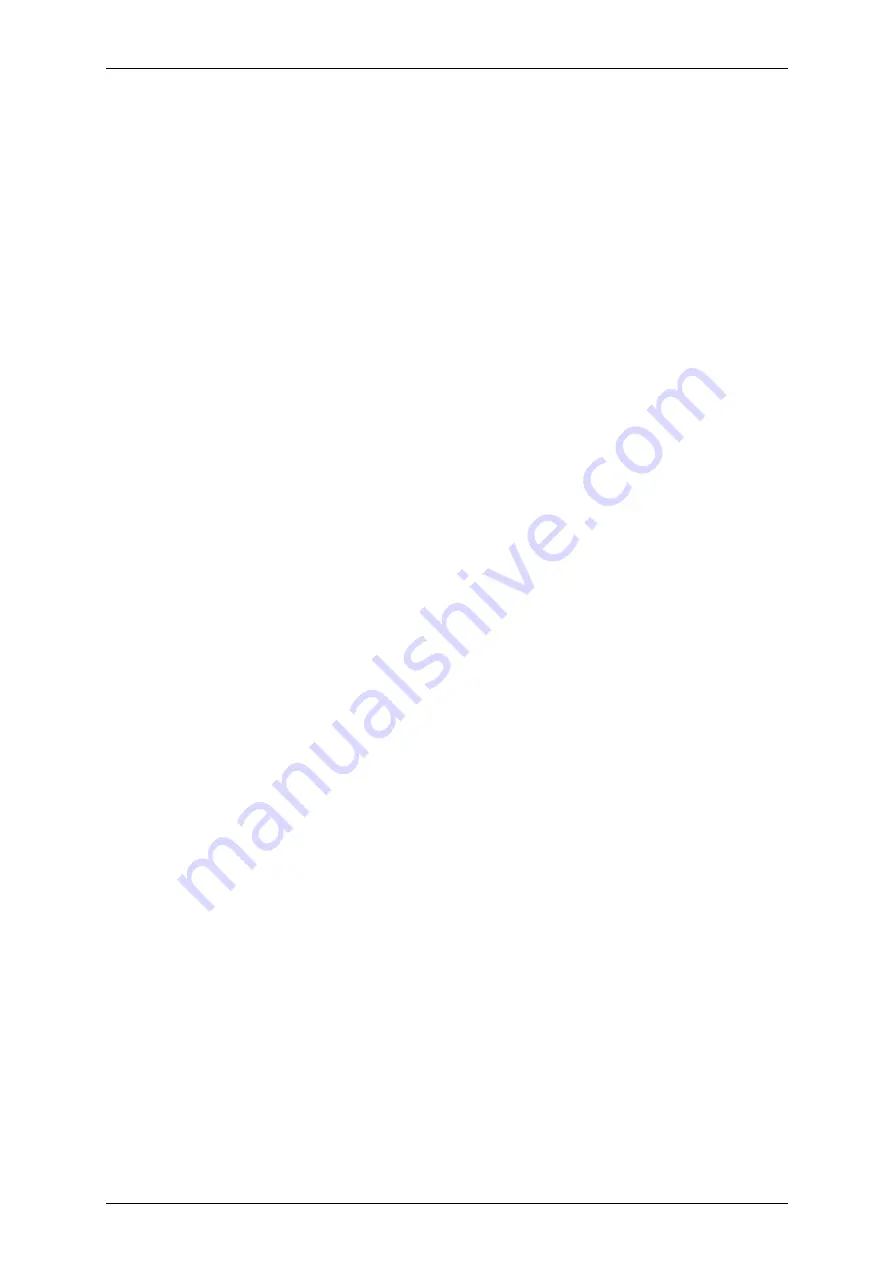
AMD5x Passive Infeed Unit and AMD5x Servo Drive - User Guide
ANCA MOTION
D-000129 Rev 09
70
Motor Signal Cable Shielding
5.6.6
The motor encoder signal cable must use drive and motor connectors where the shield is terminated to the
connector housing. The encoder signal cable should not use a shield clamp.
Earth Bond Strap
5.6.7
Any installation which mounts the AMD5x system on a painted gear tray should use braided earth bond straps
from each Drive and PIU metal chassis to the gear tray or nearby common shield clamp DIN rail / Bus Bar. If the
earth bond strap is connected to the gear tray, then paint must be removed under the whole connection point. A
short, wide braided strap provides low impedance for common mode noise currents, and cannot be replaced with
PE wires. The braid should be copper or tin plated copper, and have a cross sectional area of 6mm
2
or greater.
Cable Routing
5.6.8
In a drive system the return common mode currents flow through shields, cabinets, gear tray and earth wiring to
create localized parasitic ground potentials, which may affect control signals using the ground as a common
voltage reference. Careful planning of cable routing and location of shield grounds must be done to minimise
influence of parasitic ground potentials, and ensure compliance with EMC requirements. The following guidelines
must be followed.
Physically separate “noisy” and “clean” cables at the planning stage. Pay special attention to the
motor cable.
All cable routing in an enclosure should be as mounted close as possible to a gear tray or grounded
cabinet walls; “free-floating cables” act as both active and passive antennae.
Use twisted pair wires for analogue and control level wherever possible to prevent interference from
radiated common mode noise sources. Continue the twist as close as possible to terminals, and for
wires exiting from the overall enclosure.
Keep power and control wiring separate. Crossing at right angles is permitted, but no significant
parallel runs should be allowed, and cables should not share cable trays, trunking or conduits
unless they are separately shielded and the shields correctly terminated
Avoid mixing pairs with different signal types. Do not mix 415 V AC with 24 Vdc, analogue, digital.
If plastic trunking/ducting is used, secure it directly to installation plates or the framework. Do not
allow spans over free air which could form an antenna.
Keep shield pigtails as short as possible and note they are less effective than full clamping
Allow no breaks in the cable shields.
Cabinet Earth connections should be as short as possible using flat strip, multi-stranded or braided
flexible conductors for low RFI impedance.
Avoid coiling excess lengths of Motor Armature cables (particularly with Hiperface DSL Motors).
Ensure that all Hiperface DSL Motor cables are separated from each other where feasible.
Hiperface DSL Segment Shield Clamping
5.6.9
The ANCA Motion Hiperface DSL Motor Cable Assembly range is designed to be used with an AMD5x Drive
fitted with HDLS Encoder support and an ANCA Motion Motor fitted with a Hiperface DSL Encoder.
The Cable Assembly is supplied with wire designator labels. The Cable Assembly range includes variants with an
optional Brake Segment and variants to suit termination to the full AMD5x Drive range (3/6/12/20 A, 35 A).
Two exposed shielded braid areas on the Hiperface DSL Cable Assembly support the separate clamping of the
Outer Shield and Hiperface DSL Segment Shield at the Drive Gear Tray, adjacent to the top face of the Drive.
Both shields carry significant RF Noise Current and both shields must be terminated to an effective RF Ground,
which is normally formed by the Equipment Cabinet Gear Tray (refer to
11.8.9 Motor Power Cable Shield Clamps
for details of the recommended Hiperface DSL Segment EMC Shield Clamp).
All AMD5x Drives use the same EMC Clamp for the Outer Shield (ICN-3049-0522) and the same EMC Clamp for
the Hiperface DSL Segment Shield (ICN-3049-0523).
Local strain relief for the motor power cable should be fitted immediately after the cable is inserted into the EMC
Clamps.