and spread a new cotter pin making sure each
side of the pin is flush to the hub nut.
NOTE: If the cotter pin does not line up, always
tighten to the next alignment.
7. Install the wheel and tighten to 40 ft-lb.
8. Remove the ATV from the support stand.
! WARNING
Make sure the ATV is solidly supported on the support
stand to avoid injury.
For Discount Arctic Cat Parts Call 606-678-9623 or 606-561-4983
www.mymowerparts.com