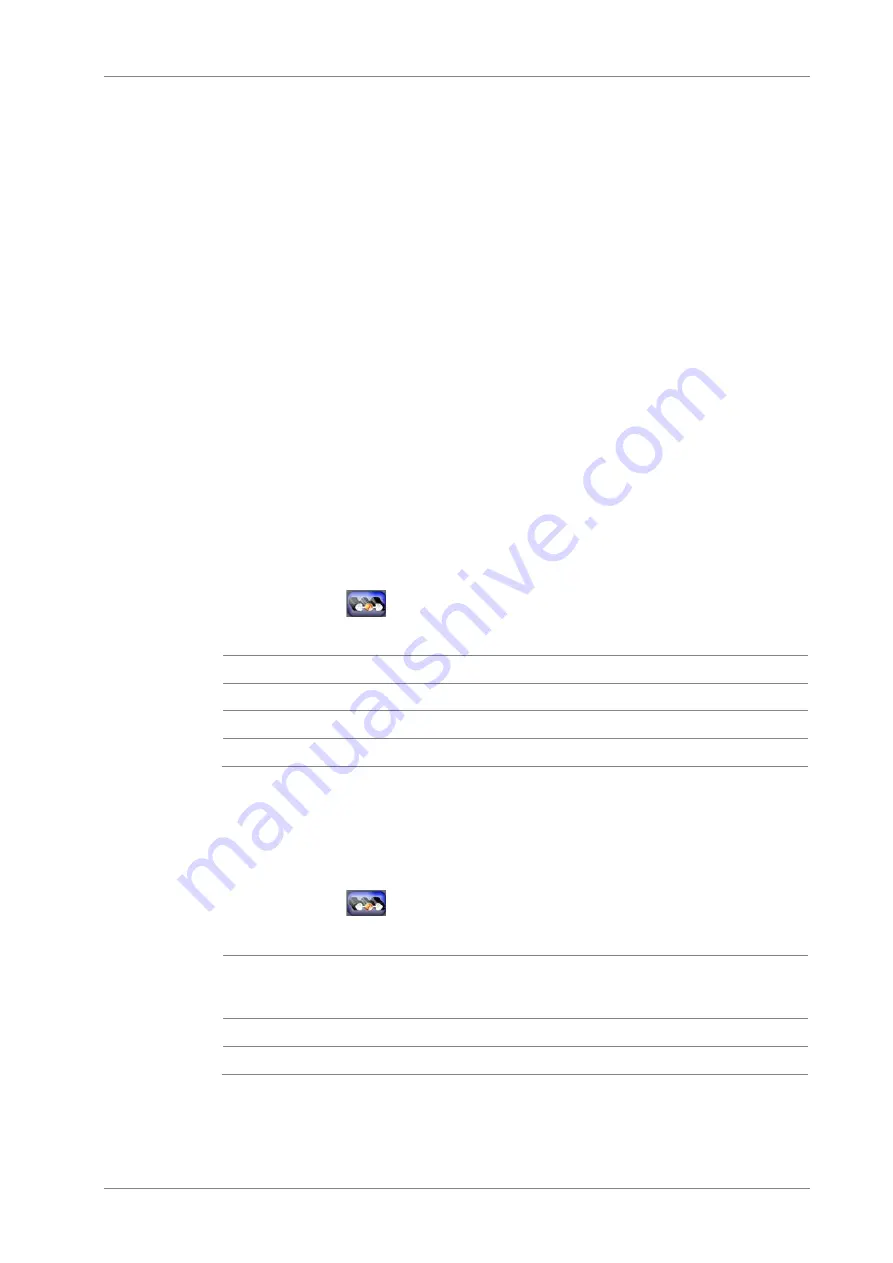
Installation and start-up
contrAA 600
Edition 01/2014
43
6.4.4
Formatting the graphite tube
When the graphite tube is formatted the following takes place
Atmospheric oxygen is expelled from the oven and the force on the movable furnace
part is adjusted
The tube temperature is recalibrated
A new installed graphite tube is formatted
The furnace is cleaned after pausing
The furnace must be formatted after the following:
Switching on the spectrometer
Closing the previously opened furnace
The complete formatting program contains nine pre-programmed temperature stages.
Formatting is started in the
Furnace / Control
window. During formatting, the current tem-
perature stage, time and ramp are displayed in the
Format tube
window. In the first five
stages, the furnace and the graphite tube are cleaned and conditioned (contacts between
the graphite tube and the electrodes are aligned). By means of a special sensor technique,
the tube temperature in the remaining four stages is measured. The corrected furnace tem-
perature ensures correct measurement results.
At a formatting factor of
≥
+10
%
an automatic temperature correction no longer takes place,
but the current furnace program can still be started after confirming the corresponding
screen message.
1.
In ASpect CS use
to switch to the
Furnace
/
Control
window.
2.
Enter specific data on the current graphite tube:
New graphite tube
Heat cycles
0
Lifetime
0
Used graphite tube
Heat cycles
Current value of the graphite tube
Lifetime
Current value of the graphite tube
3.
In the
Format tube
area click the
[Formation]
button.
6.4.5
Cleaning the graphite tube / cleanout
1.
In ASpect CS use
to open the
Furnace
/ Control
window.
2.
In the
Clean out
area set the following parameters:
Temp. [°C]
Final temperature to be reached during clean out.
The final temperature should be approx. 50 °C higher than the
previous atomization temperature.
Ramp [°C/s]
Heating rate
Hold [s]
Set the hold time
3.
Start the cleanout with the
[Start]
button in the furnace area. Cleaning may be repeated
several times, if required at a higher temperature.